Category Archives: Bandsaw Machine
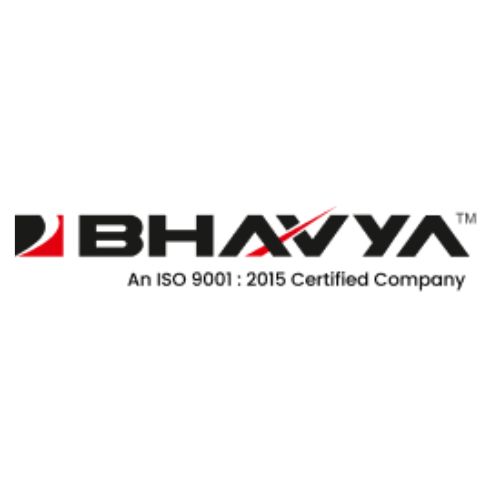
Top Applications of Horizontal Bandsaw Machines in Kuwait’s Oil & Gas Industry
Kuwait’s oil and gas industry plays a pivotal role in powering the country’s economy and meeting global energy demands. Behind the scenes of exploration, drilling and infrastructure expansion lies a critical backbone of mechanical equipment-particularly cutting machinery-that keeps fabrication and…
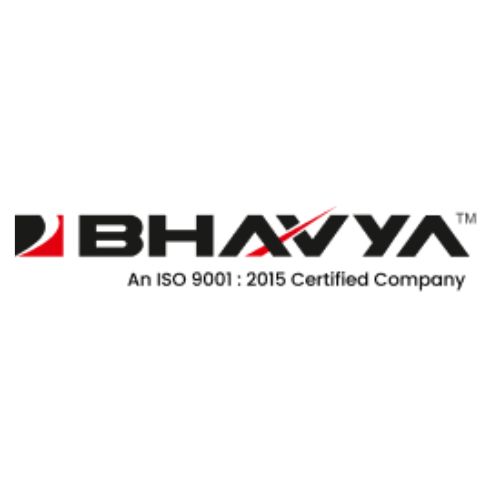
Global Demand and Supply for Machine Tools: Key Products and Role of Bhavya Machine Tools
The demand for machine tools is growing exponentially across the globe as industrial development accelerates in sectors like manufacturing, construction, and metalworking. Machines like Radial Drill Machines, Slotting Machines, Power Presses, and CNC Vertical Machining Centers play a crucial role…
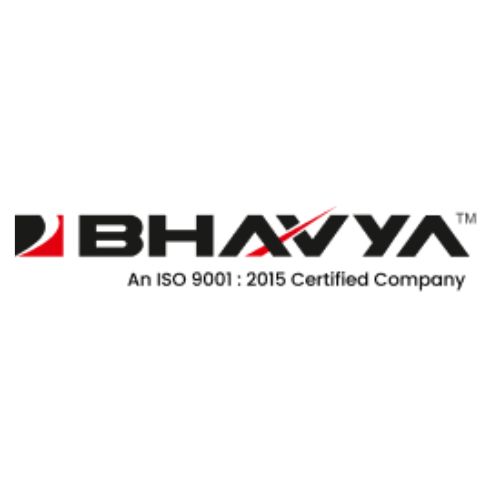
Bandsaw Blade Sharpener – Features, Applications and Benefits
A Bandsaw Blade Sharpener is a machine that is used to sharpen bandsaw blades used for cutting wood, metal, and other materials. Bandsaw blades tend to become dull over time due to the constant friction and wear and tear that…
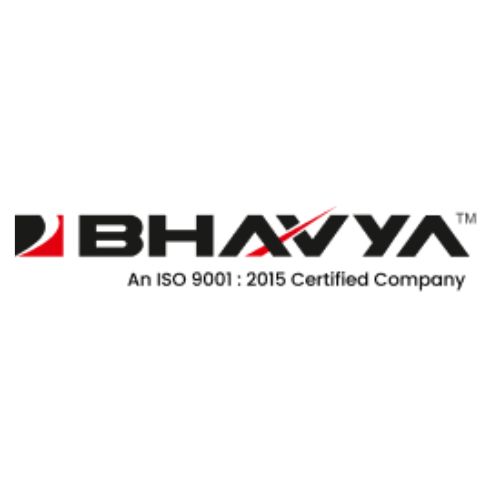
Different Types of Bandsaw Machine in India
Whether you're a seasoned woodworker or just starting out, choosing the right Bandsaw Machine in India for your woodworking needs can be a daunting task. But with a little research, you can rest assured you're buying the best tool for…
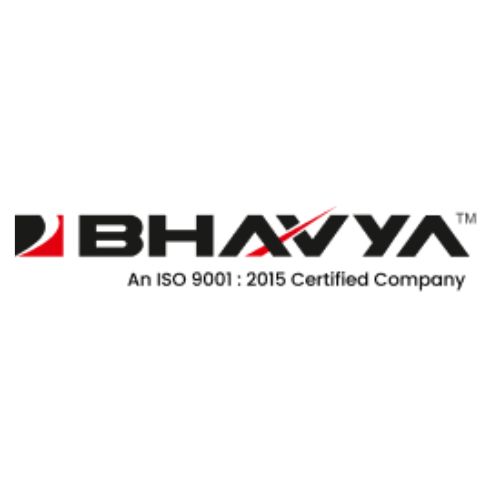
How to Use a Vertical Bandsaw Machine?
