Category Archives: Grinding Machine
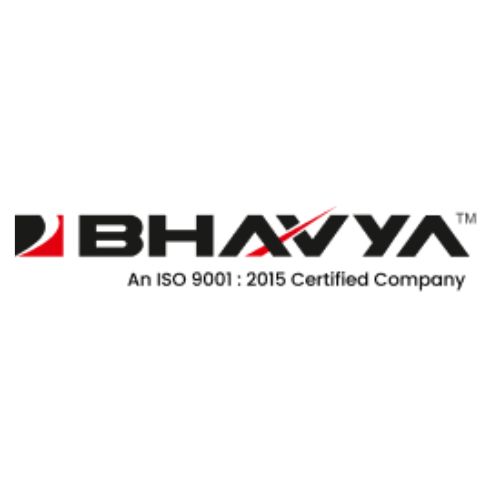
Surface Grinding Machines: Precision and Efficiency in Machining
Introduction Surface grinding machines are indispensable tools used for achieving precise and smooth surfaces. With the ability to remove any surface irregularities, they play a vital role in various industries, including automotive, aerospace, metalworking, and construction. The surface grinder works…
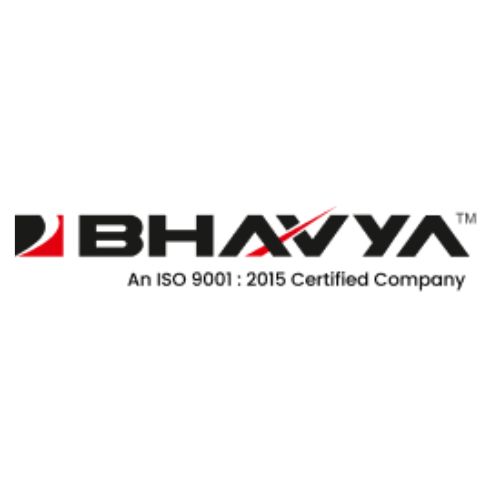
Universal Tool and Cutter Grinding Machine
The Universal Tool and Cutter Grinding Machine is a specialized piece of equipment designed for precision grinding and sharpening of cutting tools. It offers a wide range of capabilities, allowing manufacturers to produce tools with exceptional accuracy and consistency. This…
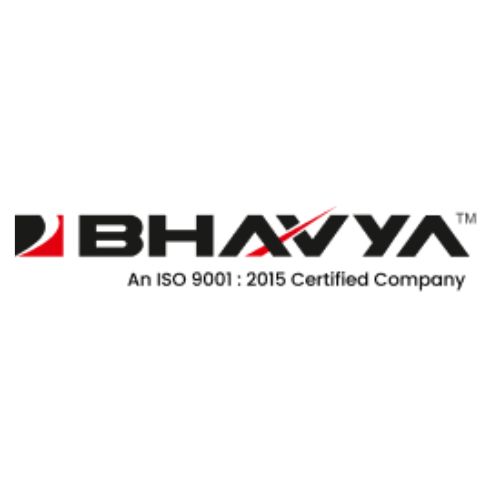
Tool & Cutter Grinding Machine Features, Applications and Benefits
What is Tool & Cutter Grinding Machine A Tool and Cutter Grinding Machine is a type of machine used to manufacture, sharpen, and repair various cutting tools such as milling cutters, drills, reamers, and other types of tools used in…
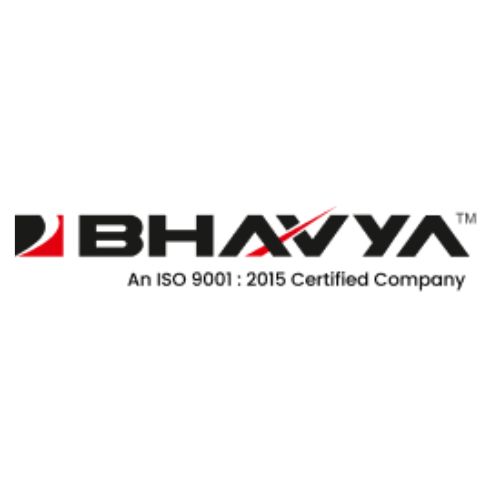
The Surface Grinding Machine Market in Bahrain
