Category Archives: Lathe Machine
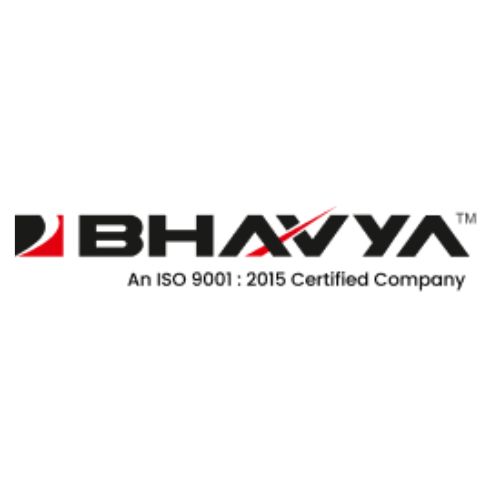
Lathe Machine: Everything You Need to Know
A lathe machine is one of the most important tools in manufacturing, offering precise control over the shaping and finishing of various materials. With its versatility and ability to create highly accurate parts, it is widely used in industries such…
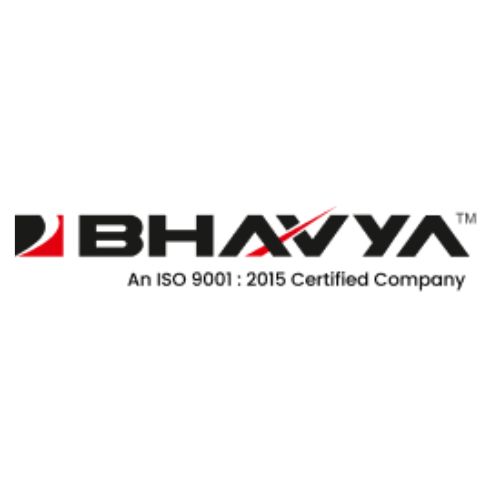
The Role of Lathe Machines in Bhutan’s Small-Scale Industrial Development
Bhutan's small-scale industrial sector is growing, driven by increasing demand for locally manufactured components and mechanical services. Lathe machines are playing a vital role in this transformation, enabling businesses to produce precision components, repair mechanical equipment and reduce reliance on…
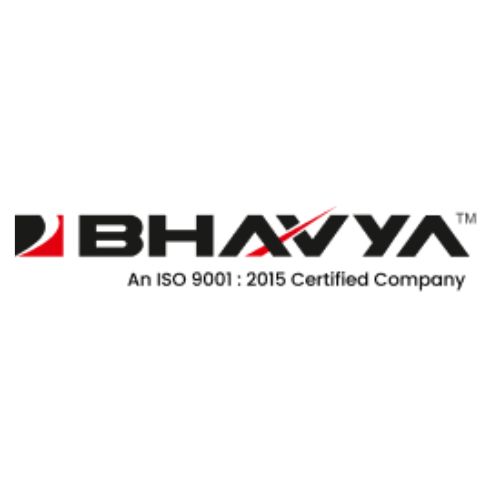
The Future of Lathe Machines in Tanzania’s Heavy Machinery and Mining Sectors
Lathe machines are essential in manufacturing, maintenance and repair across industries. Whether in mining, construction or transportation, these machines improve efficiency and precision. Cities like Dar es Salaam, Mwanza, Arusha and Mbeya of Tanzania are driving demand for modern machining…
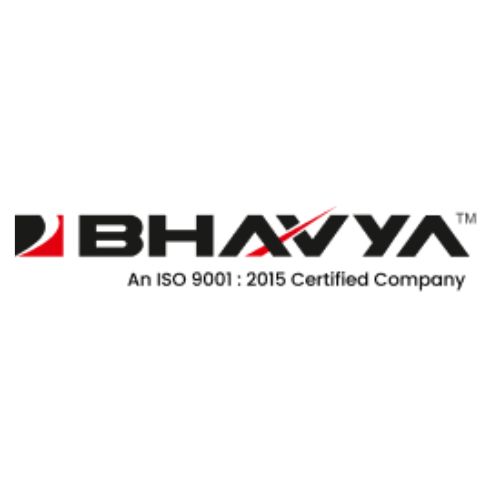
Role of Lathe Machines in Development of Kenya’s Agricultural Equipment Manufacturing
Kenya’s agricultural sector is a key driver of the economy, supporting millions of livelihoods. The demand for locally manufactured farming tools and machinery is increasing as farmers seek more efficient equipment. Lathe machines play a crucial role in producing durable…
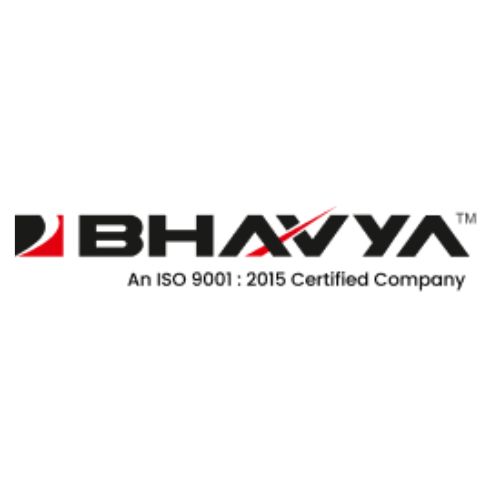
The Impact of Lathe Machines on the Maldives’ Shipbuilding and Repair Industries
The Maldives, a nation built around its maritime economy, relies heavily on ships for fishing, trade and transportation. Shipbuilding and repair are crucial industries that require high precision and efficiency. Modern lathe machines in Maldives have significantly enhanced these sectors,…
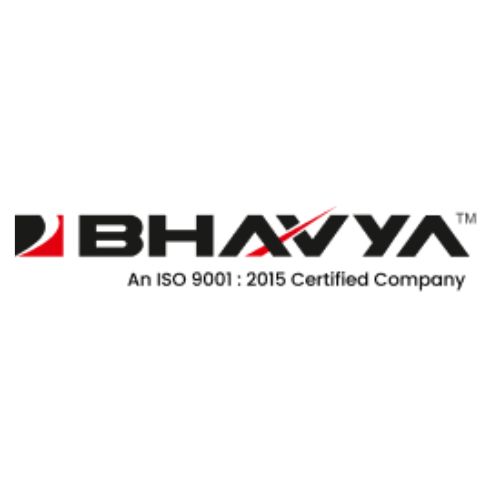
Lathe Machines Demand and Supply in Indian Cities for Various Industries
Lathe machines are a crucial part of the manufacturing sector, widely used for metalworking, woodturning, glass-working and parts reclamation. Industries like automobile, aerospace, toolmaking and general engineering depend on All-Geared Lathe Machines, V-Belt Lathe Machines and CNC Lathe Machines for…