A Vertical Bandsaw Machine is an advanced single blade machining unit, capable of cutting timber of various thicknesses and producing high-class finish. A Vertical Bandsaw Machine consumes less electrical power. They are also built with a sturdy frame and machining…
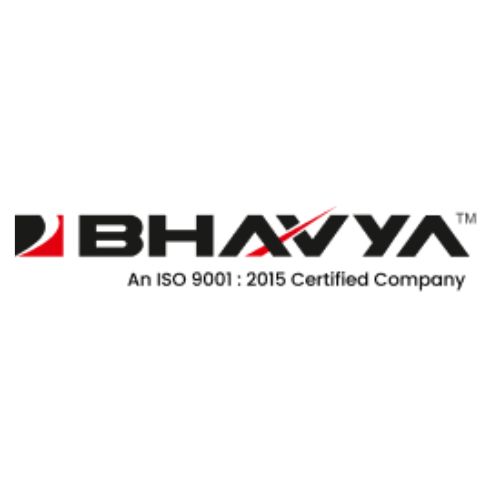
Bandsaw Machine Tools for Africa
If you're looking for a Bandsaw machine for sale in Africa, you've come to the right place. We've provided information about the benefits and features of bandsaw machines as well as their price and segmentation. Read on to learn more…
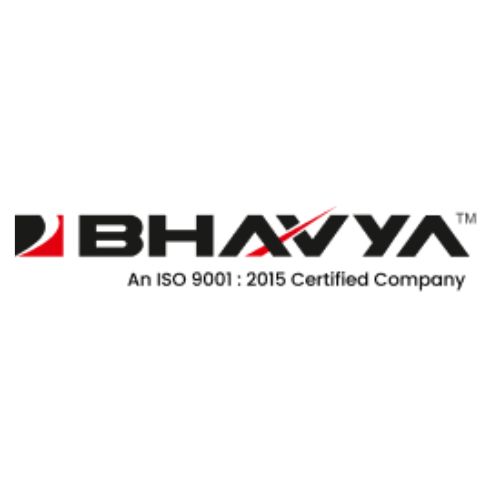
How to Install a Bandsaw Machine – User Guide
A bandsaw machine is a machine that shaves wood using a blade that is continuously rotating. It is powered by steam, electricity, or wind power. The process for removing the blade involves turning off the power, opening the cabinets, and…
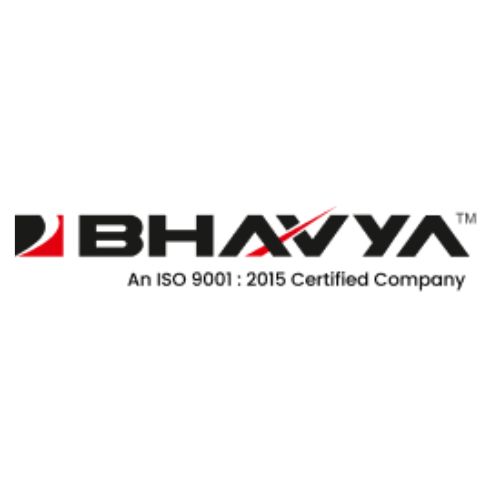
Choosing a Bandsaw Machine – User Guide
Whether you're looking to make a large or small cut, a bandsaw machine is a great tool for the job. These machines come in various models and can be used for many different jobs. The table on a bandsaw is…
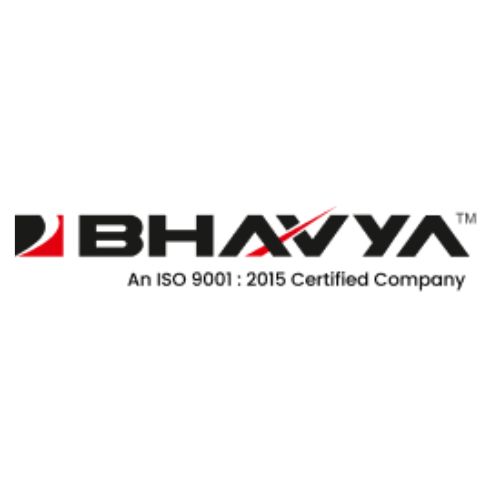
How Versatile Are Vertical Bandsaw Machine?