Currently, the surface grinding machine market in Bahrain is experiencing a high level of growth due to the increase in demand for grinding machines in the automotive industry. This is because automotive manufacturers are looking to improve production processes and…
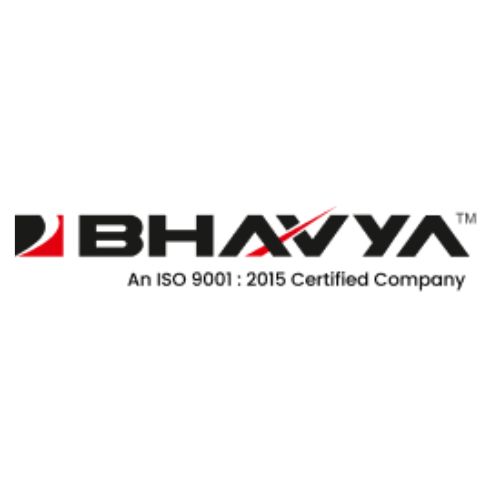
Surface Grinding Machine Demand and Supply in Oman Market
Considering the growing demand for surface grinding machines in the Oman market, the companies are offering a wide range of machines that can cater to the need of various industries. These machines include CNC grinding machines, which have a major…
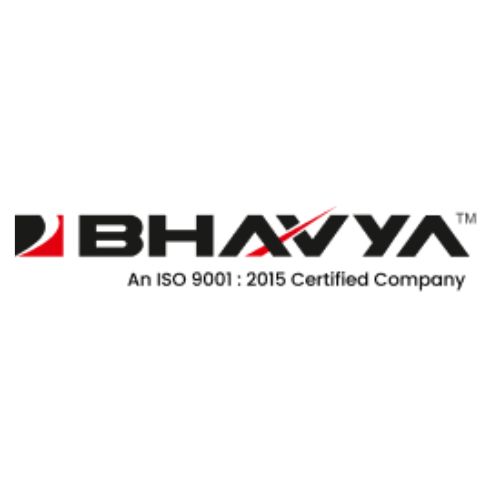
Surface Grinding Machine Demand and Supply in Qatar
Various industries in Qatar are in need of surface grinding machines. They need them to manufacture parts that are more accurate and precise. These machines are used in several industries, such as construction, automotive, manufacturing and engineering. Which Surface Grinding…
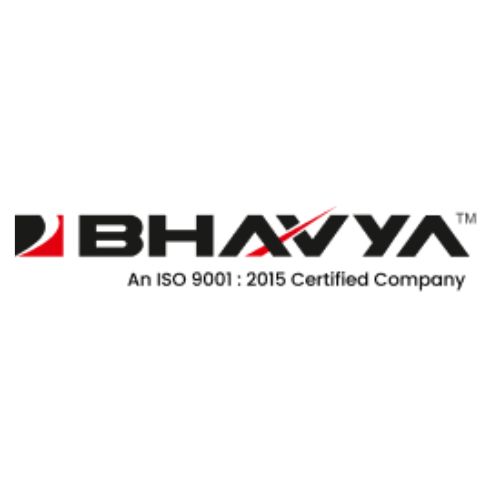
Surface Grinding Machine Market in Kuwait
Currently, the market for Surface Grinding Machine in Kuwait is undergoing rapid growth as non-residential buildings and other construction projects are booming in the country. This is because the demand for the surface grinders is rising owing to the increasing…
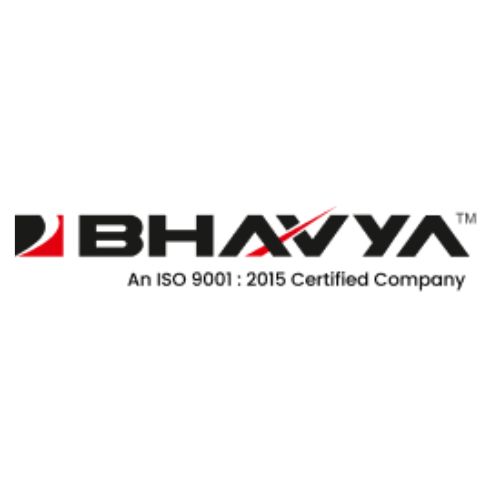
Know More about Hydraulic Cylindrical Grinding Machine