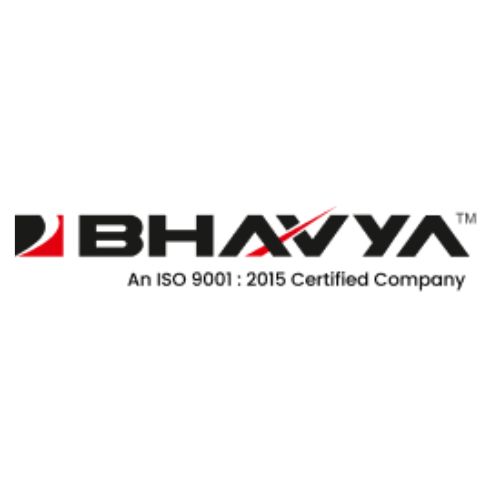
Barriers to Lathe Machine Adoption in Accra’s Small and Medium Enterprises
Lathe machines are essential tools in metalworking, manufacturing and machining. However, many SMEs in Accra struggle to adopt these machines due to financial, technical and infrastructural challenges.In this article, we will explore the key barriers affecting SMEs in various districts,…
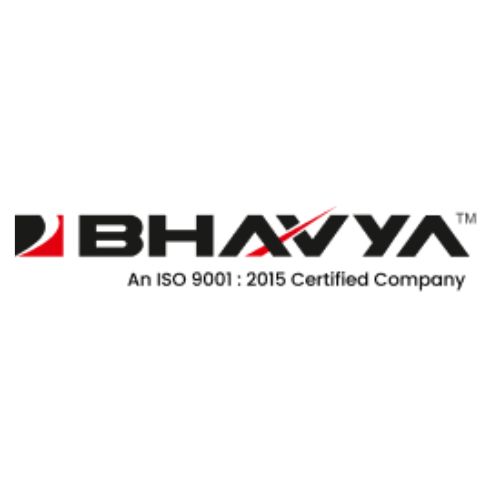
The Relationship between Lathe Machines and Robotics in Manufacturing
The integration of lathe machines and robotics is reshaping the manufacturing industry, combining traditional precision machining with modern automation. Lathe machines have been essential in manufacturing for decades, providing the ability to shape and cut materials with high accuracy. With…
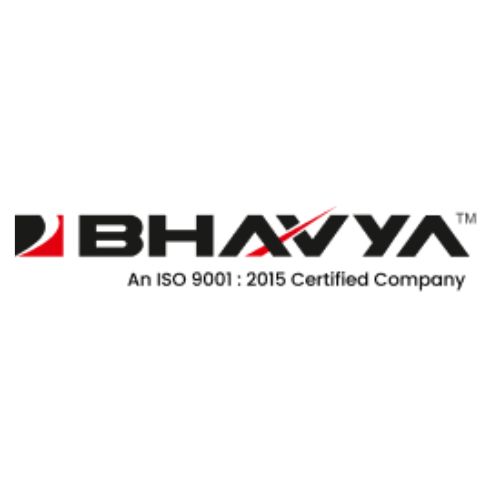
Role of Lathe Machines in Aerospace Manufacturing and Automotive Industry’s Mass Production
Lathe machines play a crucial role in manufacturing, particularly in the aerospace and automotive industries. These industries demand high precision, efficiency and reliability in machining components, making lathe machines indispensable for shaping, cutting and refining metal and other materials. From…
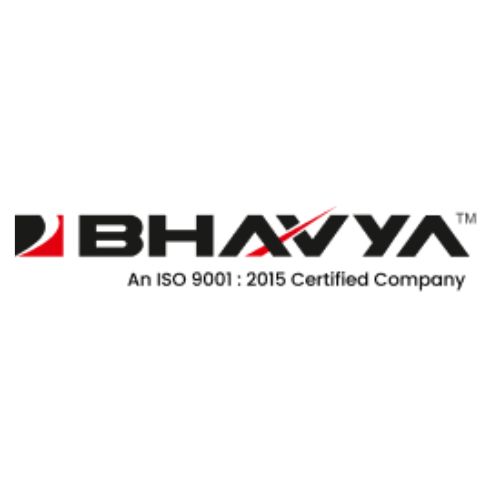
The Rising Demand for Lathe Machines in Bangladesh’s Construction and Infrastructure Sector
Bangladesh is undergoing rapid industrial and infrastructural growth. From bridges to high-rise buildings, the country is investing heavily in development. Lathe machines play a key role in shaping and machining metal parts for these projects. Cities like Bogra, Jessore, Tangail and…
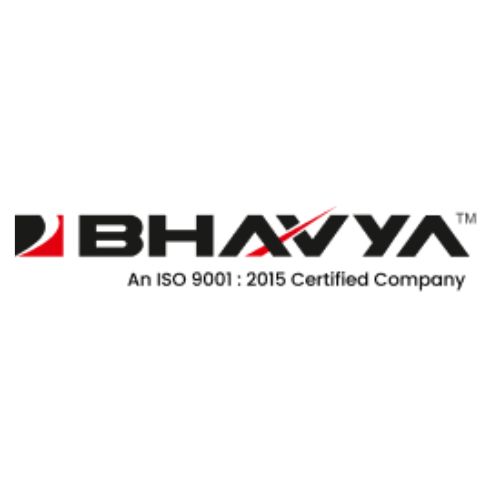
Lathe Machine Technology Impact on Bhutan’s Renewable Energy Industry
Bhutan is emerging as a leader in renewable energy, with its vast hydropower potential and growing interest in solar energy. Lathe machines play a critical role in manufacturing and maintaining components for turbines, solar panel structures and other renewable energy…
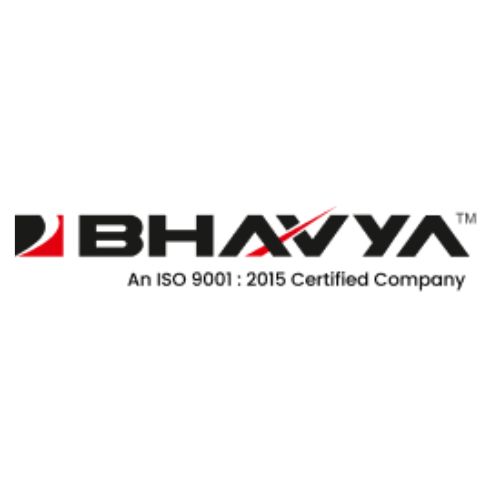
Lathe Machines in Dhaka: Driving Bangladesh’s Industrial Growth
Dhaka, the capital of Bangladesh, is at the heart of the country’s industrialization. Lathe machines play a crucial role in metalworking, precision engineering and large-scale manufacturing. As industries expand, the demand for CNC lathe machines, light-duty lathe machines, vertical lathe machines…
