Category Archives: Hydraulic Press Brake
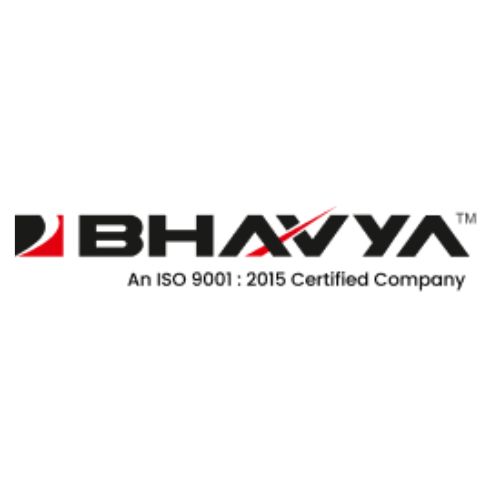
Enhancing Industrial Efficiency with NC Hydraulic Press Brake Machines in Saudi Arabia
Introduction Saudi Arabia, a prominent hub for industrial growth and development, demands advanced machinery to support its diverse manufacturing sector. Among the essential equipment enhancing productivity and precision in Saudi industries is the NC Hydraulic Press Brake Machine. As a…
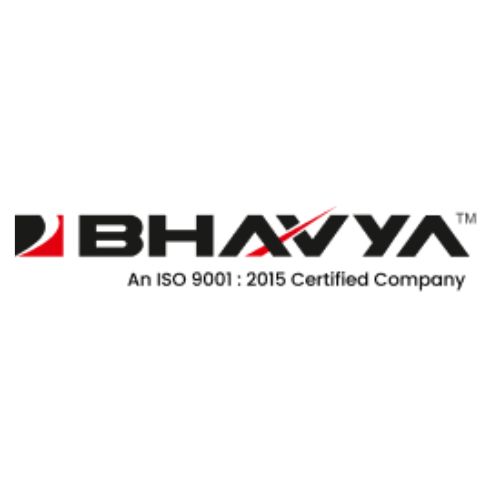
Features of Hydraulic Press Brake Machine: Unveiling Precision in Metal Fabrication
In the realm of metal fabrication, the Hydraulic Press Brake Machine stands out as a cornerstone for precision and versatility. Bhavya hydraulic press brakes, in particular, amalgamate a set of versatile features that elevate them to the epitome of precision…
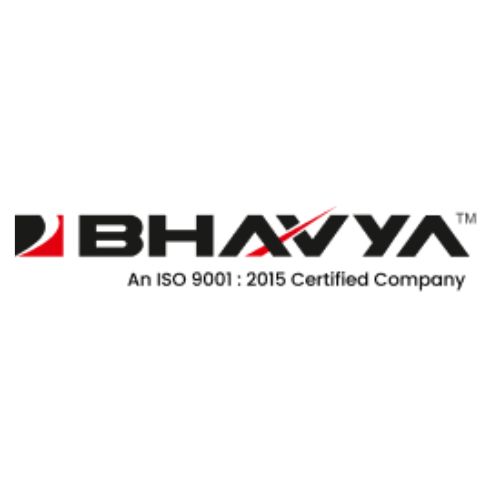
Press Brake Machine Industry in Dubai
A press brake machine is a type of mechanical device which helps to prevent a part from being bent, which means the machine can be used for pressing the end of a piece of material. There are several types of…
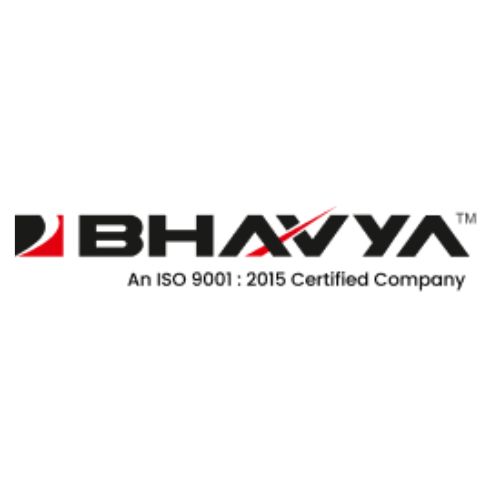
Hydraulic Press Brake – What You Should Know Before Purchasing?