Bhavya Machine tools produce the best vertical Bandsaw Machine. As a business, they put lots of time and money into the research and development of the latest model available on the market. We continue to use innovative methods to improve…
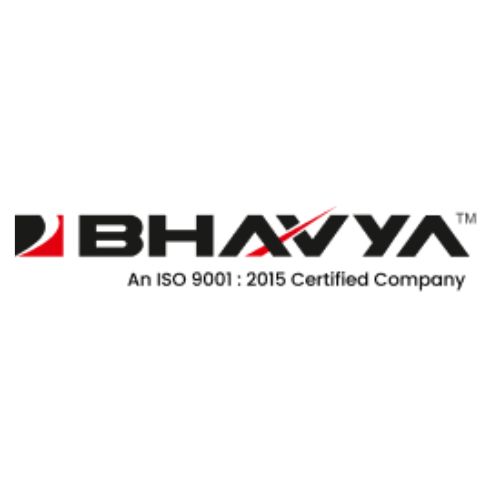
Why Use a Horizontal Bandsaw Machine? And how to choose a Degree Cutting Bandsaw Machine
A Horizontal Bandsaw Machine has been a fundamental tool in many woodworking workshops and a very versatile power tool. The operative work piece is placed into a horizontal position and the cutting blade drags down through the material along its…
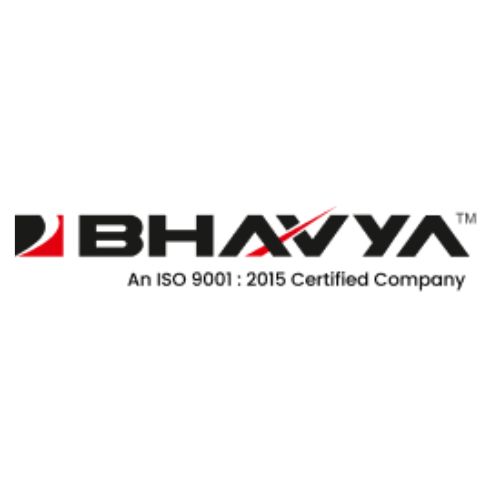
Bandsaw Butt Welding Machine – Overview
If you are looking for a versatile power tool that can perform multiple welding operations, you will want to consider the popular but little-known Bandsaw Butt Welding Machine. This amazing device uses the concept of a handheld plasma cutter/welder to…
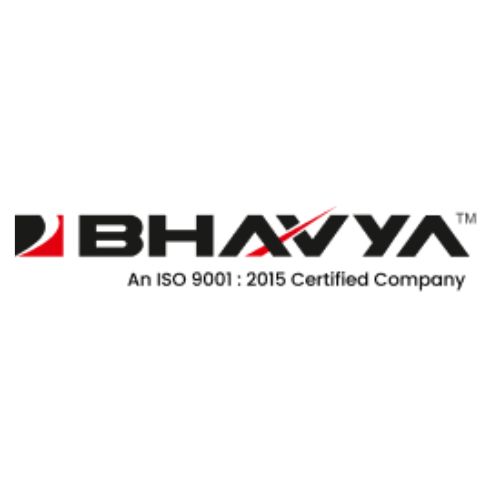
Rising Demand for Different Machine Tools in Industrial Sectors of Punjab
