Category Archives: Sheet Bending
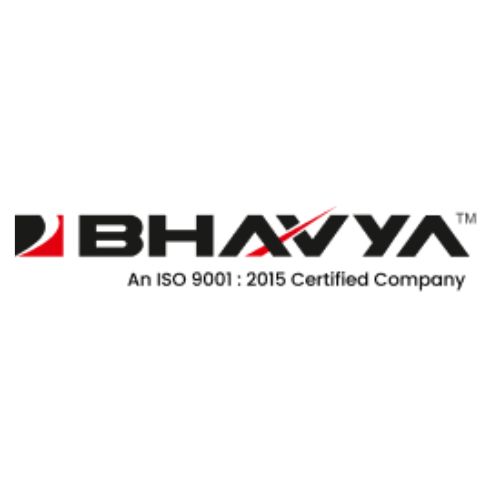
How to Select a Sheet Bending Machine?
If you've ever seen a sheet bending machine, you're familiar with its intricate design. While it looks like a standard workbench, this model comes with a sophisticated automation system. The user-friendly controls of the EasyRoll AI-based CNC software make bending…
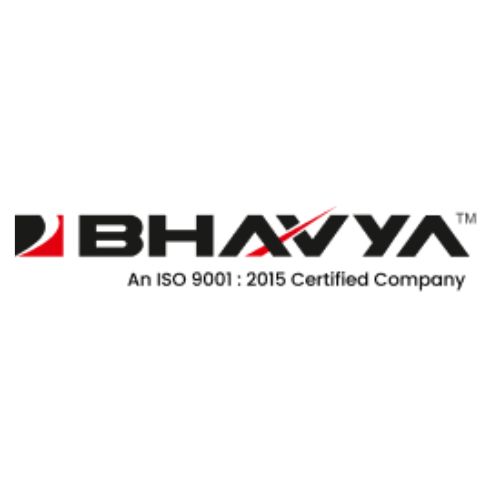
Evolution of Sheet Metal Machine
Today, Sheet Metal Machines are being widely used to perform cut, drill, press and shear on various hardened materials including aluminium, brass, copper, steel, tin, nickel, etc. These operations help reform the shape and size of the materials. Uses of…
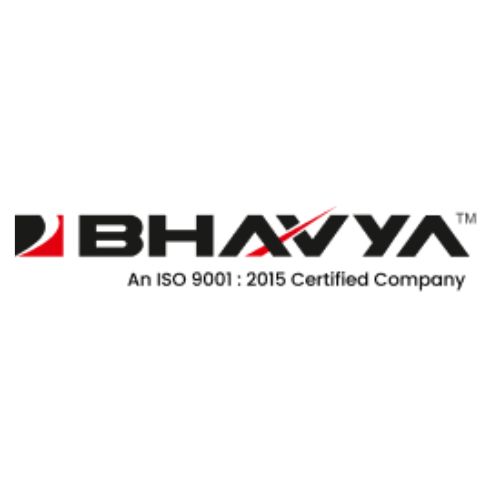
Produce Air Conditioning Systems Using Sheet Bending Machine
Introduction Air cons (AC) are widely used in residential, commercial and industrial systems to actively pump out heat and maintain a predetermined temperature and humidity. They create an artificial environment which suitable for machines, human and agricultural produce. Air conditioning…
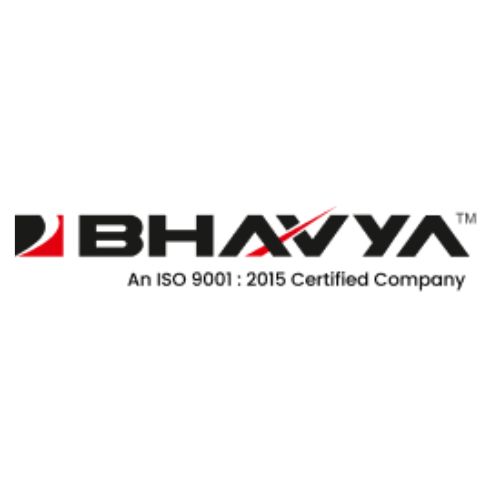
The Sheet Bending Machine in Iron Sheet Manufacturing
Introduction to Sheet Bending Machine Iron and steel are the most common fabrication material in manufacturing and repair shops. They are widely used in construction, assembly, vehicle manufacture, processing and packaging industry. Large metal plates are produced in form of…
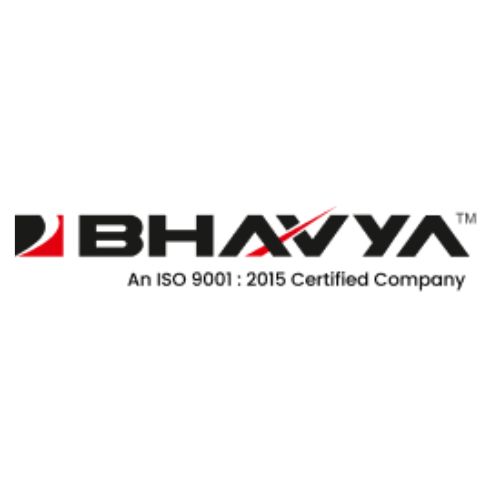