Hydraulic cylindrical grinding machine is the modern version of a mechanical Cylinder Head. These Cylinder heads are made up of plastic material and can be found in numerous types. They can be divided into two basic categories. The first category…
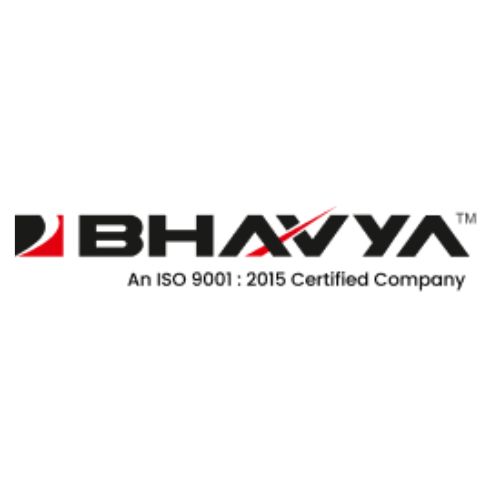
Pros and Cons of Welding and Drilling Machine Carts
A surface grinder is an excellent tool for diminishing hardened bent shafting on a metal surface. The material used for surface grinding, which is generally 0.25 - 0.5 mm, is well suited for rough cutting. However, the surface grinder can…
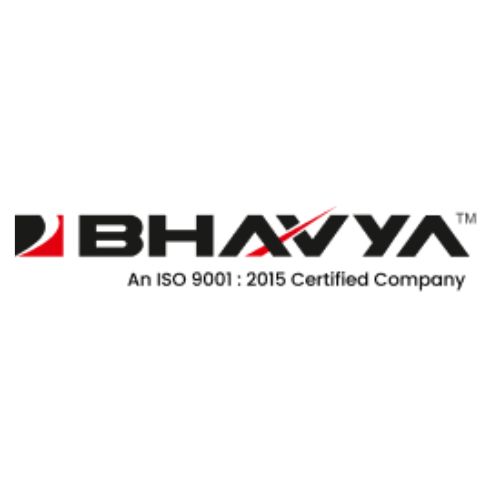
How to Manage Milling in Depth?
Growing Milling Requirements Mill is one of the priority equipments for metal industries and fabrication jobs. It helps it getting the toughest metal components ready to be composed for final produce. It is one of the main devices that prepare…
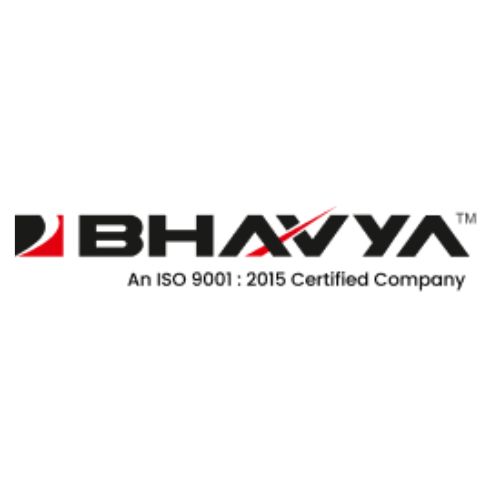
Learn about the Multipurpose Machining Advantages with Grinding Equipment
As far as the concept of grinding in machining industry is concerned, it refers to the milling device. It is applied to design wood, metal and many solid work piece materials. In most of the industries milling machines are identified…
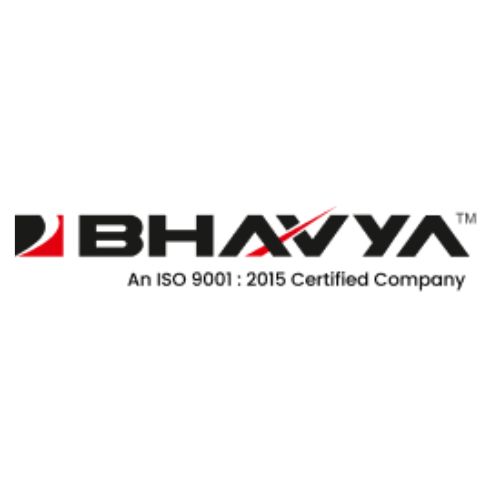
How Grinding Equipment Helps for Rapid Metal Chip Removal Application and for Obtaining Precise Surface Quality?