Punjab has emerged as India’s one of the most industrially advanced states. The demand for specialized industrial machine tools has risen significantly over the years in Punjab state, thanks to rapid industrialization and the rise of small and medium-sized businesses.…
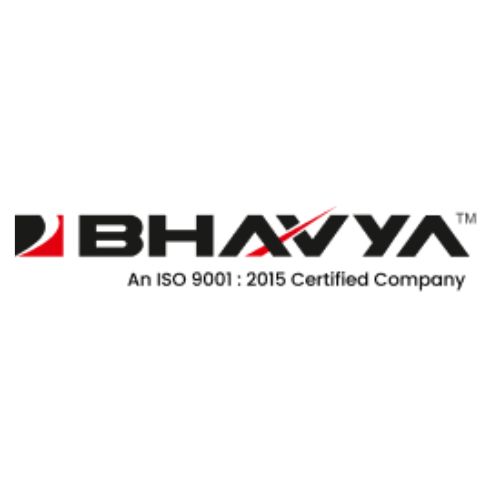
Growing Demand of Machine Tools in Rajkot for Various Industries
Rajkot is a city in Gujarat where industries have existed since the olden days. There are different industries in Rajkot like auto parts industries and machine tools industries. And with the increasing population, the demand for different tools like drilling…
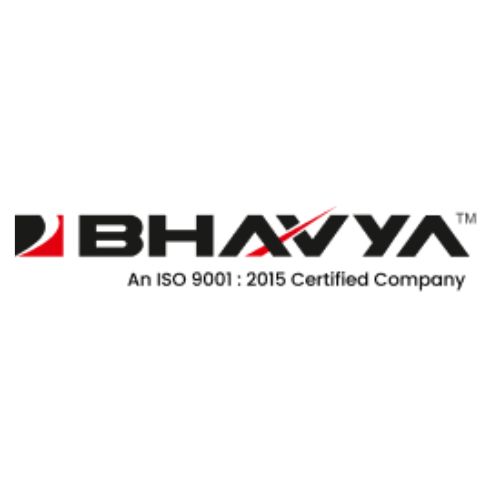
Automatic Saws – Supporting Preparation of Decorative Objects
Countless Uses of Metal for Decorative Purposes Recently the craze for beautifying construction works has reduced the use of brick work and employs metals in artistic ways. Steel, cast iron, aluminium, alloy coated material are few among them that are…
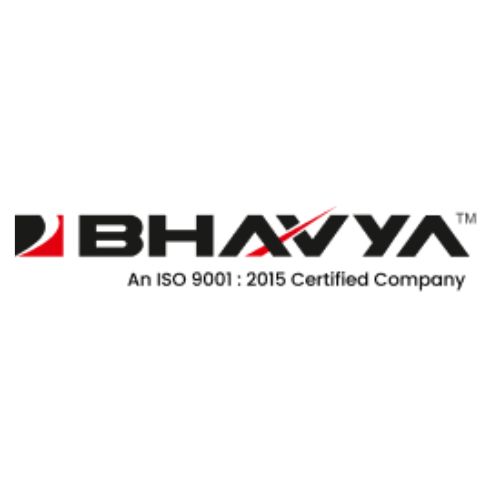
Blade Metallurgy – Why Industries Concerned Much about This?