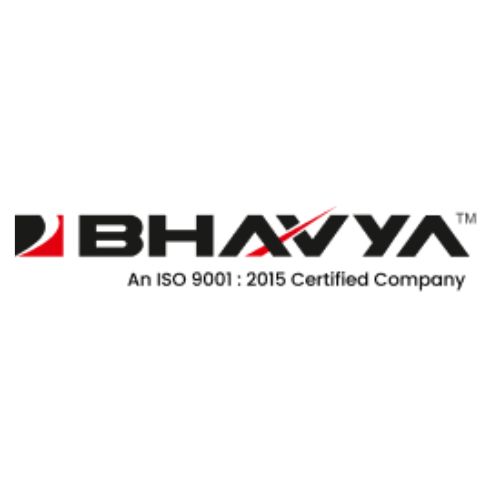
Ghana’s Lathe Machine Market: Trends, Challenges and Future Prospects
Ghana’s industrial sector is evolving rapidly, with cities like Accra, Kumasi, Tema, Tamale, Sekondi-Takoradi and Ashaiman playing a pivotal role in shaping the future of machining and manufacturing. The lathe machine market is at the center of this growth, with increased…
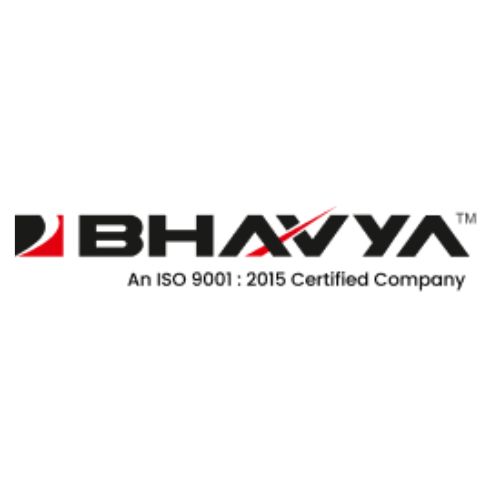
Different Applications of Lathe Machine in Tanzania’s Local Factories
Lathe machines are the backbone of Tanzania’s industrial sector. From Kigoma to Musoma, they help local factories produce high-precision metal and wood components. These machines shape, cut and drill materials essential for automotive, construction and metalworking industries. Tanzania’s factories use…
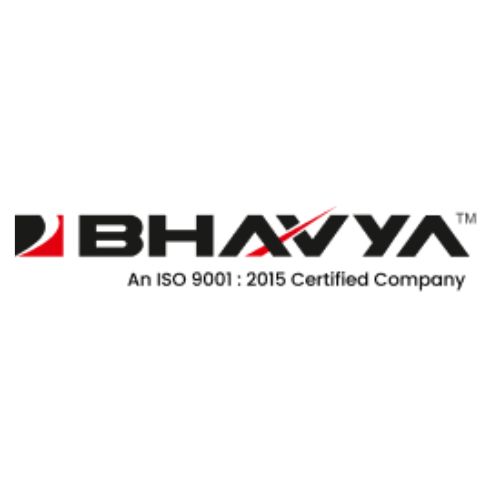
Exploring the Importance of Lathe Machines for Kenya’s Automotive Industry
Kenya’s automotive industry has experienced remarkable growth, largely driven by the adoption of advanced machinery. These technologies have played a pivotal role in enhancing the precision and efficiency of local manufacturing. This article will explore the specific challenges, benefits and…
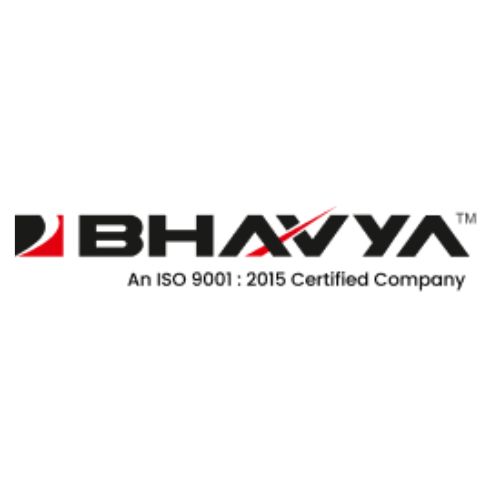
Challenges of Using Lathe Machines in the Maldives’ Limited Manufacturing Environment
The Maldives is globally recognized for its tourism industry, but its manufacturing sector remains small due to geographical and infrastructural limitations. Despite a rising demand for industrial machinery, using Lathe Machines in Maldives presents significant challenges. Cities like Villingili, Ungoofaaru, Hinnavaru, Naifaru,…
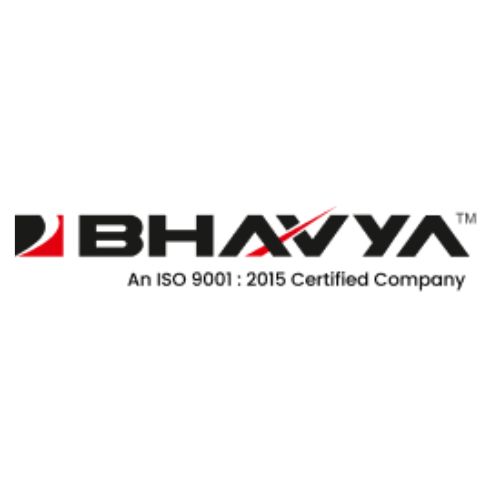
Lathe Machines: Transforming Local Manufacturing in Accra’s Industrial Hub
Accra has become a hub for industrial growth, with increased demand for precision machining across various sectors. From automotive workshops to heavy metal fabrication, businesses require accurate and efficient equipment to meet industry standards. Lathe machines have become an essential tool in…
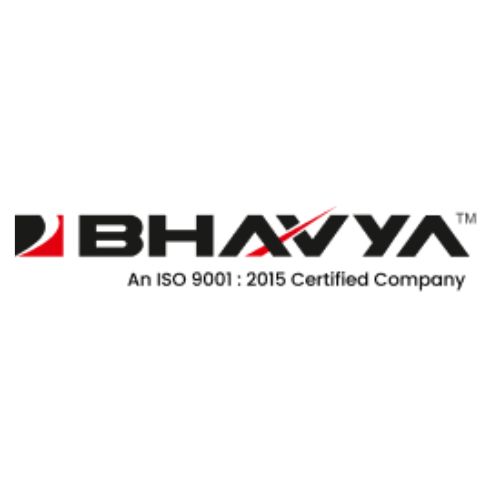
Lathe Machines in Ghana’s Oil and Gas Sector: The Need for Precision Manufacturing
