Category Archives: CNC lathe
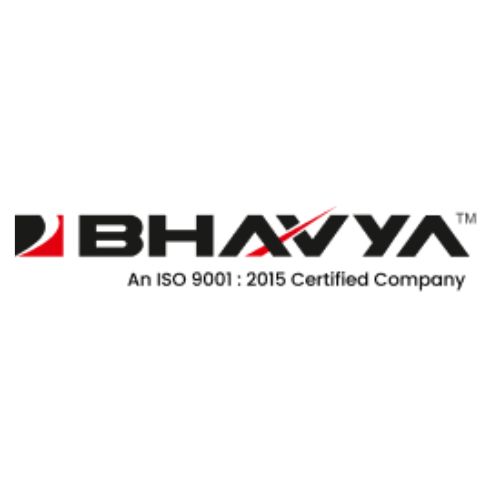
CNC Lathe Market in 2025: From Desktop Models to Heavy-Duty Machines and Smart Controllers
The CNC lathe market in 2025 is defined by rapid technological advancement, increased demand for machine versatility and a growing emphasis on digital integration. For manufacturers, engineers, machinists and procurement teams, understanding the evolving landscape is crucial to maintaining competitive…
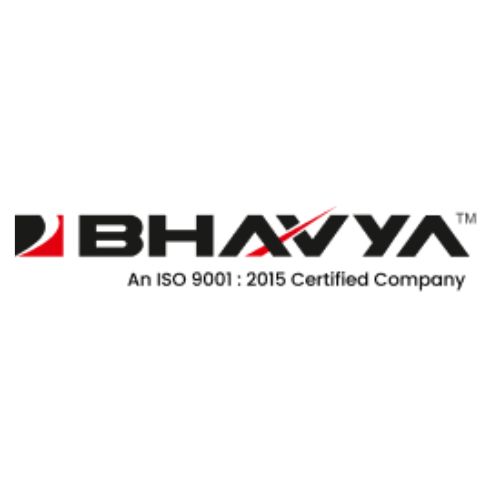
Analyzing Demand for CNC Lathes in Nigeria’s Expanding Automotive Components Sector
Nigeria’s manufacturing sector is undergoing a transformation, driven by industrial diversification and a strategic push to localize the production of automotive components. As demand for vehicle parts rises-fueled by increasing vehicle ownership, economic expansion and a shift toward self-reliance-the role…
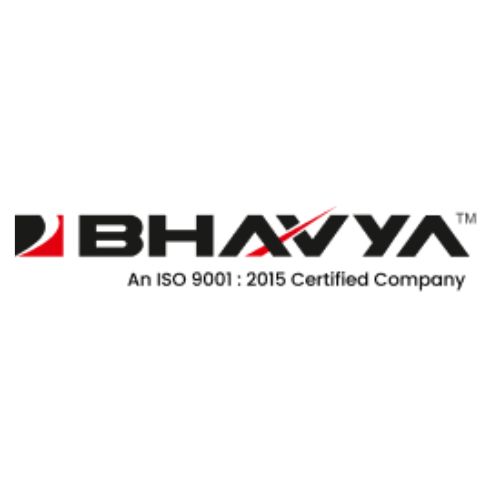
The Rising Demand for Lathe Machines in Bangladesh’s Construction and Infrastructure Sector
Bangladesh is undergoing rapid industrial and infrastructural growth. From bridges to high-rise buildings, the country is investing heavily in development. Lathe machines play a key role in shaping and machining metal parts for these projects. Cities like Bogra, Jessore, Tangail and…
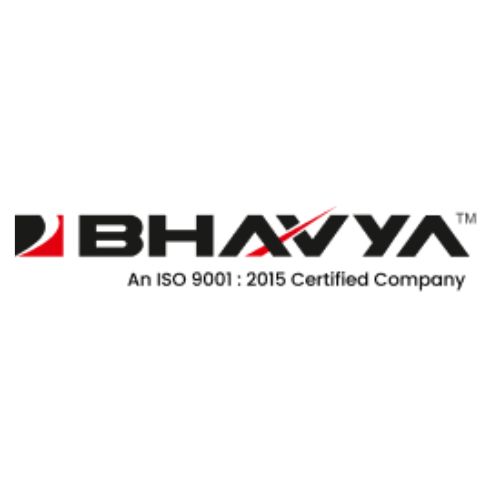
Lathe Machine Technology Impact on Bhutan’s Renewable Energy Industry
Bhutan is emerging as a leader in renewable energy, with its vast hydropower potential and growing interest in solar energy. Lathe machines play a critical role in manufacturing and maintaining components for turbines, solar panel structures and other renewable energy…
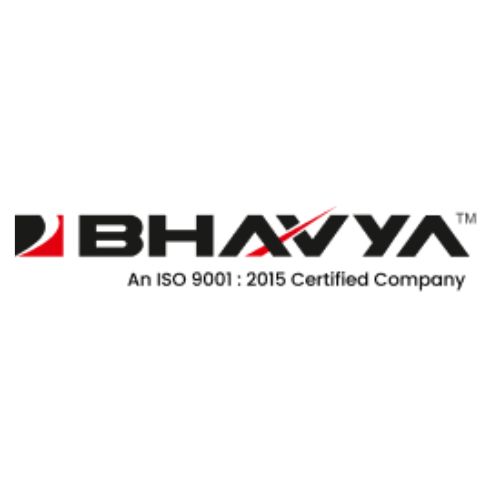
Challenges of Using Lathe Machines in the Maldives’ Limited Manufacturing Environment
The Maldives is globally recognized for its tourism industry, but its manufacturing sector remains small due to geographical and infrastructural limitations. Despite a rising demand for industrial machinery, using Lathe Machines in Maldives presents significant challenges. Cities like Villingili, Ungoofaaru, Hinnavaru, Naifaru,…