Metals and Metallurgical Concern in Industries Metallurgical concern is more important when it comes to selection of machining components. If you are very particular about investing for long term and continuous production requirements, then selection of equipments which are designed…
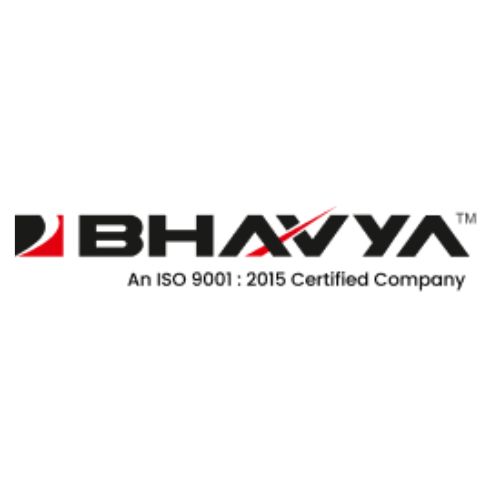
Powerful and Durable Welding Equipment for Fabrication
Welding is of different sorts and it starts from minute to higher level operations. We present powerful and durable equipments of various types that can be used for fabrication works. Flexibility and Portability of Table Mounted Spot Welding Spot welding…
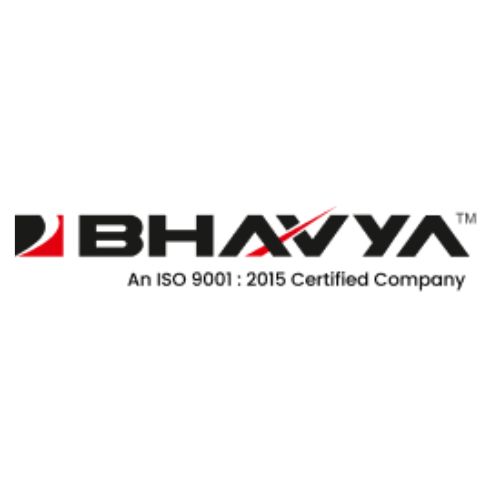
The Bandsaw machine; No more Quality losses
It used for cutting metal, wood or even meat in food processing. It is made up of a continuous band of metal with cutting teeth similar to a wood work saw. The construction of the saw blade is such that…
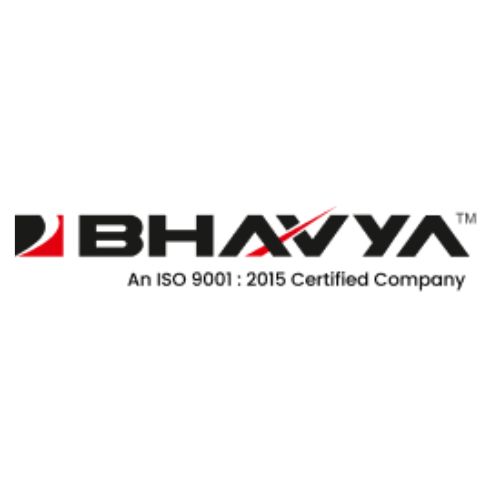
How to Choose Right Bandsaw Machine for Woodworking & Metal Shaping
The bandsaw is one of the most important equipment in any workshop. It is also regarded as an ideal tool for accurately cutting different types of materials that includes wood, metal, plastic, etc. In fact, besides cutting curves a bandsaw can…
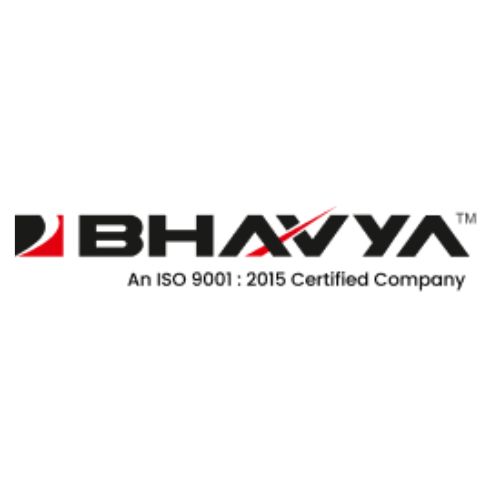
5 Most Important Machine Tools For Any Workshop [INFOGRAPH]
Nowadays, several types of workshop machine tools are manufactured in many countries around the globe. These tools are commonly used for different purposes in a wide range of industrial segments such as woodworking, automobile, electrical, construction, etc. This infograph give…