Ghana’s oil and gas industry requires high-precision equipment to ensure efficiency and safety in drilling, transportation and refining operations. Machining plays a critical role in manufacturing pipeline components, drilling tools, flanges and pump systems. Without precise engineering, oil extraction and…
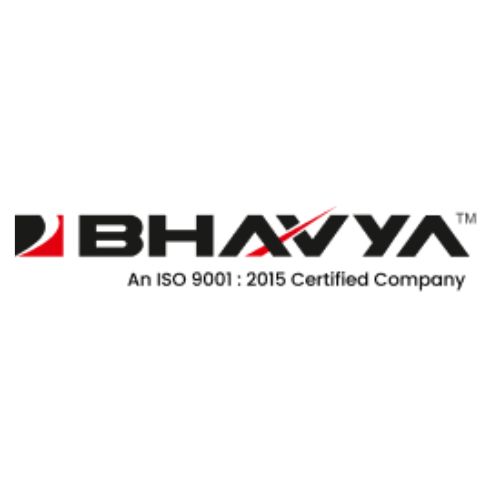
Lathe Machines: Challenges Faced by Dhaka Manufacturers in Operation and Maintenance
Dhaka, the industrial hub of Bangladesh, heavily relies on Lathe Machines in Dhaka for precision metalworking and manufacturing. However, manufacturers in Mirpur, Mohammadpur, Motijheel, Jatrabari, Paltan and Lalbagh face significant challenges in operating and maintaining these machines. Issues such as skilled labor…
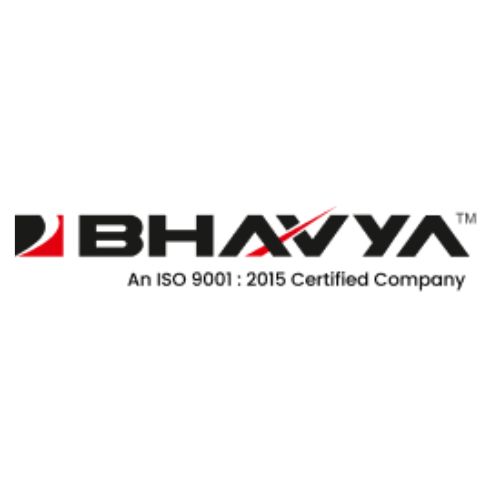
The Role of Lathe Machines in Iran’s Growing Aerospace Industry
Iran’s aerospace industry is undergoing rapid transformation, with increasing investments in aircraft production, space exploration and defense aviation. As the country strengthens its domestic aerospace capabilities, Lathe Machines in Nigeria, including Universal All Geared Lathe Machines, are playing a vital role…
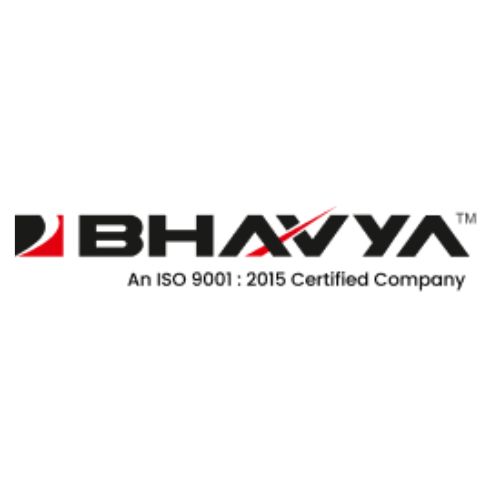
The Growth of Lathe Machine Technology in Nigeria’s Manufacturing Sector
Lathe machines are at the heart of Nigeria’s industrial development, supporting road construction, infrastructure projects and economic expansion. These machines play a crucial role in metal fabrication, equipment repair and precision machining, ensuring the durability and efficiency of infrastructure projects…
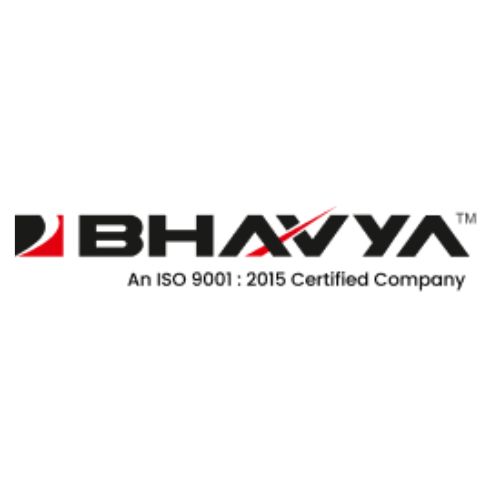
How Lathe Machines are Supporting Ethiopia’s Road Construction and Infrastructure Projects?
Lathe machines play a key role in Ethiopia’s infrastructure development. From shaping metal components for bridges to fabricating precision parts for road construction, these machines are essential in manufacturing durable and efficient construction materials. Cities like Asella, Nekemte, Woldia, Gambela,…
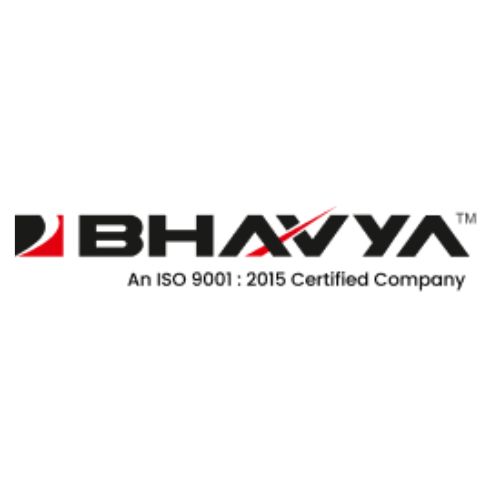
The Evolution of Lathe Machines in Bangladesh’s Textile Industry
Lathe machines have played a transformative role in Bangladesh’s industrial sector, particularly in textile manufacturing. These machines, which shape metal and wood into precise forms, are essential for producing textile machinery components. Over the years, the demand for imported lathe…
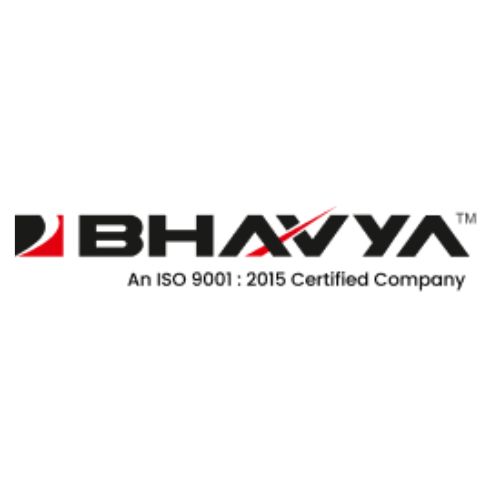
History of Lathe Machine Production in Iran: An Overview