The Need for Smooth Finish in Metal Work Piece Metal sheets with fine surface finish remain one of the important pre-requisites in many industries. However, obtaining a smooth and precise surface appearance on a metal surface is not easily done…
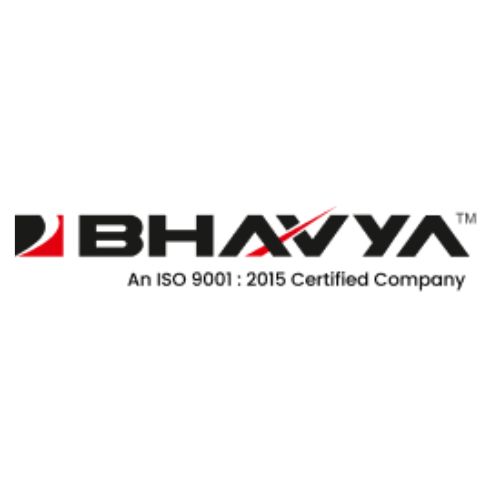
5 Most Important Machine Tools For Any Workshop [INFOGRAPH]
Nowadays, several types of workshop machine tools are manufactured in many countries around the globe. These tools are commonly used for different purposes in a wide range of industrial segments such as woodworking, automobile, electrical, construction, etc. This infograph give…
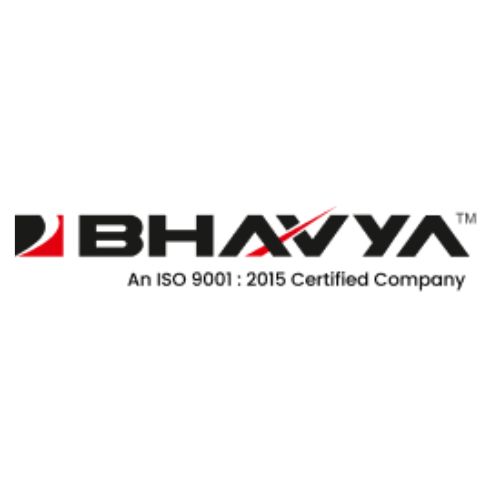
Facts About a Surface Grinding Machine
To give a meticulous smooth finish to the surface, as regards the level, size or finish of the surface of a flat metallic or non-metallic object, surface grinding tools are used. In order to make the surface flat and smooth…
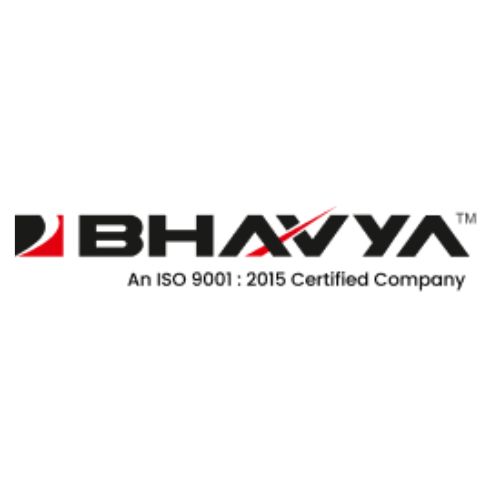
Popular Types of Woodworking Machinery Used in Workshops and Industries
Machines employed in a wood processing operation to cast the desired shape or dimensions from the wood work piece are known as woodworking machine. It may be manual operated or computer controlled machinery. Manual machines are good for the small…
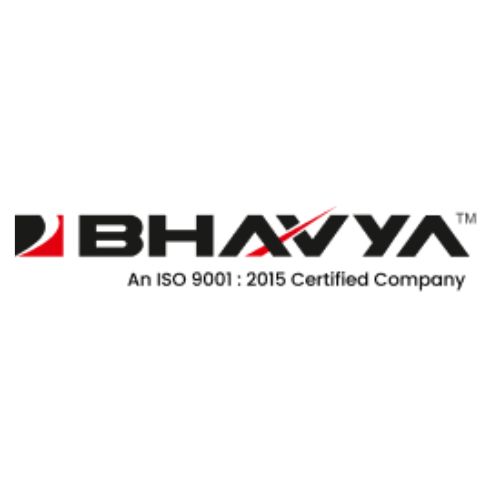
Types of Workshop Machinery – Milling, Grinding, Shaping Machines
Types of Workshop Machinery – Milling, Grinding, Shaping Machines Machine play a very important role in a workshop where metal working or woodworking tasks are performed. They enable speed process in the workshops and enhance the accuracy and efficiency of…
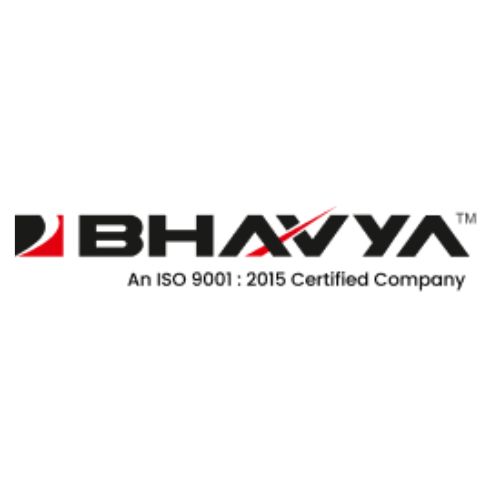
How to Use a Grinding Machine Safely?
