A centerless grinding machine is an essential tool in the machining world, widely used for producing highly accurate cylindrical components. Unlike traditional grinding machines, which require the workpiece to be held in place by centers, the centerless grinder allows for continuous workpiece feed, making it ideal for high-volume production. These machines are designed to grind cylindrical parts with high precision and speed, particularly when the parts require tight tolerances.
In this article, we will cover the centerless grinding machine in detail, including its working principle, types, applications, key components and maintenance tips. By understanding the various aspects of centerless grinders, businesses can make informed decisions when selecting grinding equipment for their manufacturing processes.
What is a Centerless Grinding Machine and How Does it Work?
A centerless grinding machine is a machine tool used for grinding parts without the need for supporting centers or fixtures. Instead, the part is supported by a regulating wheel, a grinding wheel and a work rest blade. The workpiece is fed through the machine, which ensures continuous and efficient grinding of cylindrical parts.
How it Works:
The process begins with the regulating wheel, which rotates the workpiece and pushes it into the grinding wheel. The grinding wheel performs the actual grinding of the workpiece, removing material to achieve the desired dimensions. The work rest blade holds the workpiece in place while it is being ground, providing stability and alignment.
Centerless grinding machines operate in two primary methods: throughfeed grinding and infeed grinding, depending on the size and shape of the part.
Explanation of Infeed Grinding and Throughfeed Grinding Methods
- Throughfeed Grinding: This method is used when the workpiece can be fed through the grinding zone continuously, often applied to parts with uniform diameter throughout. The workpiece is fed in one side and exits the other side with the desired finish.
- Infeed Grinding: This method is used for workpieces with varying diameters or specific shapes. The workpiece is positioned at an angle and the grinding wheel is adjusted to remove material from specific areas, often used for parts with a shoulder or complex geometry.
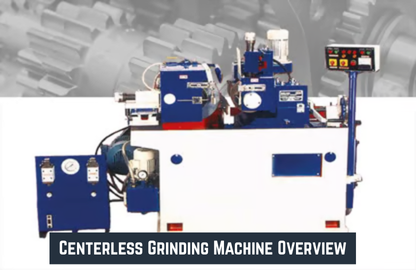
Types of Centerless Grinding Machines
Centerless grinders come in various types, each designed for different applications:
Manual Centerless Grinding Machines: These are traditional machines where the operator manually controls the infeed and regulating wheels. These machines are simple to operate but require more labor and time for setup and operation.
CNC Centerless Grinding Machines: CNC centerless grinders use computer numerical control to automate the grinding process, allowing for more precise and consistent grinding with minimal human intervention. These machines are ideal for high-volume, complex manufacturing.
Infeed Centerless Grinders: These are designed for grinding parts with specific diameters or shapes, where the workpiece is fed into the machine and held in place while the grinding wheel performs the operation.
Throughfeed Centerless Grinders: These are designed for high-volume production of cylindrical parts that have a consistent diameter. The parts pass through the grinding zone without interruption, providing continuous operation.
Key Components of a Centerless Grinding Machine
A centerless grinding machine is made up of several key components that work together to deliver high precision and efficiency:
Grinding Wheel: This is the primary tool for material removal, typically made of abrasive materials such as aluminum oxide or silicon carbide. The grinding wheel’s size and abrasive properties determine the efficiency and quality of the grinding process.
Regulating Wheel: The regulating wheel controls the rotation of the workpiece and applies a continuous feed to guide the part through the grinding wheel. This component helps maintain accuracy and precision throughout the grinding operation.
Work Rest Blade: The work rest blade supports the workpiece during grinding, ensuring that it remains stable and aligned. It is adjustable to accommodate various workpiece sizes.
Coolant System: To prevent overheating and maintain optimal grinding conditions, a coolant system is used to lubricate the grinding wheel and cool the workpiece.
Control Panel: The control panel is used to operate the machine, including adjusting settings for speed, feed rate and other parameters. In CNC centerless grinders, this panel also controls automated operations.
Advantages of Centerless Grinding Machines
Centerless grinding machines offer several advantages, making them ideal for high-volume production and precision work:
High Precision and Accuracy: These machines provide tight tolerances and highly accurate results, making them ideal for parts requiring exact specifications.