Lathe machines have played a critical role in Iran’s industrial advancement. From the early days of manual metalworking to the adoption of modern precision machining technologies, Iranian cities have experienced a remarkable shift in manufacturing capabilities. This article explores the…
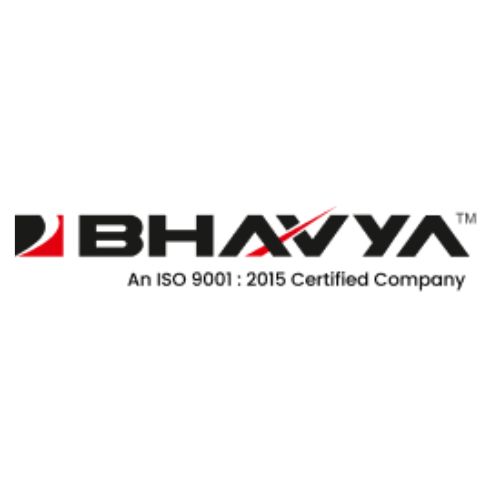
Top Nigerian Industries Adopting Lathe Machines for Advanced Manufacturing
Nigeria’s manufacturing sector is undergoing a significant transformation, with industries rapidly adopting lathe machines to enhance production efficiency and precision. In cities like Lagos, Abuja, Kano, Port Harcourt, Ibadan and Benin City, various industries are integrating CNC lathe machines, capstan lathe…
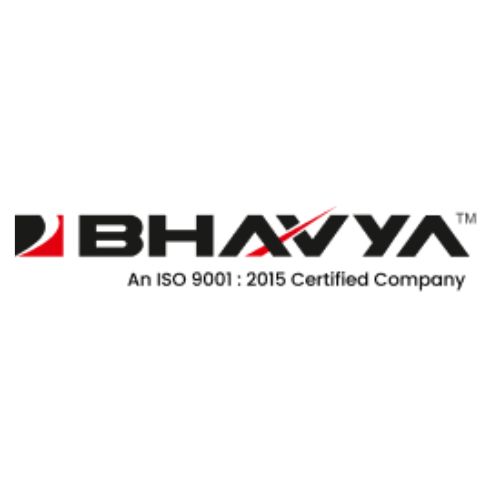
Lathe Machines Impact on Ethiopia’s Expanding Industrial Manufacturing Landscape
Ethiopia’s industrial sector is undergoing rapid transformation, with Lathe Machines playing a crucial role. These machines are used in metalworking, woodturning and precision engineering, making them essential for various industries. From Addis Ababa to Dire Dawa, manufacturers rely on All Gear…
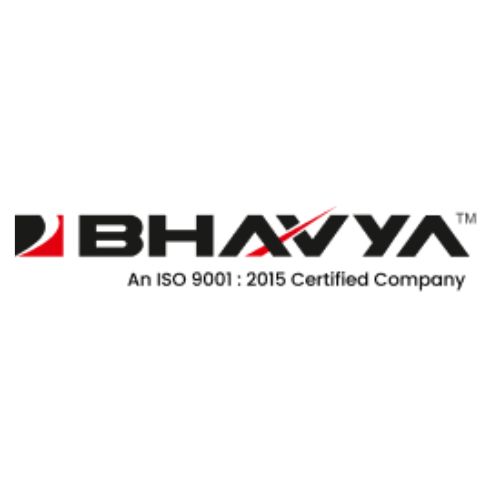
Light Duty All Geared Lathe Machine: Precision Engineering for Light Materials
Introduction Light-duty all geared lathe machines are an essential tool for industries that require precision machining of light materials such as metal sheets, wood sheets, and other lightweight workpieces. Bhavya Machine Tools offers a versatile and reliable light-duty all geared…
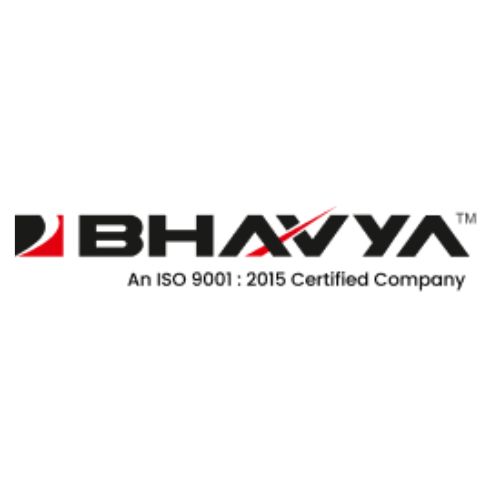
Light & Medium Duty All Geared Lathe Machine for the Gulf Region
Introduction The Gulf region, known for its rapid industrial growth and diverse manufacturing sectors, demands high-quality and efficient machinery to support its booming industries. One such essential piece of equipment is the Light & Medium Duty All Geared Lathe Machine.…
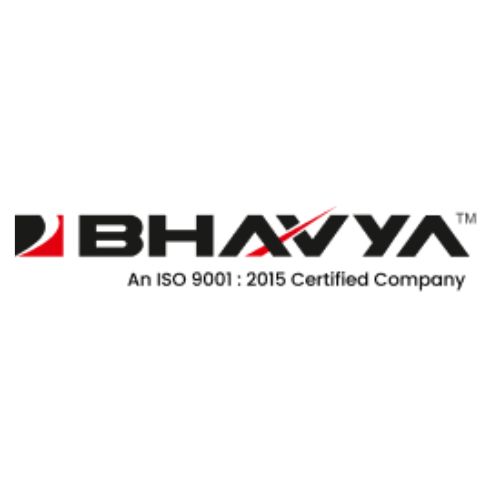
Types and Applications of All Geared Lathe Machines
All Geared Lathe Machines have revolutionized the machining industry, offering versatility and precision. In this article, we delve into the various types and applications of these machines, shedding light on their significance in modern manufacturing. Understanding All Geared Lathe Machines…
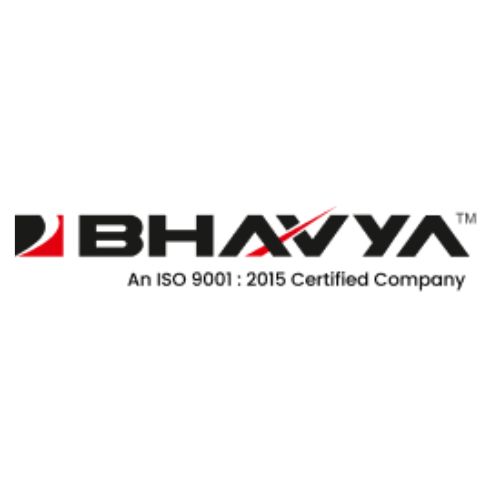
How Lathe Machines Revolutionize Manufacturing Processes?