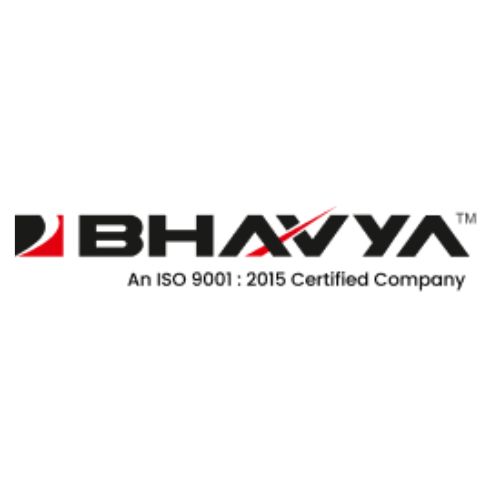
Lathe Machines: Transforming Local Manufacturing in Accra’s Industrial Hub
Accra has become a hub for industrial growth, with increased demand for precision machining across various sectors. From automotive workshops to heavy metal fabrication, businesses require accurate and efficient equipment to meet industry standards. Lathe machines have become an essential tool in…
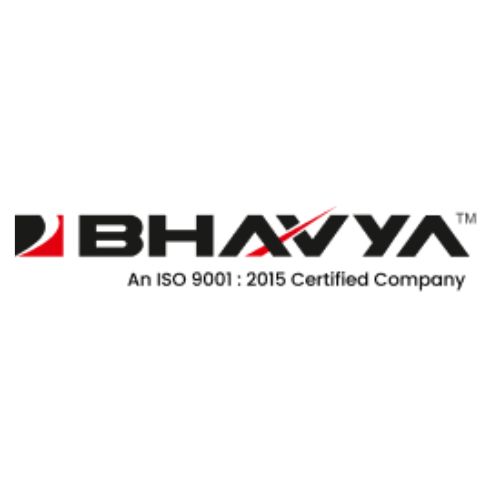
Lathe Machines in Ghana’s Oil and Gas Sector: The Need for Precision Manufacturing
Ghana’s oil and gas industry requires high-precision equipment to ensure efficiency and safety in drilling, transportation and refining operations. Machining plays a critical role in manufacturing pipeline components, drilling tools, flanges and pump systems. Without precise engineering, oil extraction and…
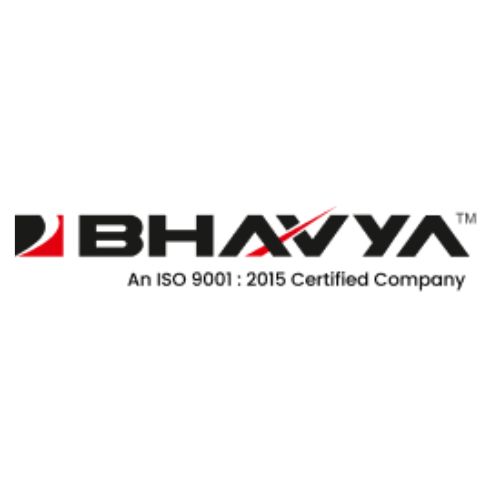
The Role of Lathe Machines in Iran’s Growing Aerospace Industry
Iran’s aerospace industry is undergoing rapid transformation, with increasing investments in aircraft production, space exploration and defense aviation. As the country strengthens its domestic aerospace capabilities, Lathe Machines in Nigeria, including Universal All Geared Lathe Machines, are playing a vital role…
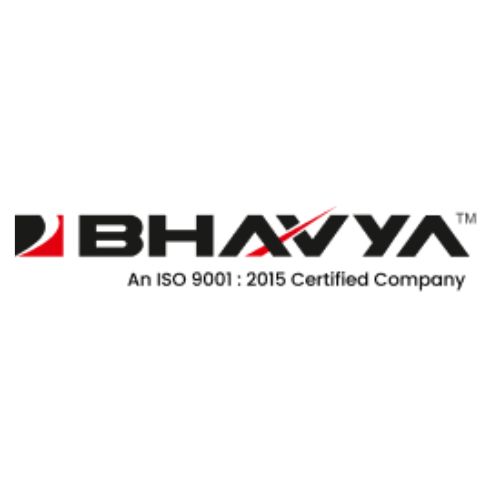
The Growth of Lathe Machine Technology in Nigeria’s Manufacturing Sector
Lathe machines are at the heart of Nigeria’s industrial development, supporting road construction, infrastructure projects and economic expansion. These machines play a crucial role in metal fabrication, equipment repair and precision machining, ensuring the durability and efficiency of infrastructure projects…
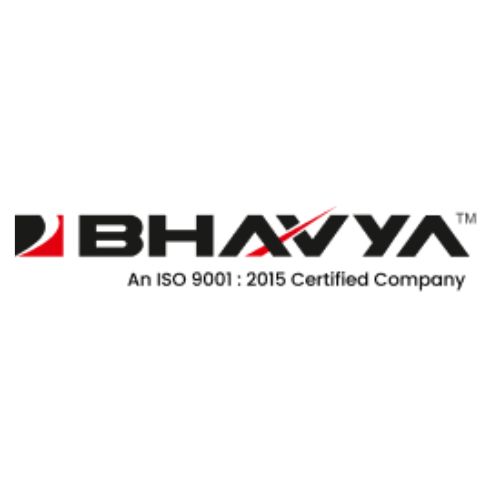
How Lathe Machines are Supporting Ethiopia’s Road Construction and Infrastructure Projects?