Channel Bending For Making Door and Window Frames
Creative Works using Metal Components Metal materials are also applied for making creative ideas like art work, designer steel doors, window frames, etc. However, range of bending operation varies when compared to customary ones. The type of reforming that suits…
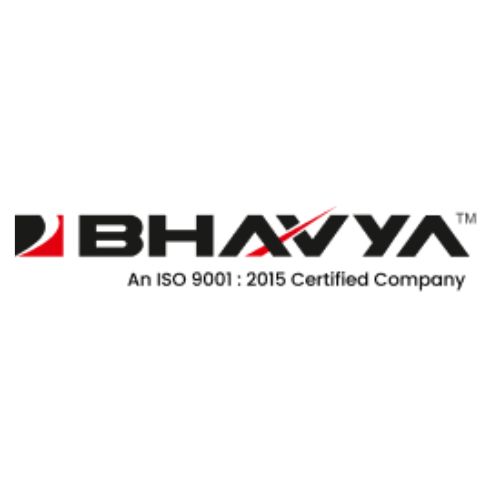
Cost Effective Bending Methods Suitable for Sheet Metal Works
How to spend little for bending? Deforming work materials into the determined dimension is quite expensive. If there is change in dimension, it leads to wastage and loss. In addition, manual bending process with the help of compact tools is…
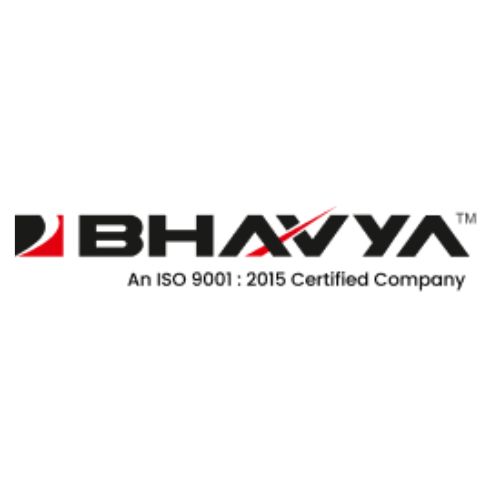
Metal Deformation Requirements in Manufacturing Sectors
Why a change in Geometry is required? Manufacturing of metal components involves application of metals as raw materials. When it comes to producing structural gadgets, a lot has to be done with work materials. Therefore, change in geometry of raw…
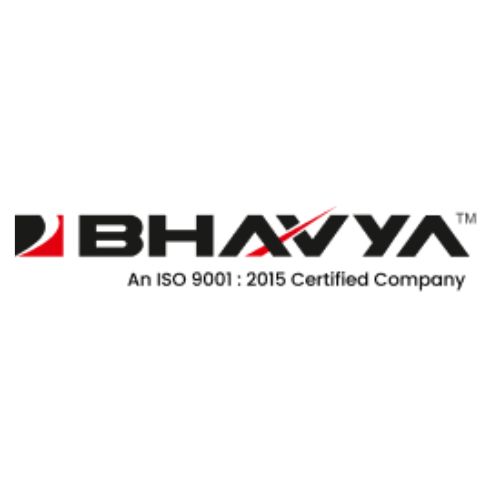
Learn about the Industrial Preference of Bend Angle and Bend Size in Sheet Bending Equipment
One Machine to Handle Variety of Metals Steel, brass, aluminum, copper, etc. these metals can be converted to variety of shapes even when they are existing in varying thicknesses. Important Aspects to be looked for in Sheet Bending Equipment Starting…
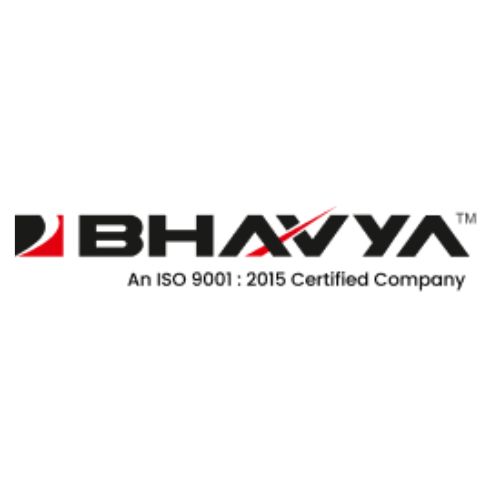
How Sheet Bending Machine is Customized by Manufacturers to Handle Variable Thicknesses of Sheet Metals?