Continuous Operation: Centerless grinders allow for continuous operation, making them suitable for mass production of cylindrical parts. Parts can be fed through the machine without interruption, optimizing throughput.
Ability to Grind Complex Shapes: Centerless grinders are capable of grinding parts with complex geometries, such as shouldered or tapered components, that are difficult to machine using traditional methods.
Low Maintenance: Compared to other grinding methods, centerless grinding requires less maintenance due to its simple design and fewer moving parts.
What Our Customers Say
“Recently we purchase tapping machine from bhavya machine tools and the performance of this machine is truly exceptional.”
Gulamrasul Panara On Google
Industrial Applications of Centerless Grinding Machines
Centerless grinding machines are used in various industries for precision parts manufacturing:
Automotive Components: Parts like shafts, valves and pins are often produced using centerless grinding, ensuring high quality and precision for automotive assemblies.
Bearing Manufacturing: Centerless grinders are essential in producing bearings with the precise dimensions required for high-speed applications.
Aerospace Parts: Parts used in the aerospace industry, such as turbine shafts, fasteners and landing gear components, are manufactured using centerless grinding due to the need for precision and reliability.
Surgical and Medical Instruments: Surgical tools and medical implants require high precision and centerless grinding ensures that these components meet stringent quality standards.
Hydraulic and Pneumatic Components: These components often require high tolerances and centerless grinding is commonly used to achieve the necessary finishes.
Buying Guide for a Centerless Grinding Machine
When purchasing a centerless grinding machine, consider the following factors:
Size and Capacity: Ensure the machine can accommodate the size and type of workpieces you plan to grind.
Automation Level: Decide whether a manual or CNC centerless grinding machine is more suitable based on your production needs. CNC machines offer higher precision and efficiency for high-volume operations.
Wheel Type: Choose the correct grinding wheel material and size to match the materials you will be grinding.
Power Requirements: Assess the machine’s power consumption and ensure it fits your workspace setup and energy requirements.
Maintenance & Troubleshooting
Regular maintenance is crucial to extend the life of your centerless grinding machinery and maintain its performance:
Daily Maintenance: Check the coolant levels, inspect the grinding wheel and clean the machine to remove debris and metal shavings.
Weekly Maintenance: Lubricate moving parts, inspect the regulating wheel and work rest blade for wear and check the alignment.
Monthly Maintenance: Perform more thorough inspections of the machine’s motor, bearings and spindle to ensure everything is operating smoothly.
Common issues include:
- Wheel Glazing: Caused by the buildup of material on the grinding wheel. Solution: Dress the wheel regularly.
- Chatter: Can result in poor surface finish. Solution: Check for proper alignment and balance.
- Dimensional Errors: Often due to incorrect settings. Solution: Calibrate the machine and check the workpiece alignment.
Cost Considerations
The price of a centerless grinding machine depends on several factors:
- Size and capacity of the machine
- Automation level (manual or CNC)
- Customization options for specific applications
While the initial investment may be higher for CNC machines, they offer long-term cost savings due to their higher precision, automation and efficiency, making them ideal for high-volume production.
Conclusion
Centerless grinding machines offer significant advantages in terms of precision, speed and versatility, making them indispensable in many manufacturing sectors. From automotive components to aerospace parts, these machines help produce high-quality, accurate parts with minimal downtime. By understanding the different types, applications and maintenance requirements of centerless grinders, businesses can optimize their production processes, reduce costs and enhance product quality.
FAQs About Centerless Grinding Machines
What is a centerless grinding machine?
A centerless grinding machine is a tool used to grind cylindrical parts without the need for centers or fixtures. It uses a regulating wheel and a grinding wheel to efficiently grind the workpiece.
What are the types of centerless grinding machines?
The types of centerless grinding machines include manual centerless grinders, CNC centerless grinders, infeed centerless grinders and throughfeed centerless grinders. Each type is suitable for different workpieces and production volumes.
What are the main advantages of centerless grinding?
The main advantages of centerless grinding include high precision, continuous operation for mass production, the ability to grind complex shapes and low maintenance compared to other grinding methods.
How do I maintain a centerless grinding machine?
Maintenance involves regularly cleaning the machine, lubricating moving parts, inspecting the grinding wheel and regulating wheel and checking coolant levels. It’s important to conduct weekly and monthly inspections to ensure the machine works at its best.