Lathe machines are mechanical devices used to rotate a workpiece while various cutting tools are applied to shape, cut, or drill it. The workpiece is clamped securely and rotated on its axis, allowing the cutting tools to remove material and…
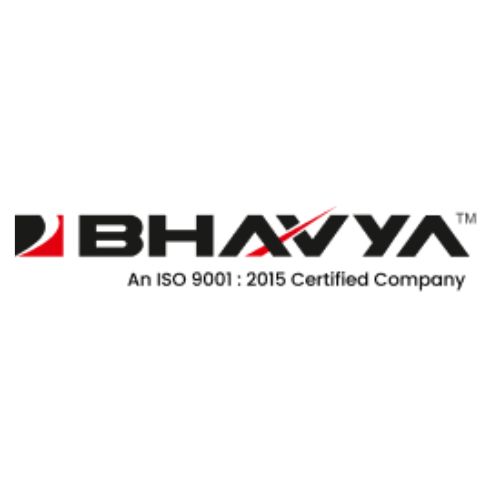
Lathe Machines – The Backbone of Machining Processess – The Backbone of Machining Processes
Lathe machines are mechanical tools used for shaping workpieces by rotating them against a cutting tool. They have been a fundamental part of machining processes for centuries and continue to be widely used in industries such as automotive, aerospace, and…
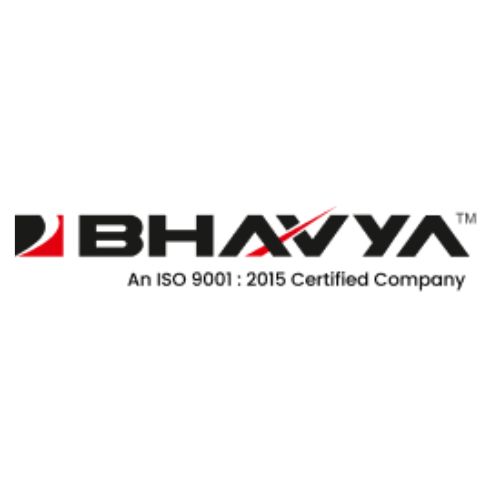
Versatility of Lathe Machines from Woodworking to Metalworking
Lathe machines are essential tools in various industries, providing immense versatility for both woodworking and metalworking tasks. These powerful machines enable craftsmen and manufacturers to shape and manipulate various materials with precision and efficiency. Woodworking Applications Woodworking is one of…
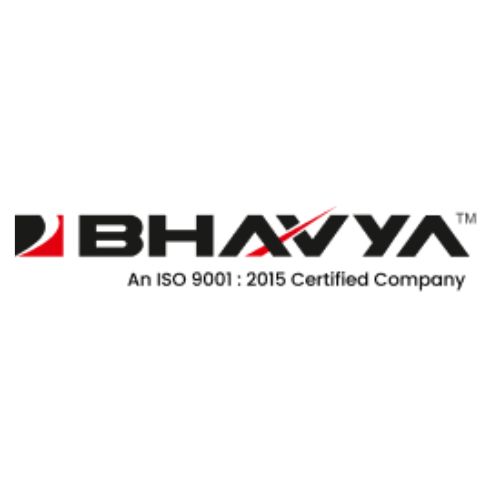
Lathe Machine Market in United Arab Emirates
If you are looking for information on the Lathe Machine Market in the United Arab Emirates, you are in the right place. This article will help you determine the market size and potential opportunities for CNC lathes in the UAE.…
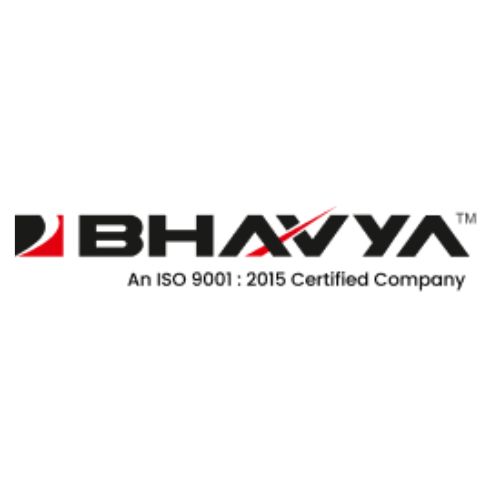
The Lathe Machine Industry in Dubai
In the Middle East and North Africa region, the lathe machine industry is booming. The demand for lathe machines is increasing as more and more companies in these regions need lathes to produce a wide variety of products. A job…
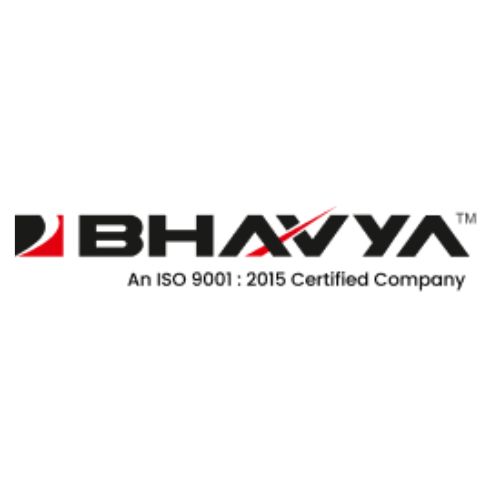
Buying Lathe Machines in Oman
Bhavya Machine Tools is lathe machine supplier to Oman, offers best lathe machine of different types and configurations to its wide customer base all over the world. So, whether you are planning to buy a lathe or are merely thinking…
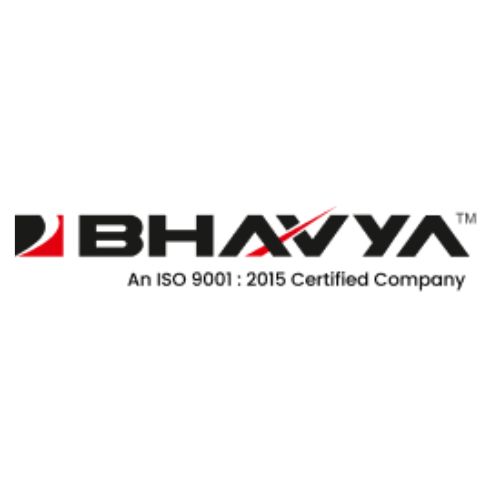
Lathe Machine and Machine Tools Market in Kuwait
During the past five years, the Lathe Machine and Machine Tools market in Kuwait has witnessed a remarkable growth rate. The growth rate of the market is attributed to the growth of the construction and automotive industries. This market has…
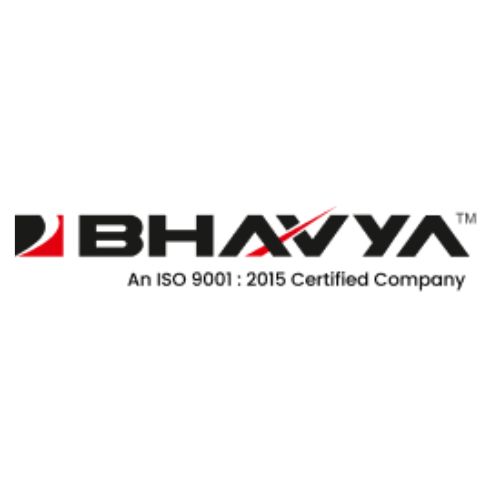