The peculiarity of sheet bending machine Among the workshop devices, the aspect of bending metal sheets to the desired dimension can be done only with the help of specific equipment. A drilling or milling device cannot be depended on for…
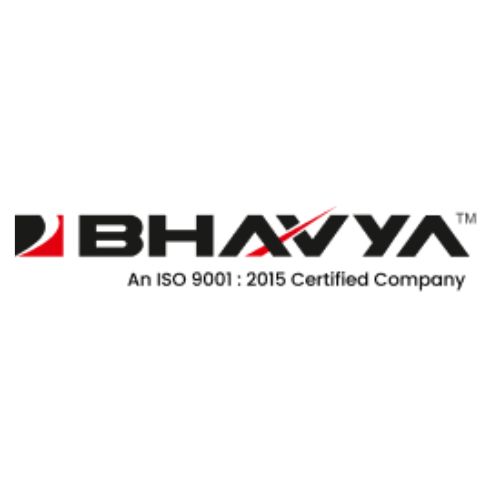
How Bending Process Influence The Work Piece to Obtain Stiffness
Facts behind Bending Work Piece Metals Metal work piece and subsequent machining process done over them had been very tough as most of the times the shaping of metal work piece was completed with manual assistant. However, the rate of…
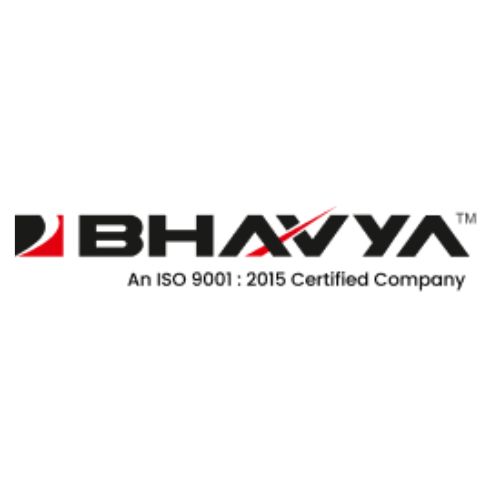
Does Sheet Bending Tools Relatively Reduce Man Power Assistances?
Sheet Bending Process Cost during Earlier Days The bending activity over metal sheets is an imperative machining work in several industries with which a metal work piece sheet is changes in its geometry without any change being made in its…
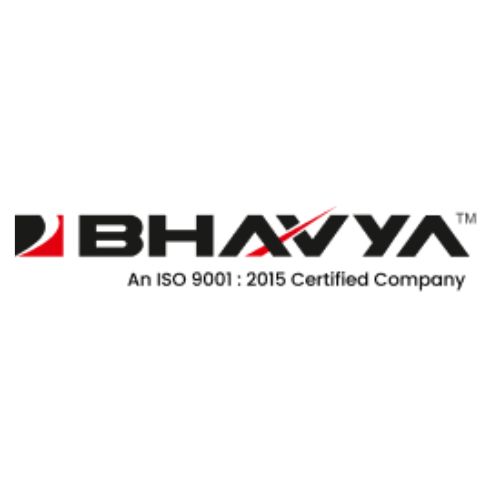
Why Sheet bending Machine Still Remains The Integral Machine tool?