Lathe machines play a key role in Ethiopia’s infrastructure development. From shaping metal components for bridges to fabricating precision parts for road construction, these machines are essential in manufacturing durable and efficient construction materials. Cities like Asella, Nekemte, Woldia, Gambela,…
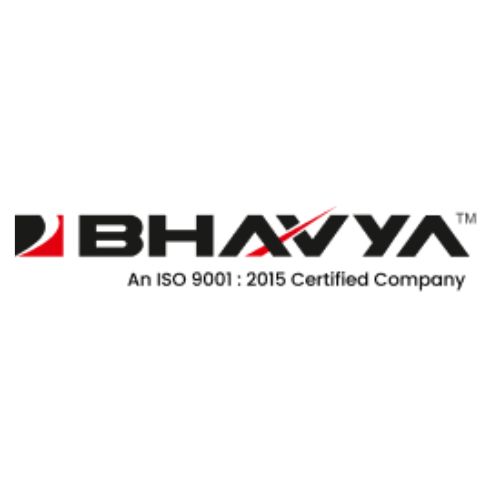
The Evolution of Lathe Machines in Bangladesh’s Textile Industry
Lathe machines have played a transformative role in Bangladesh’s industrial sector, particularly in textile manufacturing. These machines, which shape metal and wood into precise forms, are essential for producing textile machinery components. Over the years, the demand for imported lathe…
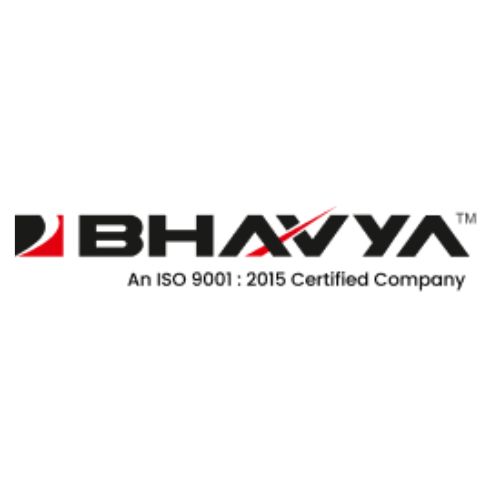
CNC Lathe Machines in the UAE: Revolutionizing Precision Engineering
Introduction CNC (Computer Numerical Control) lathe machines have become a cornerstone of precision engineering across industries. In the UAE, a country that is rapidly evolving as a hub for advanced manufacturing, the demand for high-tech machinery like CNC lathes is…
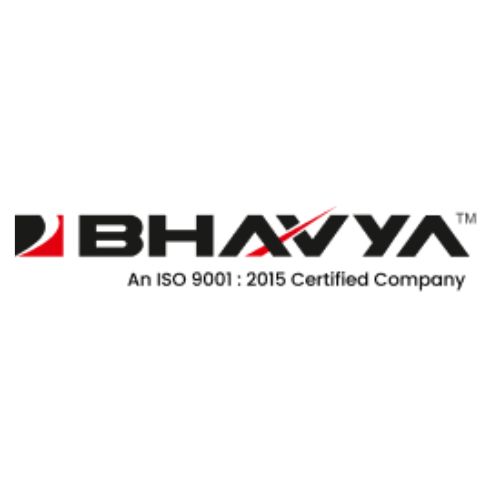
Enhancing Precision and Efficiency with Flat Bed CNC Lathe Machines in Dubai
Introduction Dubai, a bustling hub of innovation and industry, demands cutting-edge technology to keep pace with its rapid growth and diverse manufacturing needs. Among the essential machinery that supports Dubai's industrial sector is the Flat Bed CNC Lathe Machine. Bhavya…
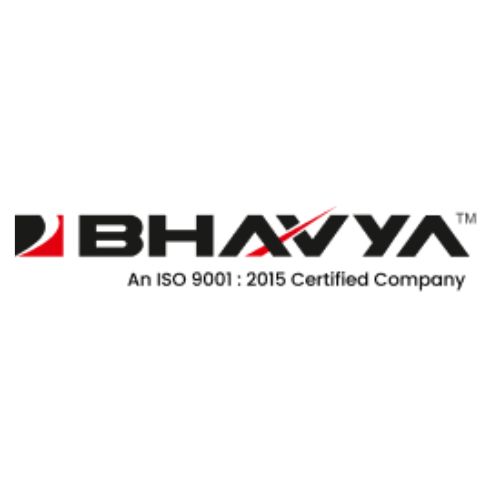
Realizing Industry 4.0: Integrating CNC Lathe Machines into Europe’s Smart Manufacturing Systems
The evolution of Industry 4.0, marked by the integration of digital technologies and smart systems into manufacturing processes, is reshaping industries across the globe. In Europe, the convergence of innovation and automation is particularly evident in the integration of Computer…
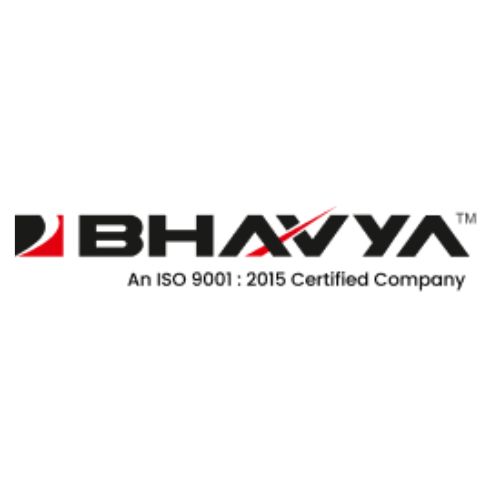
How CNC Lathe Machines are Redefining European Manufacturing Networks?