There are several things you should know before purchasing a Hydraulic Press Brake. This article explains some of the key features of these machines and their benefits. In addition, this article will explain how deflection compensation works, Adjustable gauge, and…
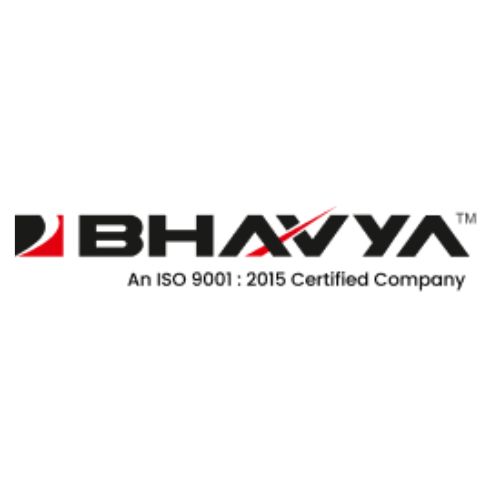
Hydraulic Press Brake Features
When shopping for a hydraulic press brake, you need to pay close attention to a few factors. These include accuracy of.0004", large strokes and daylights, and deep throat depth. In addition, you need to consider how much force it can…
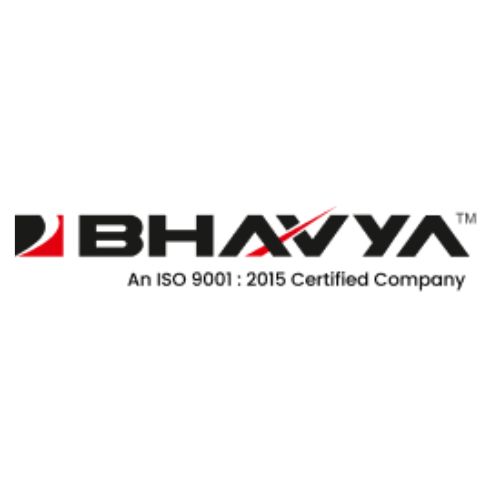
Hydraulic Press Brake – Overall Benefits
A hydraulic press brake is a tool used for bending metal components. They can handle a wide variety of materials, including thick steel and aluminum. If you are planning to purchase a press brake, here are some tips to make…
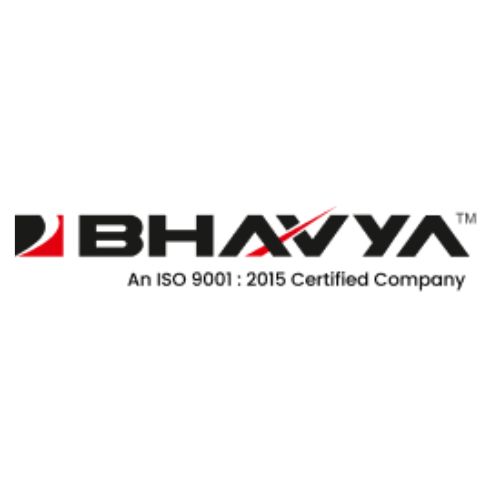
How Are Hydraulic Press Brakes Used?
A CNC hydraulic press brake (or rotary press lock) is a piece and plate metal rotating machine used in manufacturing. The rotary press lock forms curved surfaces out of workpieces before the grinding operation. The hydraulic press brake also shapes…
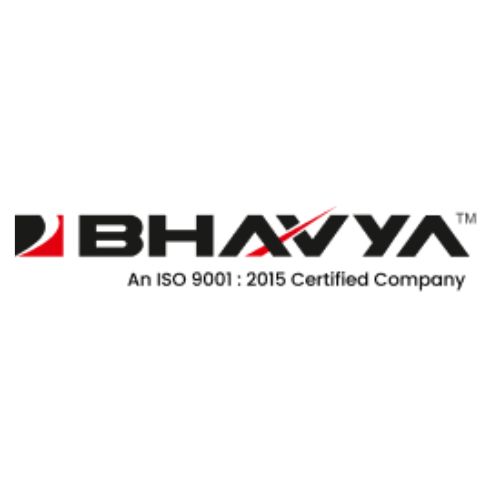
Hydraulic Press Brake System, and How do the Press Brake Machine Work?