Importance of sheet bending machine as a tool It is important workshop equipment, especially when it comes to engineering works like metal shaping and cutting. Workshop equipment industries worldwide are focusing towards designing new types to handle machining process with…
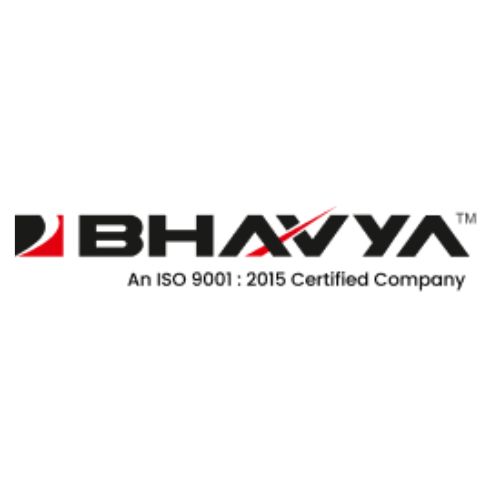
Features of a Sheet Bending Machine
With a sheet bending machine you can bend a sheet of metal. The whole sheet can be placed on the surface and bent according to your requirement to make metal structures. Pressure is applied to the metal sheet in order…
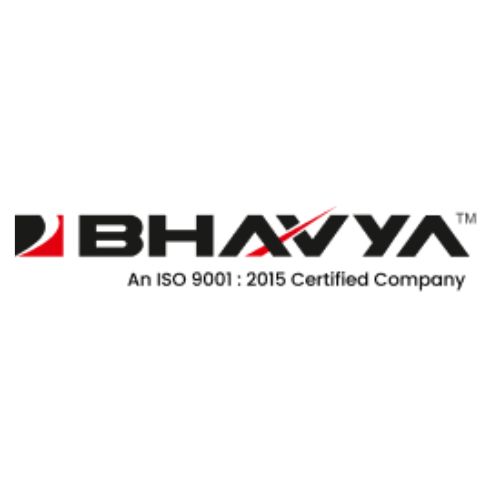
Sheet Bending – Press Brake, Power Press
Sheet Bending Process and Machines Sheet bending is a process of metal forming through which metals are bent into desired forms. In a sheet bending process the metals are casted into the required form by exerting a strong force on…
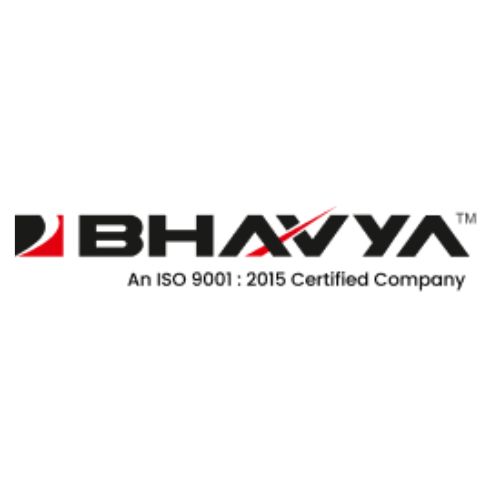
Sheet Bending Machine, Types of Sheet Bending Machine, Applications of Sheet Bending Machine
Sheet Bending Machines - Types and Applications Metals need to be casted into different shapes and sizes for various applications in different industries. They are normally very hard and therefore could not be bent or shaped easily. For bending and…
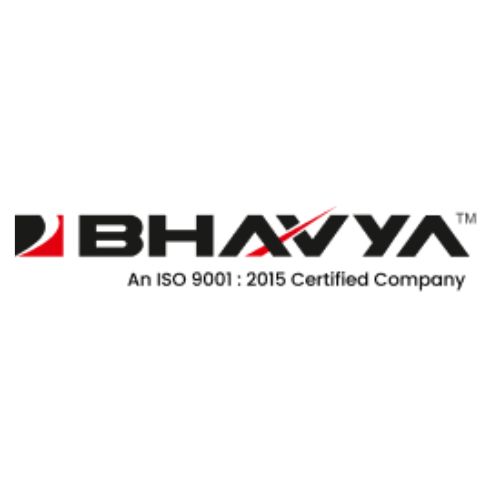
Sheet Bending, Sheet Bending Machine
Popular Sheet Bending Machines The act of bending metals into desired shape can be termed as sheet bending. In a normal sheet bending process force is applied on the metal causing it to deform in a particular direction and this…