Lathe Machine Market in Bahrain – An Overview
Currently, the Lathe Machine market in Bahrain is experiencing a good growth. This is due to a number of factors, including the increasing demand for machine tools, as well as the growing population of industrial users and the growing construction…
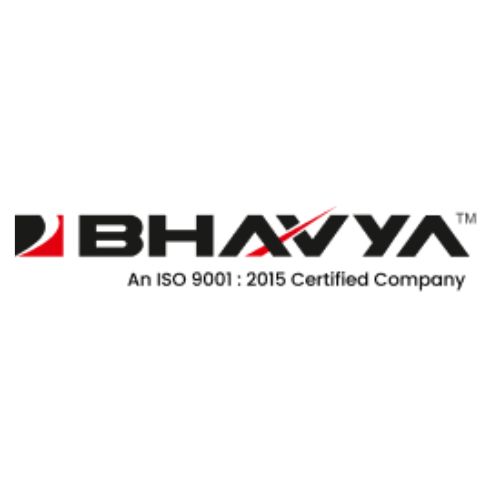
Lathe Machine Demand and Supply in Qatar
Various factors have affected the demand and supply of lathe machines in Qatar. These factors include recent innovations and major events. In addition, there has been regional segmentation. Horizontal Lathe Global Market Currently, the global Horizontal Lathes market is largely…
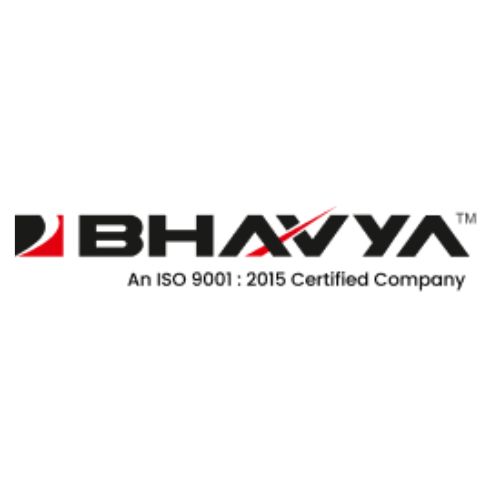
An Overview of DRO Lathe Machines
DRO (Digital Readout) lathe machines are used to measure and record the diameter and radius of workpieces. They are especially useful when cutting slots and features and can serve as a calculator for users. In addition to being useful calculators,…
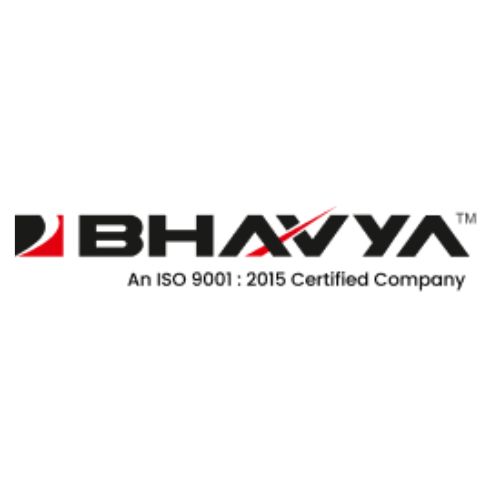
High-Speed Precision Lathe Machine – Features, Functions, & Specification
In this article, we will look at the features, functions, and specifications of the High-Speed Precision Lathe Machine. We will also discuss the price and the specifications. In the end, you will be able to buy the perfect machine for…
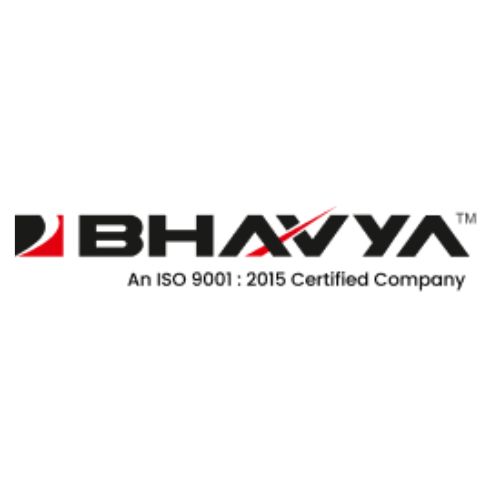
All About Turret Lathe Machine
Turret Lathe Machine is one of the most versatile machines in the industry and can perform a variety of tasks. The machine has a number of unique advantages and provides users with the facility of creating finely tuned lathes for…
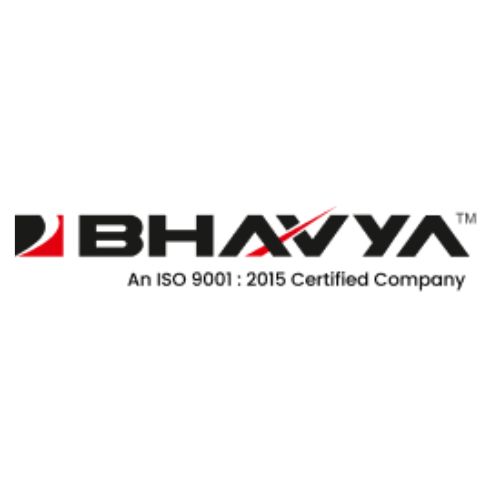
Tool Room Lathe – Flat Bottomed Vs Spindle-Mounted
The general idea of a tool room lathe refers to any machine shop. In general, a tool room lathe consists of a large engine lathe, usually powered by a steam-powered engine, that is set up for higher precision work. A…
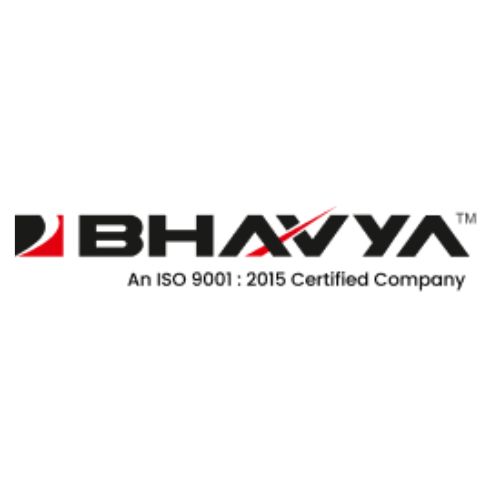
Precision Lathe – Precision Engine Lathes
A precision lathe is an automated lathe used in the manufacturing industry to make intricate, smooth solid objects from just a single piece of material. With complex computer programming, the precision lathe will automatically create a near-finished object without much…
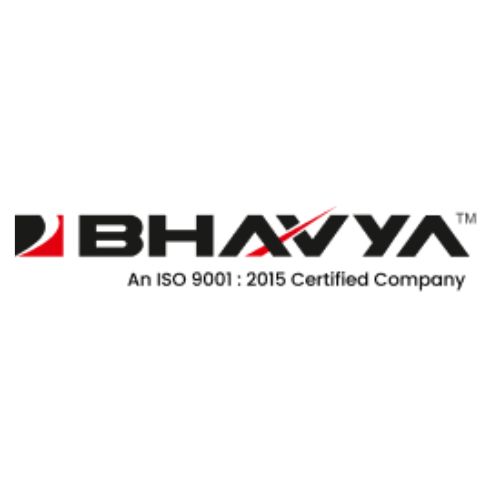
What Is A Hydraulic Lathe Machine?