The concept of supply chain resilience has taken center stage in the modern business landscape, with industries seeking ways to mitigate risks and ensure uninterrupted operations. In European manufacturing, the integration of Computer Numerical Control (CNC) lathe machines is emerging…
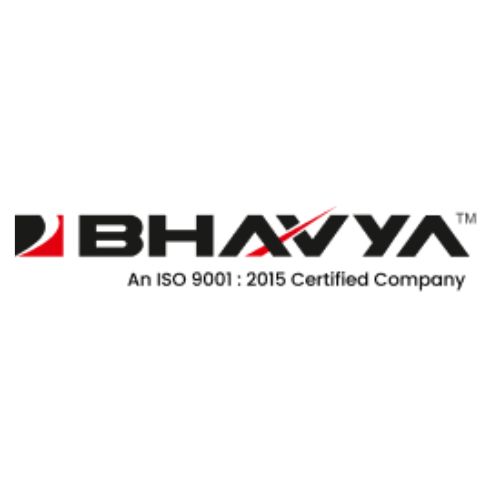
Bhavya Machine Tools at EMO Hannover 2023 – Exploring New Horizons
In the dynamic realm of manufacturing, Bhavya Machine Tools has solidified its position as a pioneering Indian Machine Tools Manufacturing Company. With a steadfast commitment to innovation and quality, the company has set its sights on a remarkable venture -…
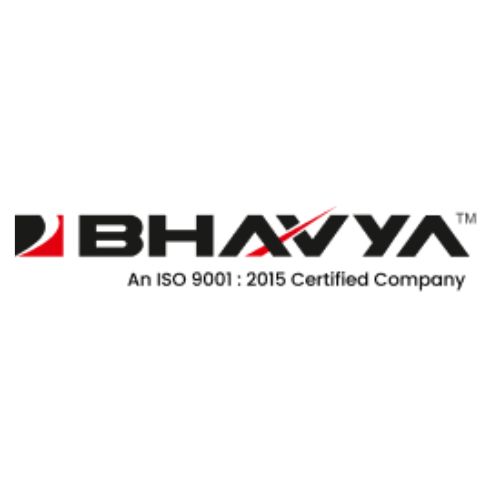
The Future of CNC Lathe Machines
In recent years, the manufacturing industry has witnessed significant advancements in technology, leading to increased efficiency and productivity. One such technological marvel that has transformed the manufacturing landscape is the Computer Numerical Control (CNC) lathe machine. With the ability to…
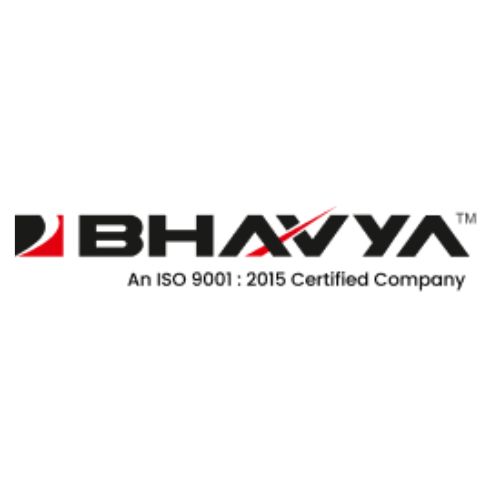
CNC Lathe Machine – Global Demand and Supply
The global CNC lathe machine market is highly fragmented with a large number of regional and local players. The key players in this market like Bhavya Machine Tools are continuously developing new products to meet the needs of the rapidly…
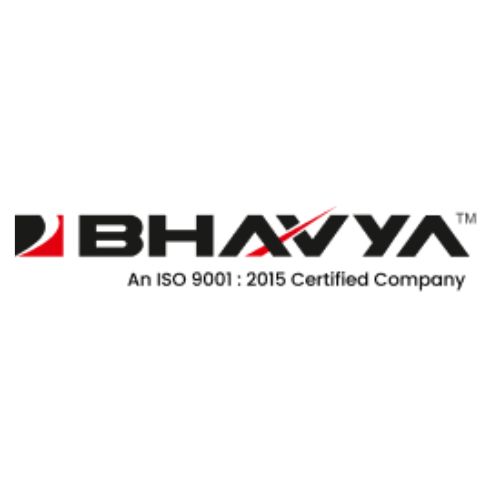
CNC Lathe Machine Market in USA and Europe
The article includes the demand and application for CNC lathe machines, as well as the micro and macro market trend analysis. It also identifies key players, the competitive landscape, and trending innovations in the CNC lathe machine market. It will…
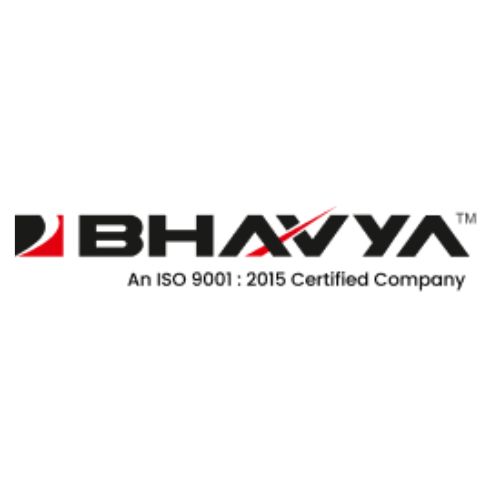
A Beginner’s Guide to Buying a CNC Lathe Machine
Before you buy a CNC Lathe Machine, it is important to learn about the different kinds. Different machines have different axes, and using different axes allows you to make parts of different sizes and shapes. You will also need to…
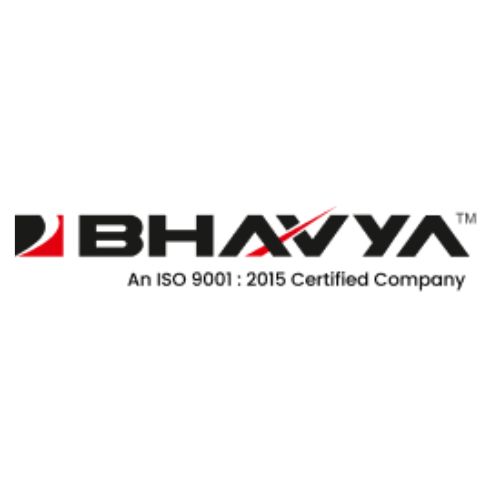
CNC Slant Bed CNC Lathe
The slant bed CNC router is a high-precision, high-volume automated machine tool. Equipped with a multiple-station power source or station, this machine tool has an exceptionally wide scope of operation, able to process curved cylinders, horizontal cylinders, flat cylinders, curved…