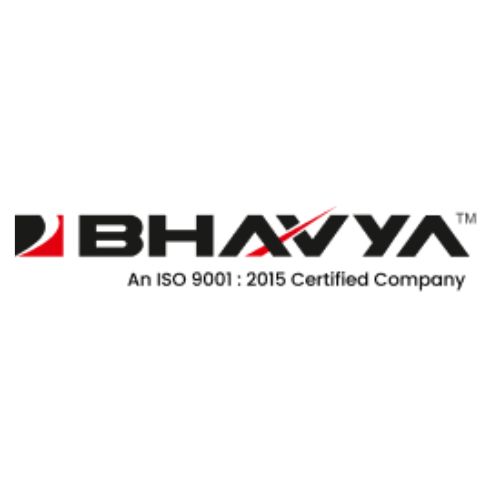
Sheet Bending with Press Brake
Sheet Bending with Press Brake Different kinds of machines are employed for sheet metal forming tasks in industries like lathe, sheet bending, power press, press brakes etc. It is a special kind of sheet bending machine that is designed to…
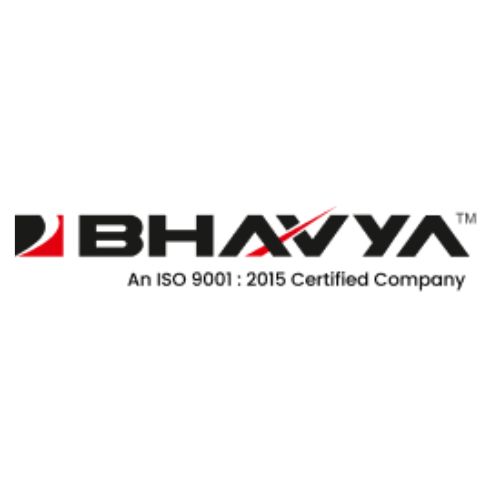
Importance of Machine Tools for Milling Machine, Sheet Bending Machine, Lathe Machine
About Machine Tools and Their Importance The term tool refers to the category of machinery which is generally powered electrically or hydraulically or by any means other than human effort. These are widely used to make manufactured parts or components…
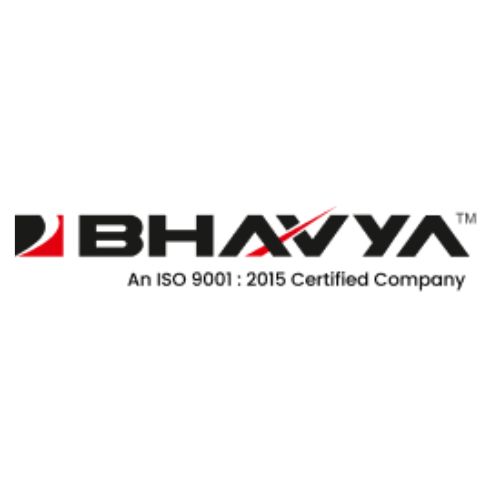
Sheet Metal Machine – Types of Sheet Metal Machines, Applications of Sheet Metal Machines
Sheet Metal Machine Machine tools are the devices used to cut, drill, press, and shear the hardened materials into specific forms. Metal Forming Machine are used to cut, press, bend and form sheet metal into different shapes and sizes. Various…
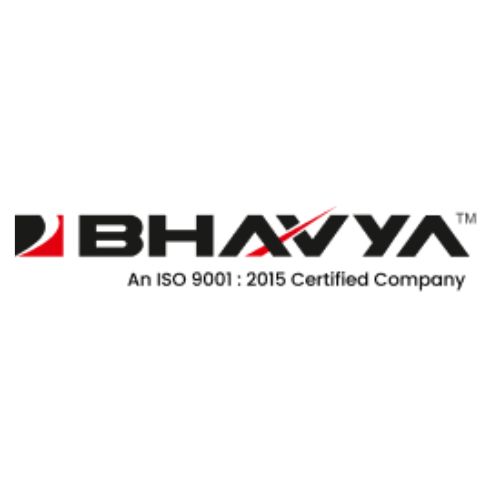
Sheet Bending – Hand Operated Sheet Bending Machine, Flat Sheet Bending Machine
Sheet bending machine is used to bend or straight the metal sheets and strips. Hand operated sheet bending is very much useful for sheet metal bending with accuracy. Many other features along with bending are punching, cutting and sheering. These…