Hydraulic presses are used in different industries. These include automotive, power generation, oil & gas, chemicals, textile, and paper production, as well as other manufacturing processes. Their design is based on the principle of reciprocity. This means that when two…
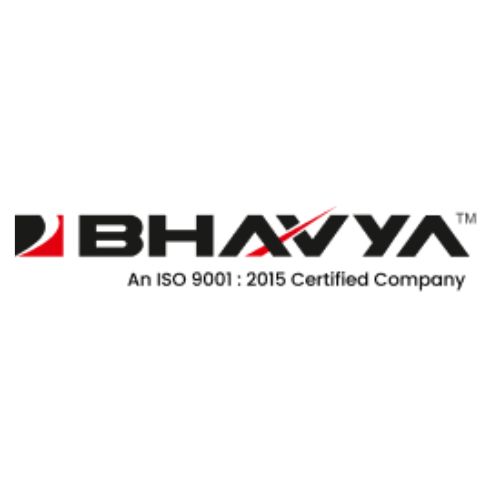
5 Important Revisions in Traditional set up of Press
Traditional Press Setup Traditional press brake setup was found to be with hydraulic principle and the usage can be traced back to ancient Mesopotamia and Egypt. Later as years went on Greeks introduced some changes into the provisions considering suitability…
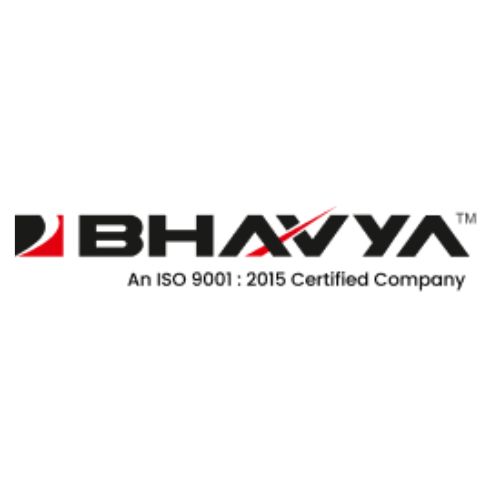
Environment Friendly Features of Press Brake
Machineries, Industry and Environment Industries that depend on machineries remain hindrance to environment in terms of the noise emitted from the industrial premises and the wastes removed. These factors certainly pollute the atmosphere in some way or other. Common Hindrance…
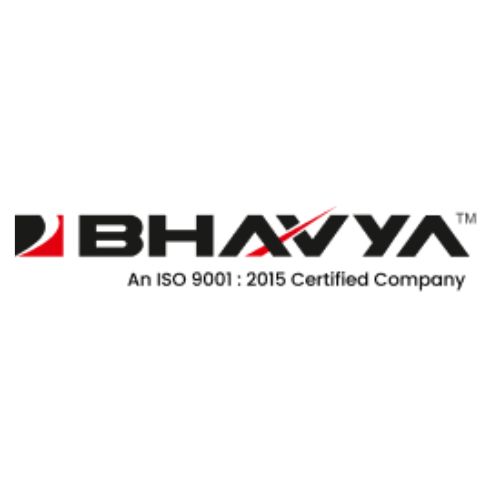
All About Mechanical Press Brake
Importance of Press Brake A press brake is a machining component applied for easy way of bending metal sheets. It is possible to make pre-determined bends and there stays the importance of this workshop device. What make Mechanical Press Brake…
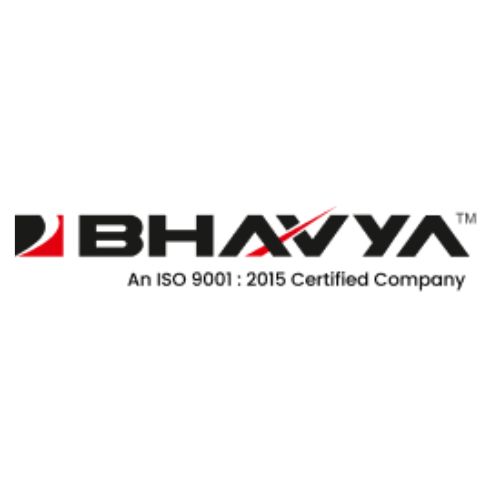
Does the Hydraulic Principle Support for Energy Saving?