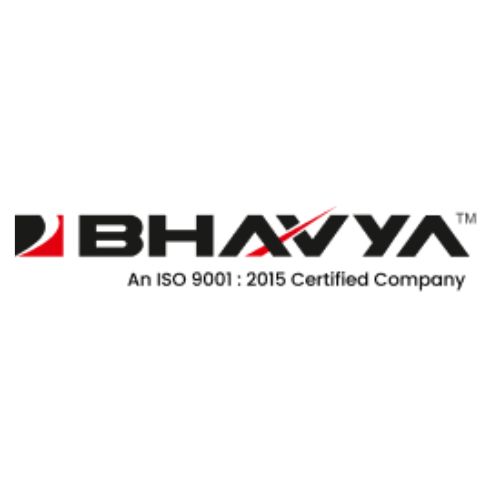
CNC Lathe Machine – Producing Art with CNC Machines
A CNC lathe is a software-controlled machine tool that utilizes state-of-the-art CAD software and mathematical algorithms to manipulate only three-dimension objects using just mathematical equations and computer programs. In simple terms, the CNC machine tool generates a three-dimensional image that…
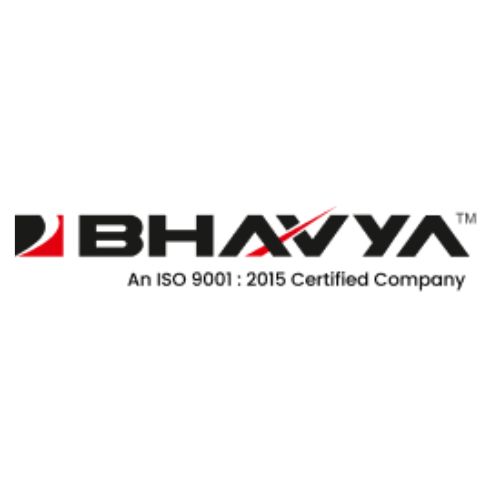
Tool and Cutter Grinding Machine for Precision Machining & Tooling
The need for precision machining and tooling became indispensable when computers were first used in factories and later in the machining process itself. The development is further complemented by the growth of aerospace and automotive industries thereby compelling the need…
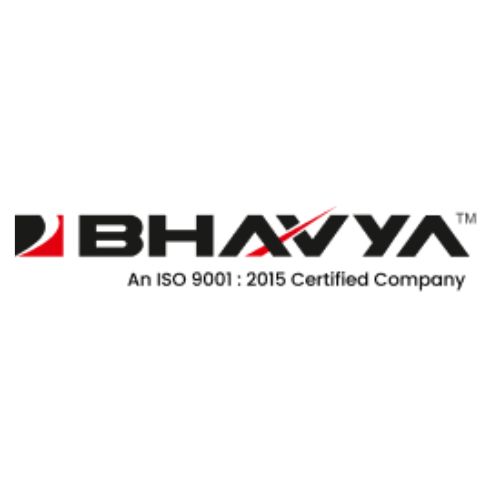
Latest Advancements in CNC Machining Center
Any CNC milling or drilling machine is referred to as a CNC machine center. There machines tend to include an automatic tool changer along with a table to clamp the workpiece. The way it works is that a tool rotates…
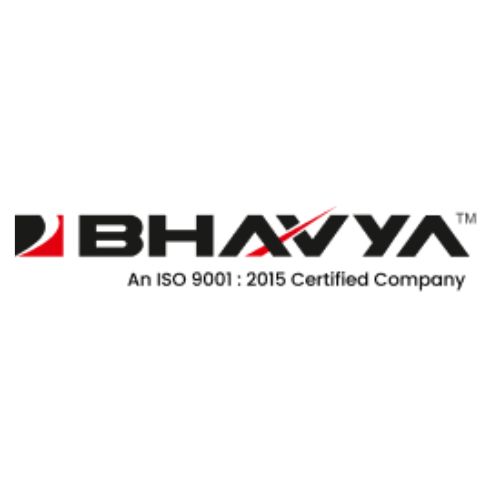
CNC Turning Machine: Understanding its Component and Features
Human cravenness for perfection with less effort has made wonders in economy. Everyday everything is going smart just like a mobile phone, machineries in manufacturing house are also adopting advanced technologies to serve the requirements of mass production. Nowadays, most…
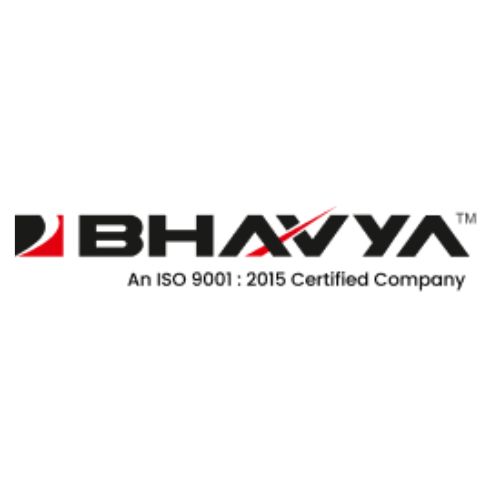
Machining Technology Developments Have Changed the Manufacturing Landscape
Recently, the machine tools industry is enjoying unprecedented surge in demand worldwide. To the surprise of many manufacturers, the output is still unable to satisfy this demand. There have been certain areas of the machine development and innovation that have…
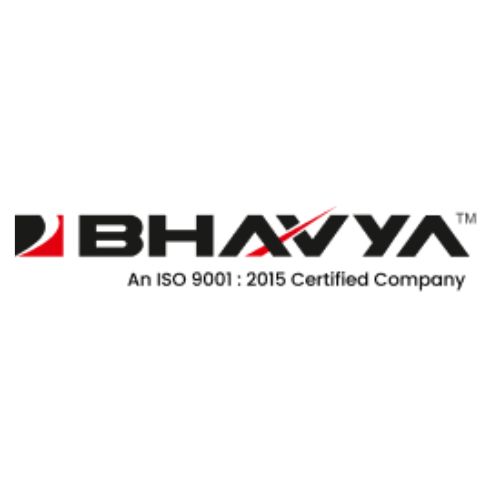
CNC Lathe Machine – Wide Range & Product of Excellence