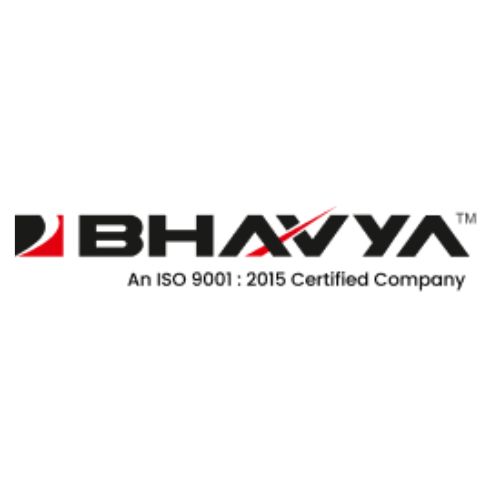
Rising Demand of Woodworking Machineries Across the World
Woodworking machines are highly popular and widely used equipments. They are basically utilized for performing various processes on wood, such as cutting, carving, drilling, finishing, grinding, joining, molding, sawing, sanding, shaping, etc. It help to avoid manual labor and the conventional…
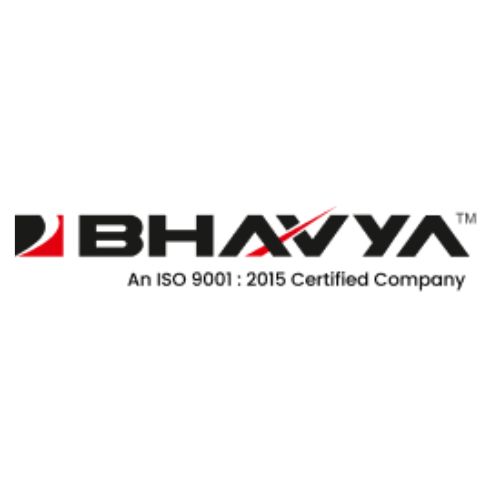
Applications of a Horizontal Bandsaw Machine
A machine that is used for cutting wood, metal, plastic and a variety of materials into straight, curved or irregular shapes is called a horizontal bandsaw. A wide range of bandsaw equipments are available in the market. They are made from cast…
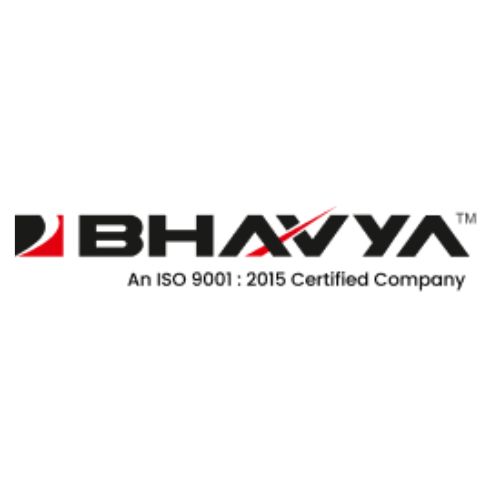
Features to Look for While Selecting a Bandsaw Machine
The bandsaw machine is one of the most essential tools widely used for woodworking, metalworking and cutting a variety of materials into straight, curved and irregular shapes. Nowadays, a wide range of bandsaw equipments are available in the market. They are built…
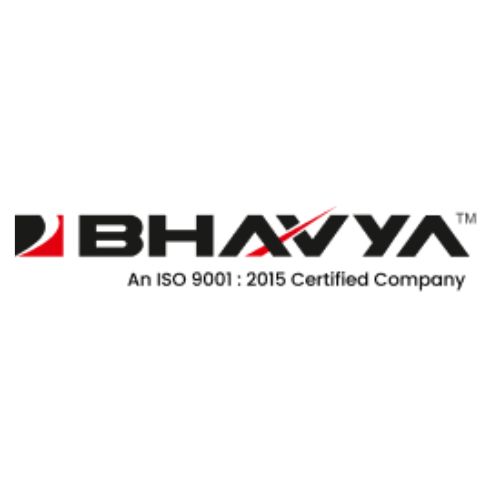
Types of Workshop Machinery Which can Enhance Efficiency and Productivity
These days, a variety of workshop machines are readily available in the market. Following are the different types which can enhance efficiency and productivity. A shaping machine is an exceptional workshop unit that is generally applied to shape flat or straight metals…
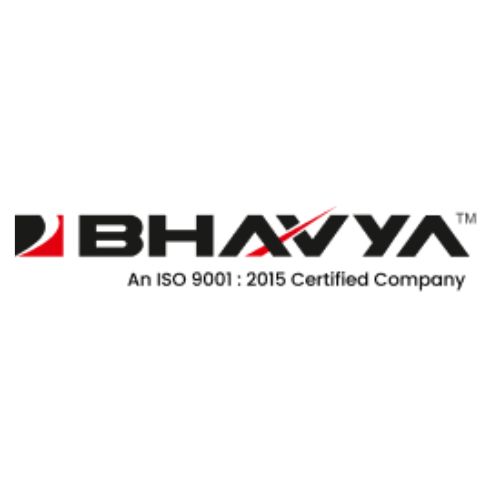
The Most Important Machine Tools Required in Any Workshop