The grinding machine is utilized in a tool shop for various purposes such as finishing, forming, sharpening, cutting, roughing, snagging, cleaning, polishing, buffing, etc. However, while operating a grinding device, it may cause serious injuries to the operator or any…
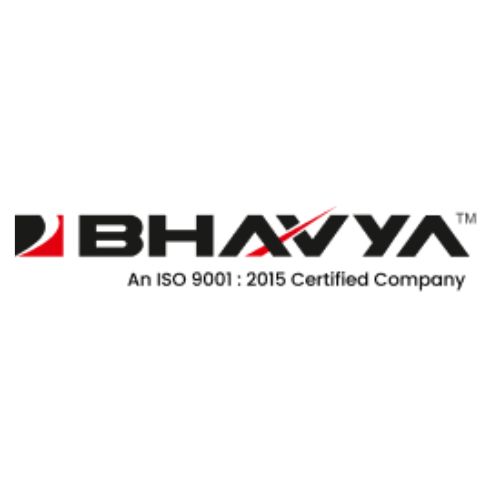
How to Select a Superior Quality and Durable Grinding Machine?
These days, several types of machines are manufactured in order to automate a number of different industrial processes. This also includes a wide range of grinding tools or grinders. They are available in numerous dimensions and a variety of diverse…
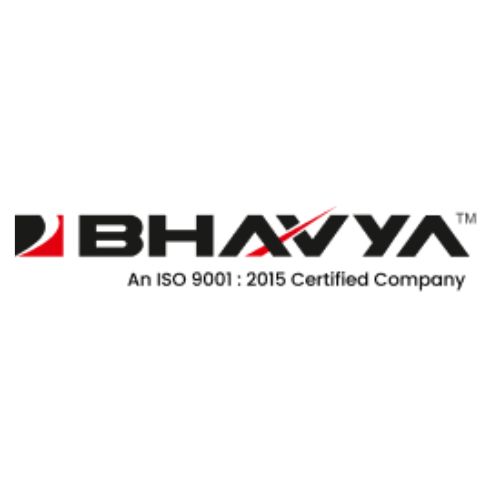
Types of Workshop Machinery Which can Enhance Efficiency and Productivity
These days, a variety of workshop machines are readily available in the market. Following are the different types which can enhance efficiency and productivity. A shaping machine is an exceptional workshop unit that is generally applied to shape flat or straight metals…
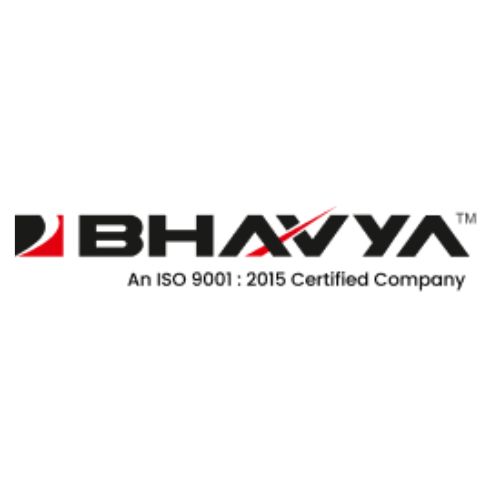
Types and Uses of a Grinding Machine
The grinding machine is a type of tool that is utilized for grinding work pieces. It basically use an abrasive wheel as the cutting tool. The rough surface of the abrasive wheel shreds off small portions of the work piece…
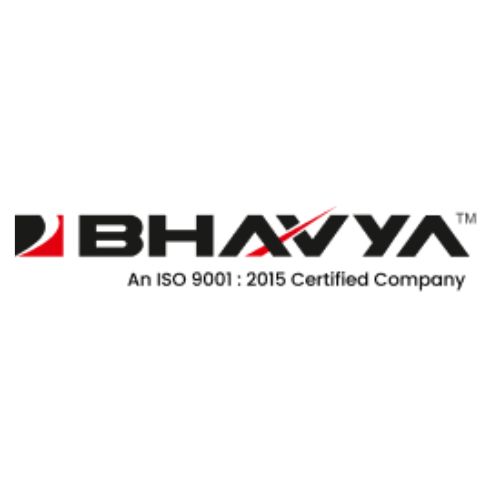