The lathe machine has been well described as the mother of all metal shaping processes. The computer Numeric controlled lathe has taken metal shaping a notch higher by making it possible to machine metal parts in an automated process, thus…
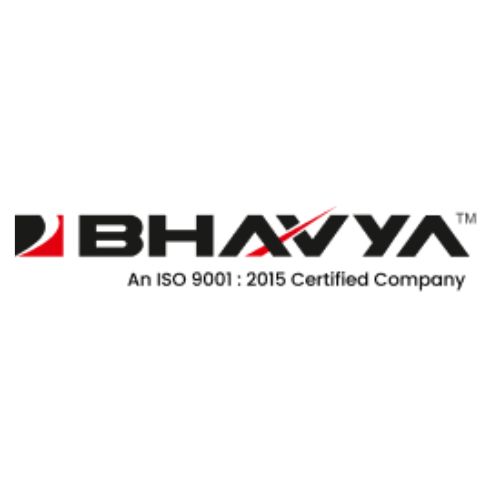
CNC Machining Center, Slant Bed CNC Turning, Drilling-cum-Milling, Re-sharpening Machines
CNC Machining Center The available models for CNC Machining Center include DL – MH series and the TD Series for drilling and tapping centers. The CNC machines are able to guarantee long term reliability and efficiency through sturdy construction, high…
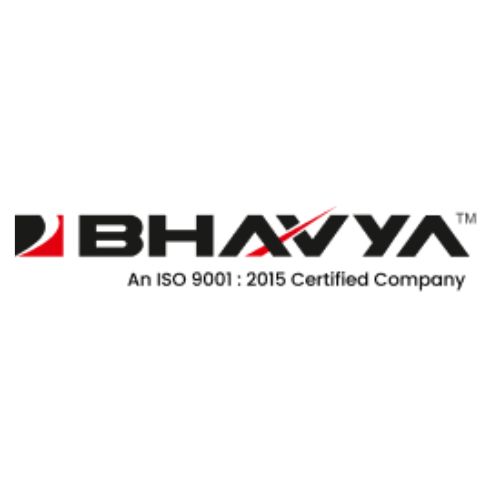
Use of Specialized and CNC Lathes in Education and Training Institutions
Introduction Lathes are referred to as the mother of all machines due to the numerous engineering functions they perform and their application in nearly all industrial sectors. As the proverb goes, there is profit in all hard work; lathes are…
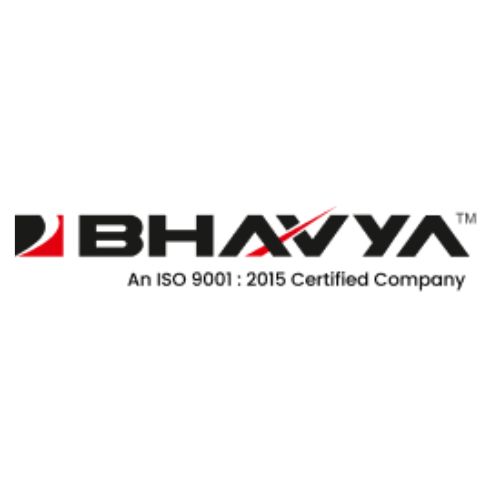
All About CNC workshop Machineries
Automated Operation Features in Workshop Machineries Machines that are applied to carry out critical core engineering works are termed as workshop components. These components were in use since several years back; however, with the advent of designing machines with computer…
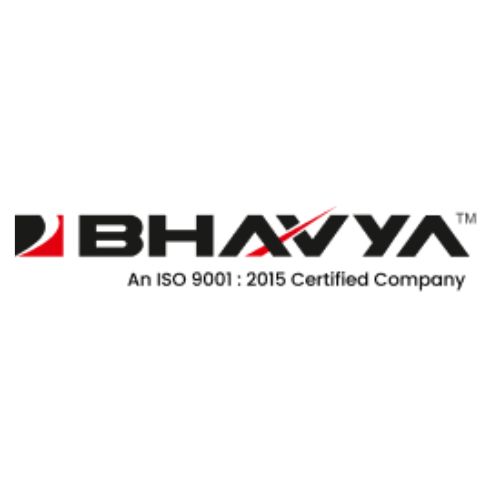
Multiply Your Investment Revenue with CNC Lathe Machine
CNC Lathe for Higher Performance and Productivity CNC lathe is a revolutionary invention for the machining processes. Though this is relatively expensive than bench and table mount models, yet while comparing the performance and productivity. More Productivity in less Timing…
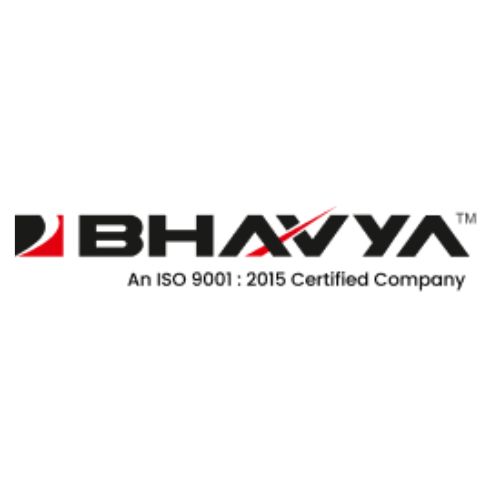
Perform Mechanical Operations on Shafts, Pipes and Other Materials Using Advanced Lathe Machines
The lathe machine is one of the most utilized tool in the world. They have developed overtime from simple to more sophisticated Computer Numerical Control (CNC), turret, capstan, all geared among others. They are widely used in mechanical workshops, automotive…
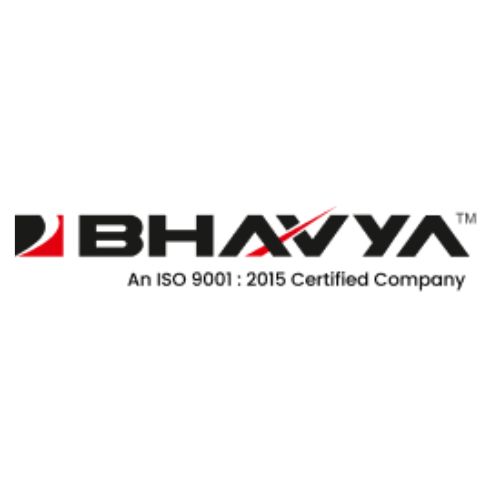