The most important tools required in any workshop, nowadays are described below. Milling Machines The milling machine is used for milling, cutting, shaping, carving, planing, contouring, drilling, stamping, and die-sinking a variety of solid materials. The work piece is positioned, to…
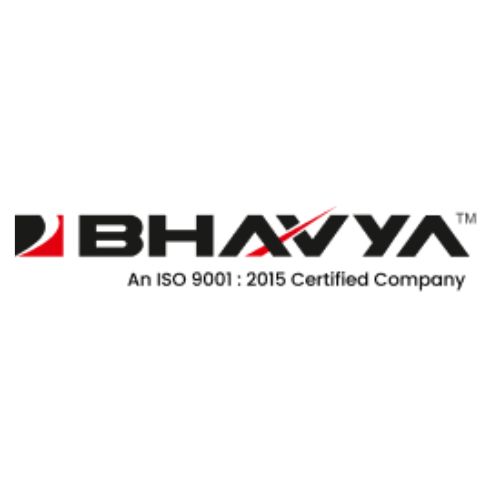
A Brief Description About Useful Tool Room Machines
A tool room basically refers to a room in an industrial unit where special machinery is used, in order to manufacture or repair the various tools and components that are necessary to produce the final product. A tool room also…
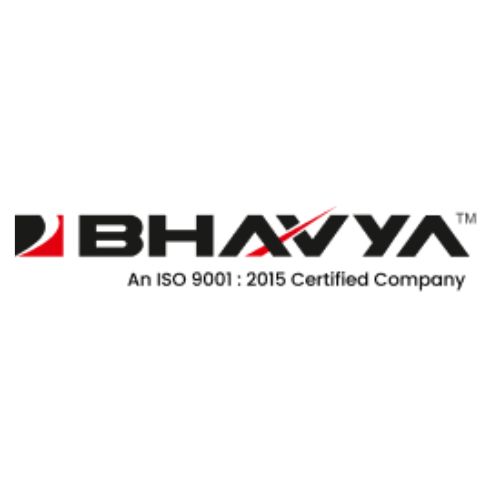
Important Tool Room Machines You Need to Buy for a Workshop
Improvement of processes in a workshop and automation doesn’t need to be an expensive affair. It needs to be a smarter choice of tool room machines required in a workshop. Various industrial applications require rigid material like wood and metal…
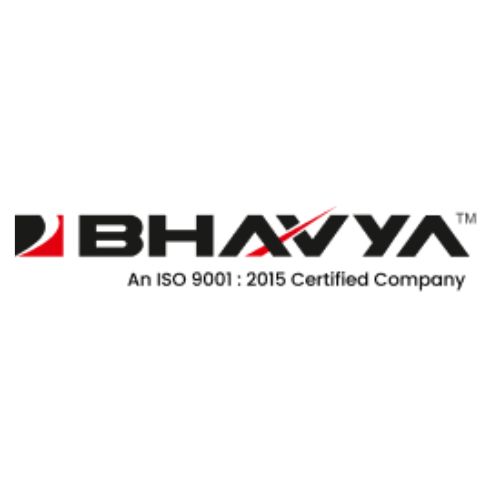
Bhavya Machine Tools introduces Bandsaw Machines for Size Ranges 175mm to 450mm
Irregular and curving shapes in wood and metal are quite efficient with new introduced technical enhancements in bandsaw machineries from us. These 175mm to 450mm capacity bandsaw machine are a power tool from us consisting blade to band the metal…
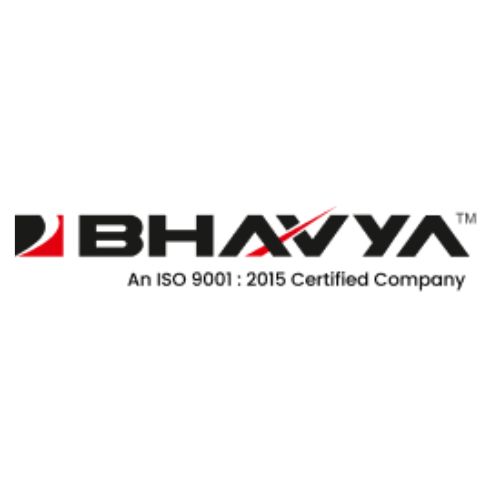
Tool Room Machines – Types of Tool Room Machine, Applications of Tool Room Machines
Tool room machines are the machines used in grinding, shaping and cutting wood, metal and other materials in various industrial applications. Grinding machine, milling machine, shaping machine, slotting machine, bandsaw machine and hackshow machines are some of the tool room…