A Brief Description About Useful Tool Room Machines
A tool room basically refers to a room in an industrial unit where special machinery is used, in order to manufacture or repair the various tools and components that are necessary to produce the final product. A tool room also…
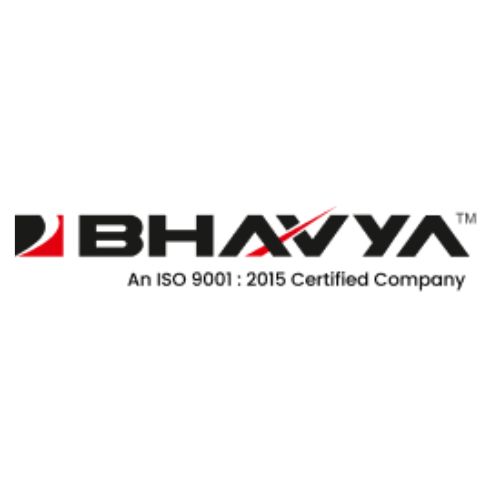
Exclusive Range of Machine Tools from Bhavya Machine Tools
We present variety of tools used in various standard and critical industrial applications. Some of the widely used industrial equipments are lathe, drill, tool room, sheet metal, shearing, press brakes, SPM & heavy, wood working and automobile unit. We are…
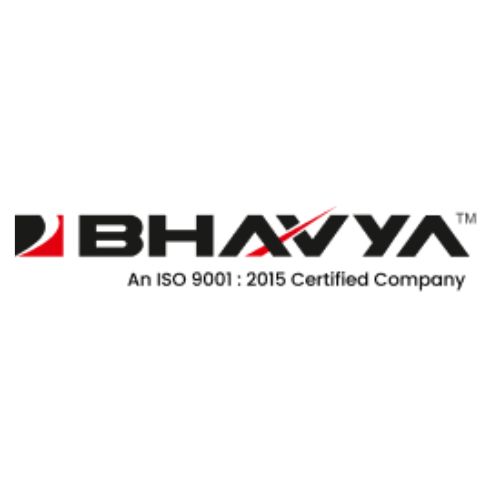
Important Tool Room Machines You Need to Buy for a Workshop
Improvement of processes in a workshop and automation doesn’t need to be an expensive affair. It needs to be a smarter choice of tool room machines required in a workshop. Various industrial applications require rigid material like wood and metal…
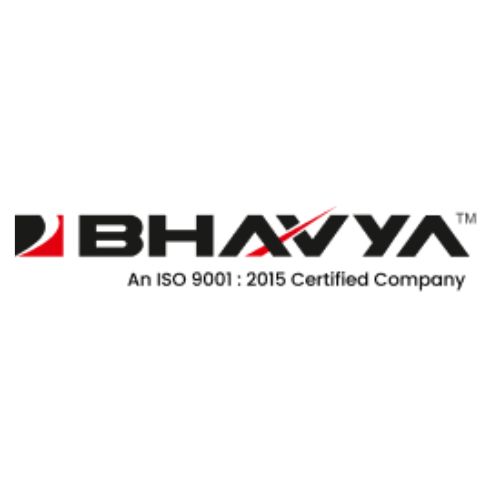
Bhavya Machine Tools Presents Grinding Machine, Slotting Machine & Shaping Machine
Machine tools are widely used tool room machineries across the industries. As an industry leader in manufacturing machine tools in various sizes and standard materials for rough & tough usage. There is a high demand of tool room, lathe, drill,…
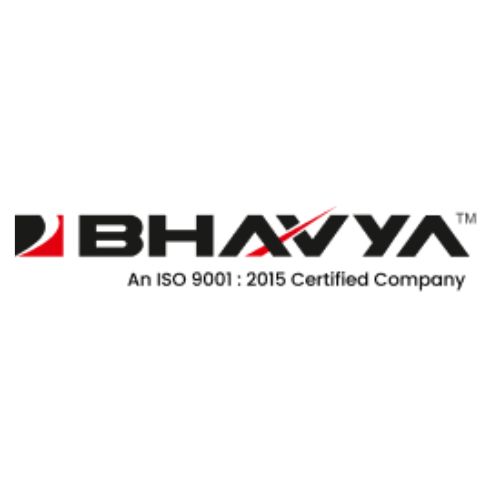