What is Hydraulic Principle? A hydraulic fluid helps to run the machinery hence, that works with hydraulic system offers great value. Large force can be generated with hydraulic fluids and can stay a power saving option too. How Hydraulic Principle…
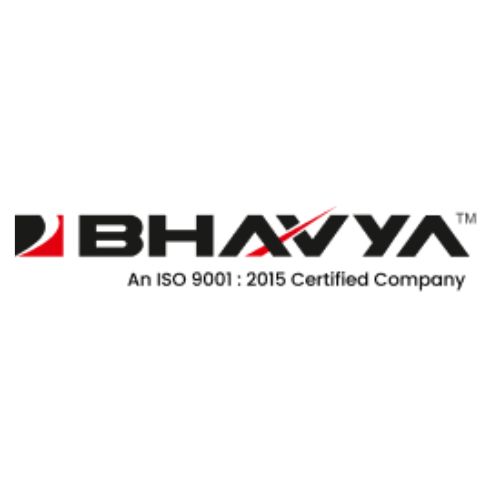
Possible Bending Variations with Press Brake
The Purpose of Press Brake A press brake is workshop equipment that is mainly used for bending metals and metal sheets. Wherein, it can be done either in V shape or U shape in accordance with the industrial requirement. It…
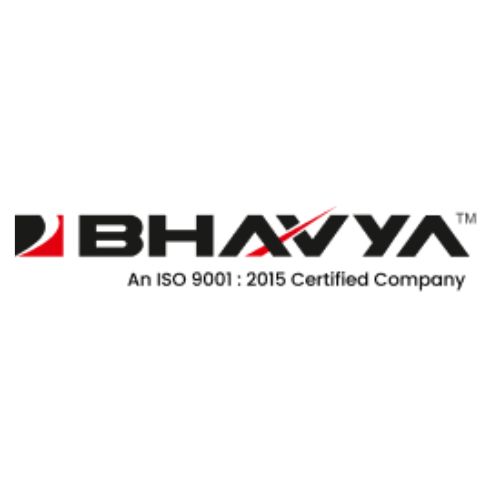
How are mechanical and hydraulic press brakes employed for sheet metal bending?
Press brake or break press is a equipments used for bending sheets of metals, or other materials. Prior to using a metal plate or a sheet it has to be shaped or formed. To do this a machine or a…
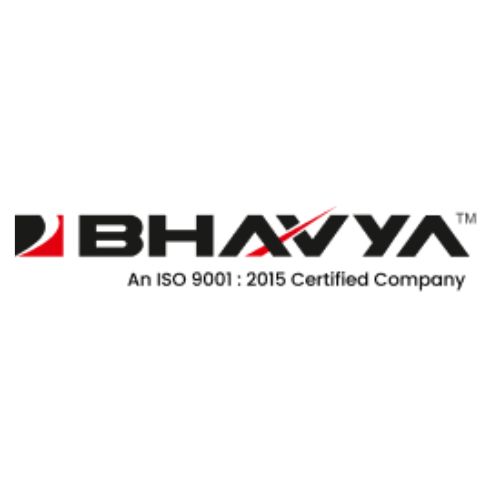
Set Up Procedure for Mechanical and Hydraulic Press Brake
Introduction - Press Brake It is a kind of bending machine used for bending sheet metal into a predetermined shape. The bending depends upon the shape of the punch and the die. These are being widely used in metallurgy, aircraft…
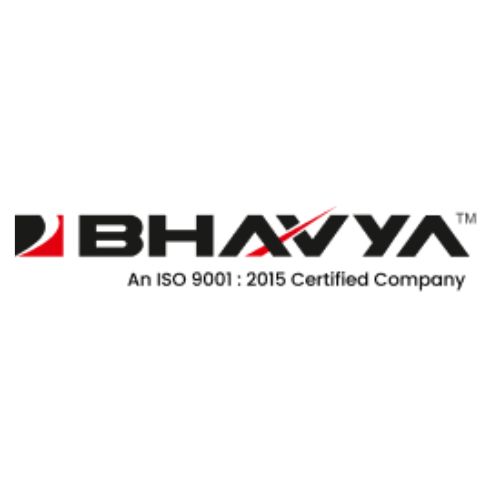
How does a Hydraulic Press Brake work to give a Customized Sheet Metal Bending Operation?