Find out the Machining Differences in Flat Bed and Slant Bed Imported Lathe
Understanding the Lathe device and its functionality A Lathe Machine is a suitable machining component with which tough work pieces can be shaped easily. It is widely used in industries for shaping, cutting, turning and grooving a range of work…
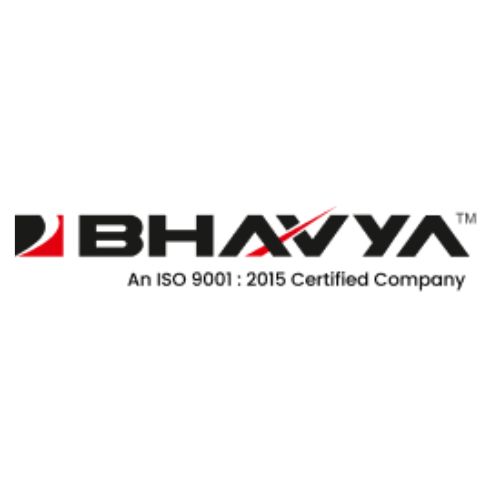
Differences between Slant Bed and Flat Bed CNC Lathe Machines
Introduction to CNC Lathes and significance of CNC Lathe equipment is one of the workshop machineries that can be used for a range of machining purposes such as shearing, sanding, turning, drilling, shaping, etc. A lathe works for different types…
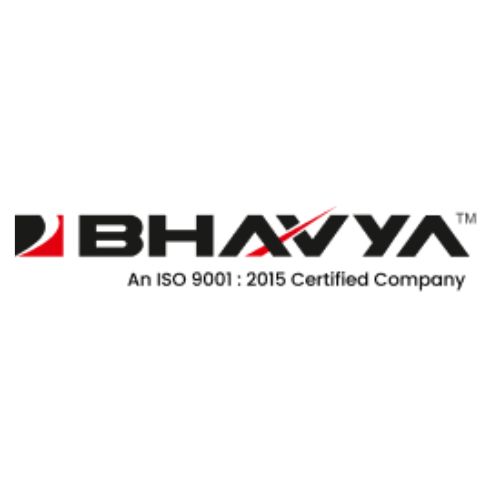
CNC Lathe Machine Range for Multipurpose Machining
The lathe is a multipurpose machine tool; that rapidly rotates the work piece along its axis to perform various tasks like cutting, shaping, drilling, turning, sanding etc.; in order to create a symmetrical object. Nowadays, the latest manufacturing machines use…
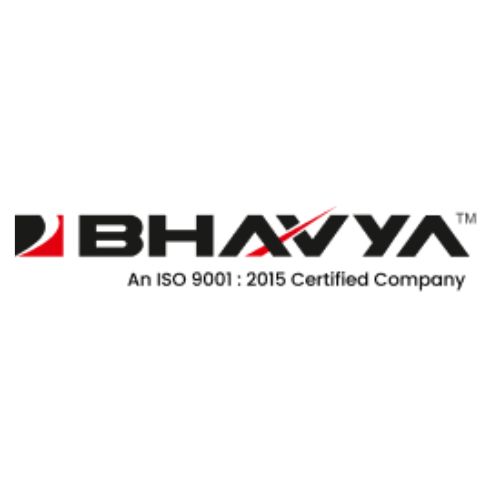
Lathe Machine Operations
Nowadays, the tool room work and workshop machine activities; are done by repairers or through suitable lathe tools. A lathe is a tool utilized to perform various functions like turning, cutting, drilling, grooving, knurling, parting, threading etc. They are used to produce accurate products made from…
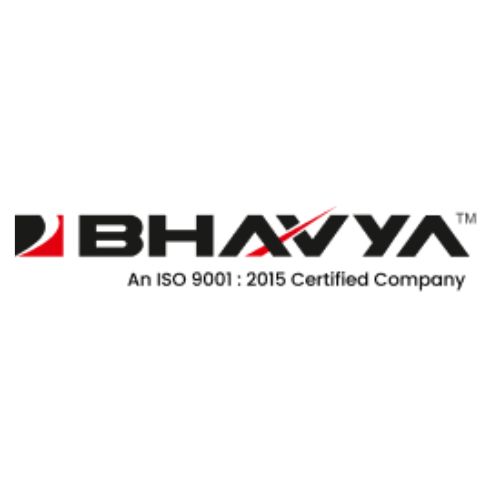
Exclusive Range of Machine Tools from Bhavya Machine Tools
We present variety of tools used in various standard and critical industrial applications. Some of the widely used industrial equipments are lathe, drill, tool room, sheet metal, shearing, press brakes, SPM & heavy, wood working and automobile unit. We are…
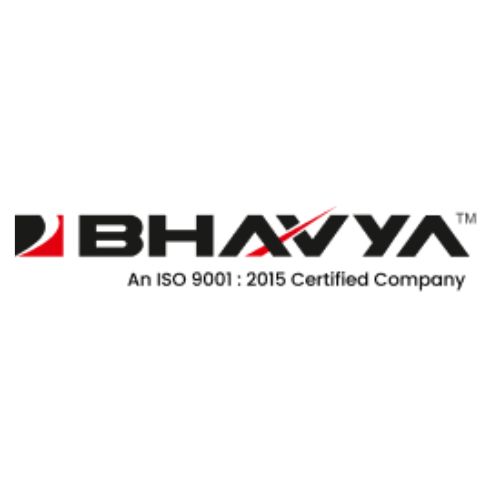
CNC Lathe Machines Can Make Your Job Easy
CNC is the short form of computer numerically controlled which refers to a process in which a computer reads code instructions in order to control a tool. A CNC lathe is controlled by a computer due to which the material…
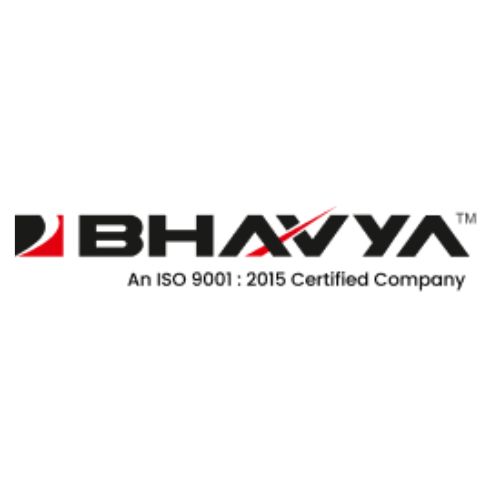
How to Buy Lathe Machine for Your Workshop?