The hydraulic lathe machine is a type of machine that generates machined movement by the use of hydraulic fluid. This type of machining device uses hydraulic fluid as the main power source, rather than electricity. Therefore, it has been a…
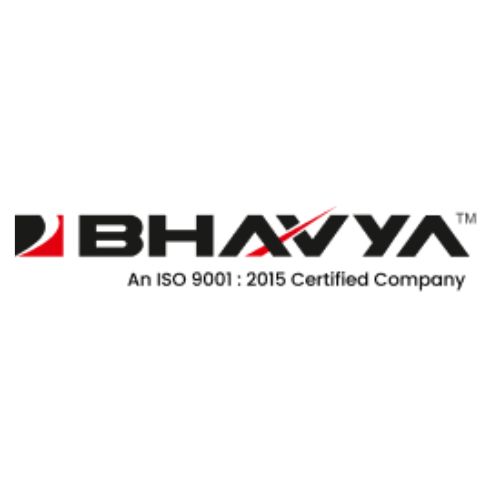
Heavy Duty Lathe Machine & Its Advancements
Lathe machines are used to execute a wide range of tasks. They are essential in various industries such as woodworking, metalworking, ceramic arts, electronics, etc. The machines are also used in the traditional manual industries such as coal mining, petroleum…
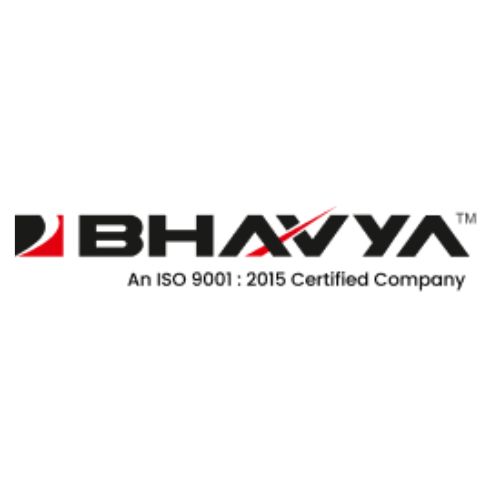
CNC Lathe Machine – Producing Art with CNC Machines
A CNC lathe is a software-controlled machine tool that utilizes state-of-the-art CAD software and mathematical algorithms to manipulate only three-dimension objects using just mathematical equations and computer programs. In simple terms, the CNC machine tool generates a three-dimensional image that…
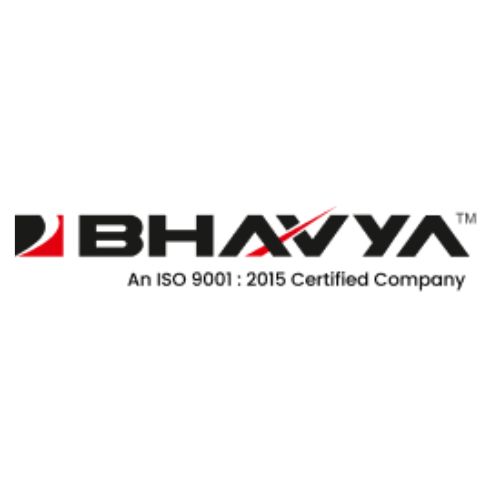
African Market for Lathe Machine
Lathe Machines are widely known as the "Mother of all machine tools". Their uses are spread over a wide range of Industries present all over the world. These applications are applied in almost every sector like food, mining, refineries, power…
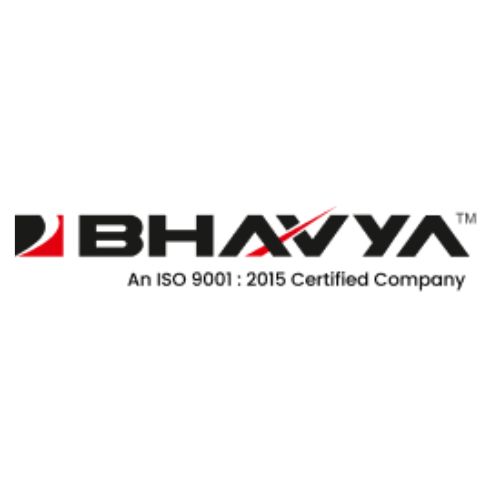
Why Precision Lathe Process is Important for Modern Industrial Needs?
The precision lathe machine is a machinery for precision operation, that is used to create an object by shaping, cutting, and removing its unwanted parts, from a block of material which can be either metal or wood. Purpose of Precision…
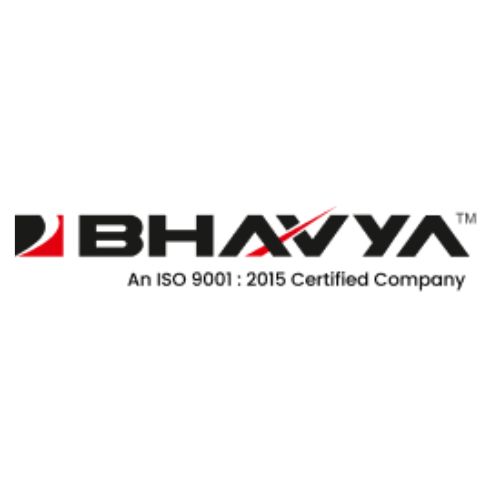
Demand and Supply of Lathe Machines in Different Cities of India
The lathe machine is a machine tool used for producing components that are symmetrical about an axis. Its primary function is to shape metal or wood and its functioning involves rotating the work piece around a stationary cutting tool. What…
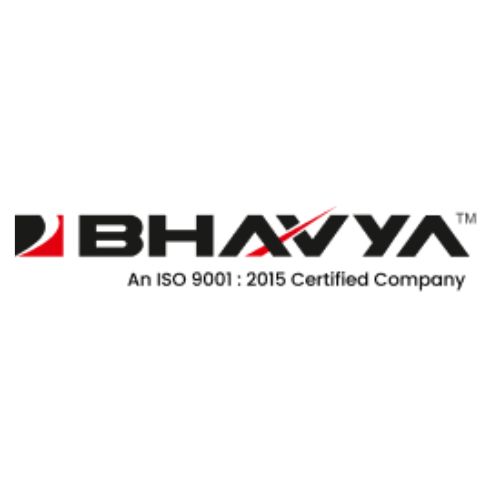
Rising Demand for Different Machine Tools in Industrial Sectors of Punjab
Punjab has emerged as India’s one of the most industrially advanced states. The demand for specialized industrial machine tools has risen significantly over the years in Punjab state, thanks to rapid industrialization and the rise of small and medium-sized businesses.…