It is important equipment for the industries having jobs related to the metal shaping or bending. Two types are popular among metal fabricators – the manually operated press brakes and the press brakes which operate on the hydraulic power. The…
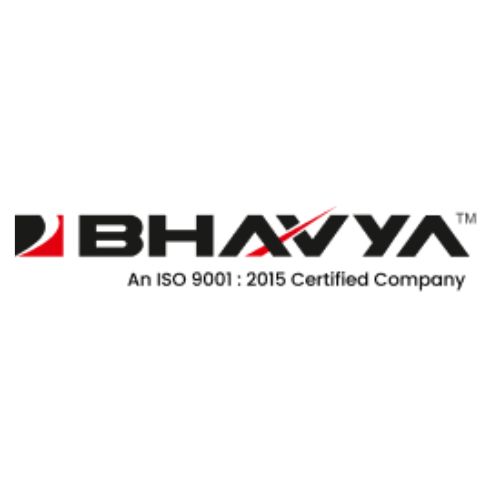
FAQs on Press Brake
A press brake is primarily used for accurately bending various types of metal sheets and plates. Some frequently asked questions are as follows: Q. What is camber? A. Camber is actually a small piece of cap which is placed on…
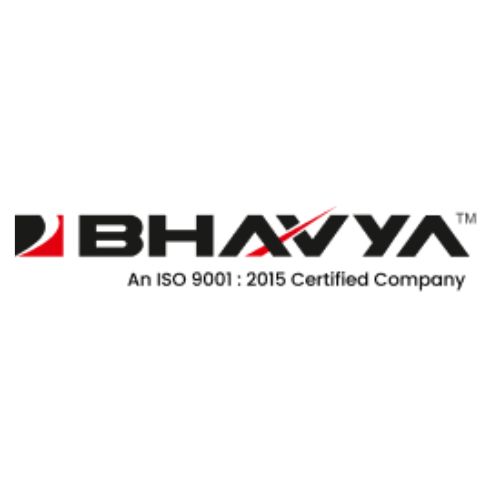
Sheet Metal Machineries for Shearing, Bending & Cutting
The various sheet metal machineries for shearing, bending and cutting are described below: Press Brake The mechanical press brake has a sturdy frame built from high grade steel. It also consists of steel plates with appropriate thickness and machined guide…
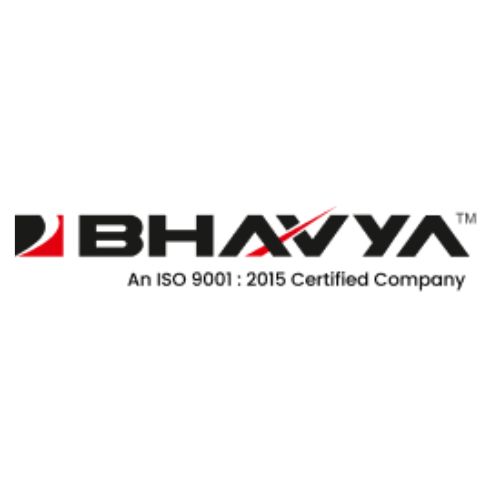
Significance of a Press Brake in Metal Cutting Applications
A number of machines are used in the process of fabrication of sheet metal parts. Fabrication is the process of collective operations which are used to give a shape to the metal sheet. This involves a number of equipments like…
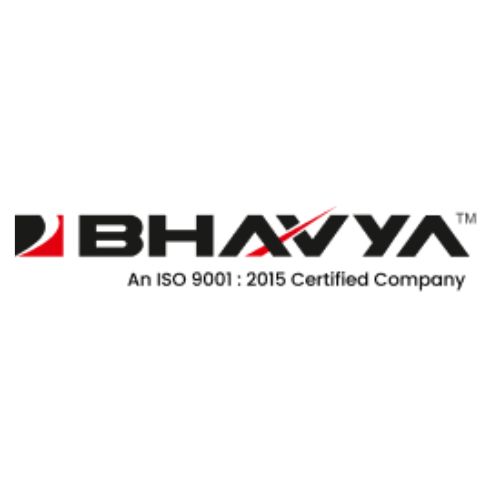
Press Brake, Slotting Machine – Machines used for Bending and Cutting Metals