Giving shapes to rigid materials like wood and metals was not an easy job in ancient times. It was a back breaking job to remove unwanted parts from metals to give a specific shape. It is rightly said that necessity…
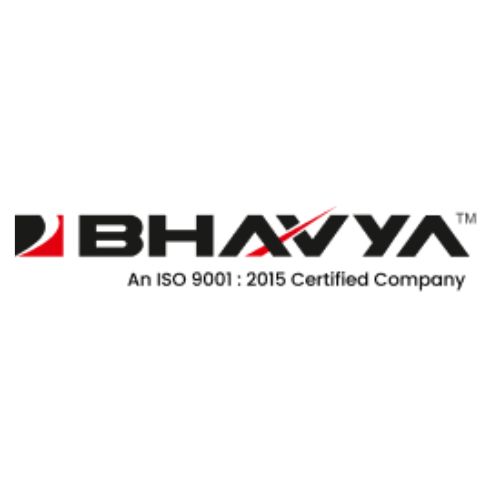
Bhavya Machine Tools Delivers Lathe Machines for Industries and Institutes across India
Lathe machine is wonderful equipment used to shape objects with symmetrical physical properties about the axis of rotation. Various actions like cutting, knurling, sanding, drilling or deformation can be easily and quickly performed on a work piece using a modern…
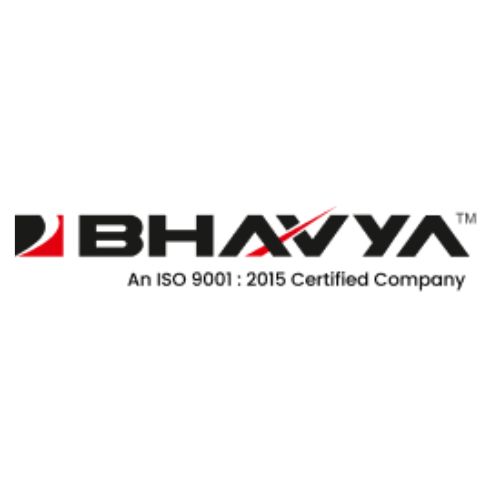
Bhavya Machine Tools Present the Series of Lathe Machines
Lathe Machines are one of the important workshop tools used in creating the symmetry about an axis rotation. It is used to equipment the comparative hard materials. We are leading manufacturer and exporter of lathe are offering a wide range…
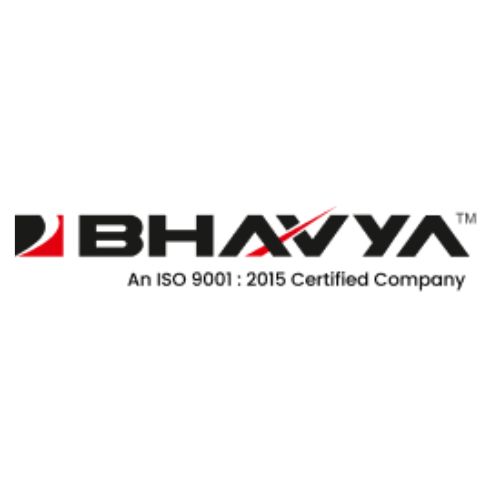
Bhavya Machine Tools Introduces 165mm and 175mm Light Duty Lathe Machines
Lathe machines are the most efficient tools for handling jobs of cutting, shaping and fabricating metals. We introduces a multipurpose light duty lathe which can easily and efficiently handle wide range of applications in a workshop or industry including production…
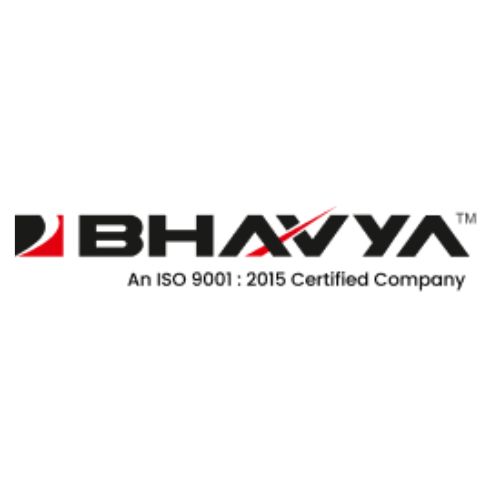
How Lathe Machine Operates?
A lathe machine is a tool used in workshop which spins a block of material to perform various operations such as cutting, turning, facing, threading, sanding, knurling, drilling or deformation such as metal spinning with tools that are applied to…
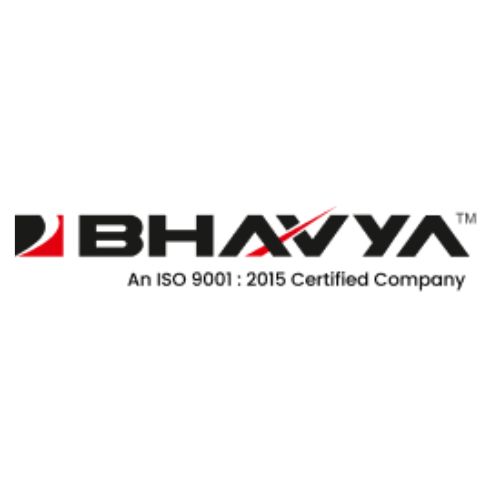
Significance of Lathe Machine for Metal Shaping Industries
There is no doubt in saying that necessity is the mother of all inventions. All the machines are invented with a single purpose and that is to reduce labour work and get things done quickly. In ancient times, giving shapes…
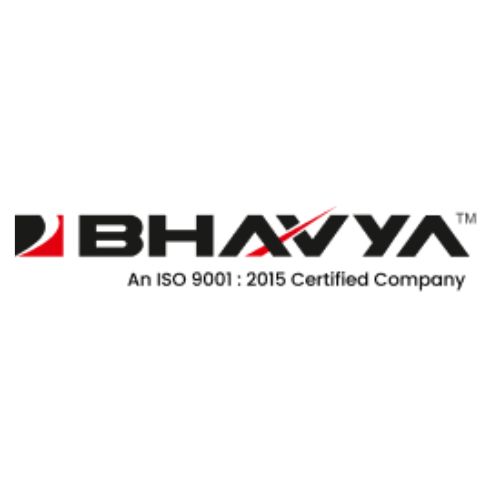
Types of Lathe Machines
A lathe machine is an important machine tool in a workshop as it is basically used to shape the metal articles. Initially the basic operation was to cut cylindrical metal stock which was then further developed to produce screw threads,…
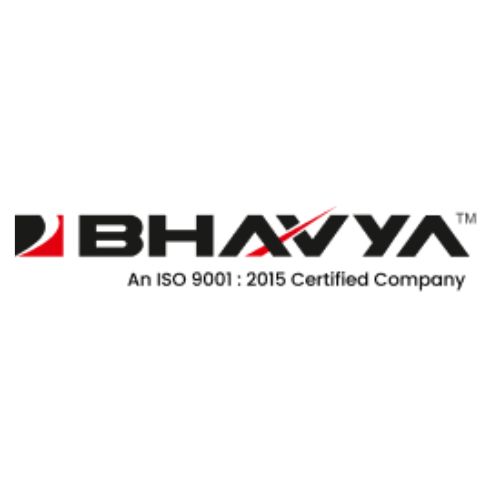
How to Use Lathe Machine?
Basically, a lathe machine is a tool used to shape metals.The material is rotated in the cylindrical motion and then touches a cutting tool to it which cuts the material. The metal sheet is fixed on the chuck of the…