Types of Machine Tools You Need to Install in Your Workshop
A workshop is a place where different kinds of machines and tools are employed to make, finish and repair machines or parts. These are the important requirements without which no workshop can function. Workshops can be found in diverse industrial…
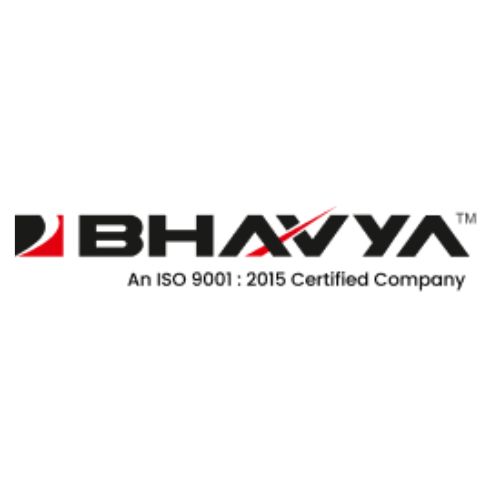
Machine Tools – Grinding Machine
Machine tools are used for various processing work on different metals. Machining works like cutting, grinding, shaping machine to shape the metal workpiece, boring, slotting on metal through slotting machine, shearing and others are carried out by mechanical and electronic…
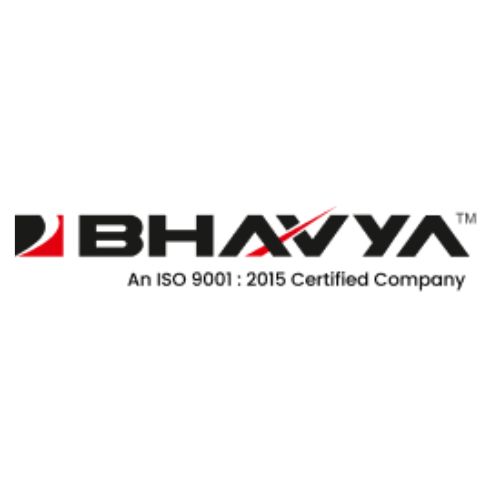
Uses of Lathe Machine, Press Brake and Grinding Machines in Metal Forming
Metals are casted into different shapes and sizes and used for various applications. This shaping and metal forming process is usually carried out with the help of various kinds of machinery in industries like automobile, engineering, electronics etc. Some of…
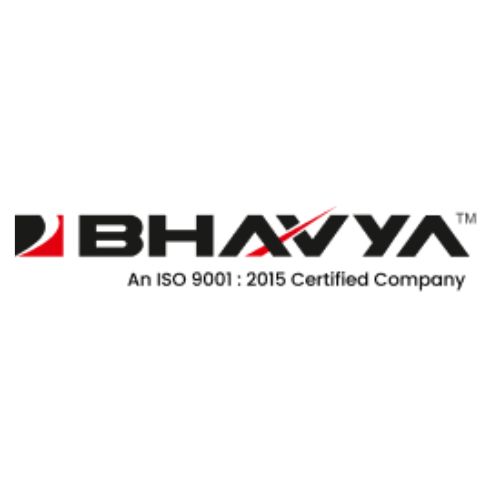
Machine Tools – Grinding Machine, Shaping Machine, Milling Machine
Grinding Machine Grinding machine is one of the important tools for industrial usage. It is also referred as Grinder. It has two abrasive wheels for grinding the work piece. Grinder can be used to cut and grinding the work piece…