Press Brake, Slotting Machine – It used for Bending and Cutting Metals Cutting and bending are the two primary functions performed on metals for casting the desired shape or dimensions. Therefore when it comes to metal working, the two most…
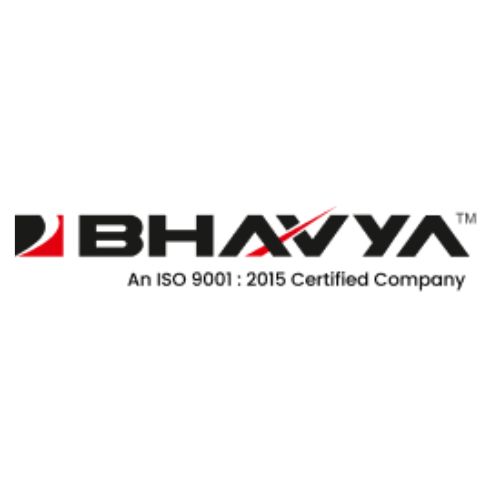
Applications of Different Types of Press Brakes – Mechanical & Hydraulic Press Brake
The press brake is primarily a machine tool that is utilized for bending a metal sheet or plate, into a shape which is determined by its die set. It forms preset bends by tightly holding the workpiece between the punch and die set.…
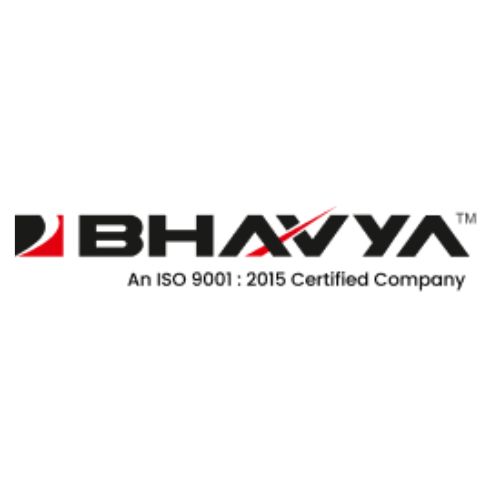
Selecting Right Type of Press Brake for Your Workshop
A press brake is also referred to as a brake press. It is basically a powerful machine tool that is commonly used for bending sheets and plates; particularly for bending sheet metal. It forms preset bends by holding the work piece in between the suitable punch…
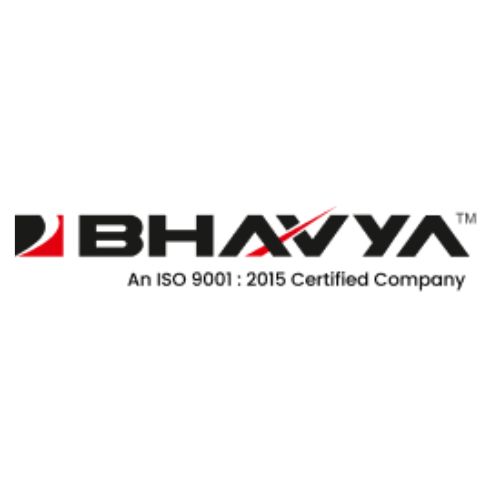
Mechanical Press Brake V/s. Hydraulic Press Brake – Which One is Better?
These days, various types of press brakes are available in the market, including mechanical and hydraulic. The main differences between a mechanical and a hydraulic is as follows. Hydraulic press brakes are simple to use and versatile for punching and…