Category Archives: Shaping Machine
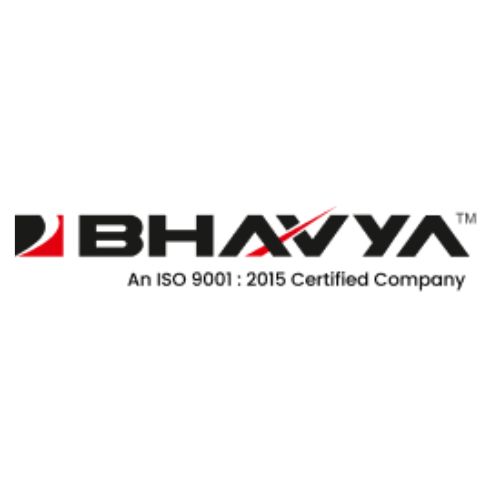
Global Demand and Supply for Machine Tools: Key Products and Role of Bhavya Machine Tools
The demand for machine tools is growing exponentially across the globe as industrial development accelerates in sectors like manufacturing, construction, and metalworking. Machines like Radial Drill Machines, Slotting Machines, Power Presses, and CNC Vertical Machining Centers play a crucial role…
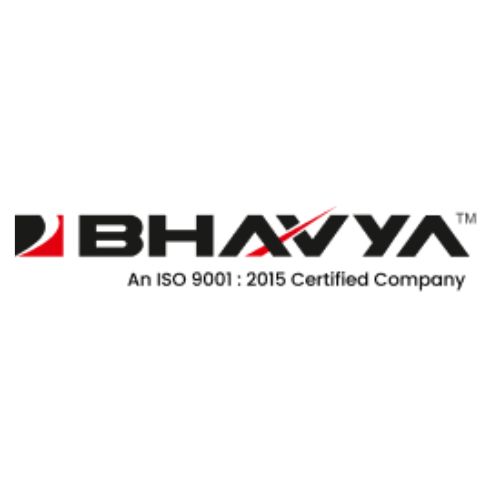
Shaping Machine Tools Demand and Supply in United Arab Emirates Market
There is a great demand for Machine Tools in the UAE market owing to the booming metal cutting segment and the increasing demand for machine mounts in various industrial sectors. Moreover, the growing popularity of additive manufacturing is also driving…
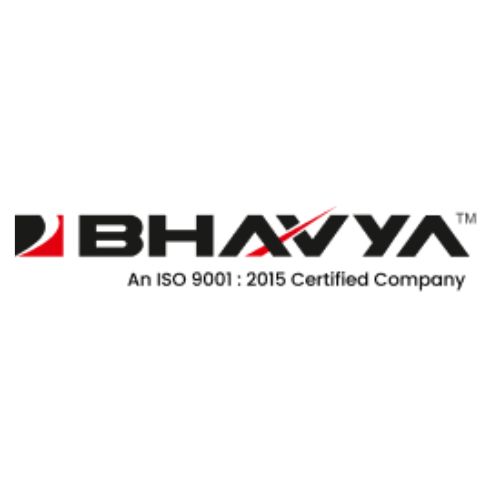
Shaping Machine Industry in Dubai
The shaping machine industry in Dubai is a booming industry that offers many opportunities for both employers and job seekers. The industry has been experiencing a renaissance in the last few years as more people have begun to realize the…
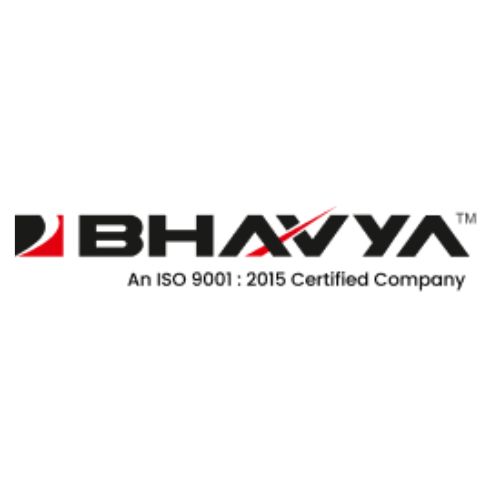
Application of the Shaping Machine in Pulleys and Gears Manufacturing
Introduction The shaper is one of the most versatile and important devices used in production and maintenance centers. It is an important production machine along with milling and lathe machines. The primary role of this tool is to produce surfaces…
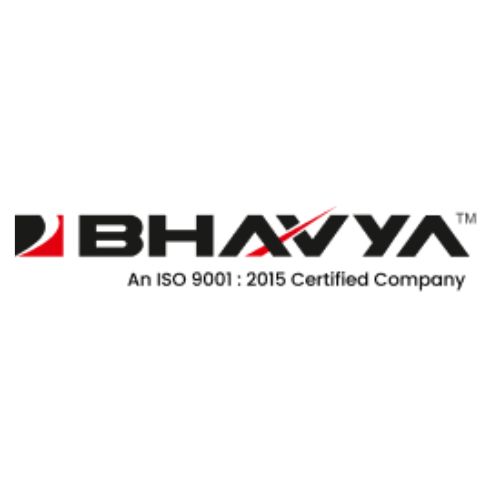
How Industrial Efficiency and Bulk Productivity can be Achieved?
Research and development has led to the availability of many new and better products across many industries throughout the world. This has resulted in designing and producing a vast range of innovative machinery including tool room units for the local…
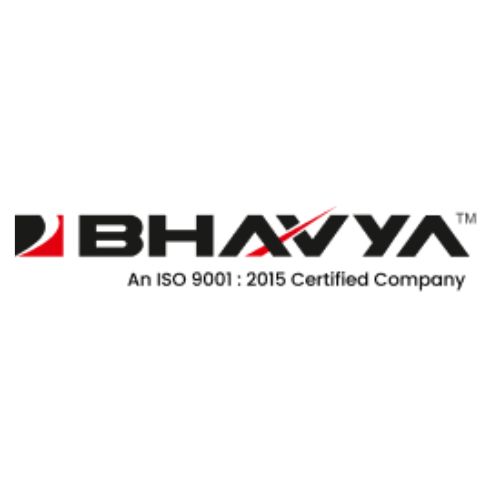
Working Principle & Significances of Shaping Machine
Working principle of shaping machine Among the range of workshop machineries available a shaping machine stays very useful to shape the surface of metal, wood or steel surfaces to a desired shape or dimension. It is quiet easy to obtain…
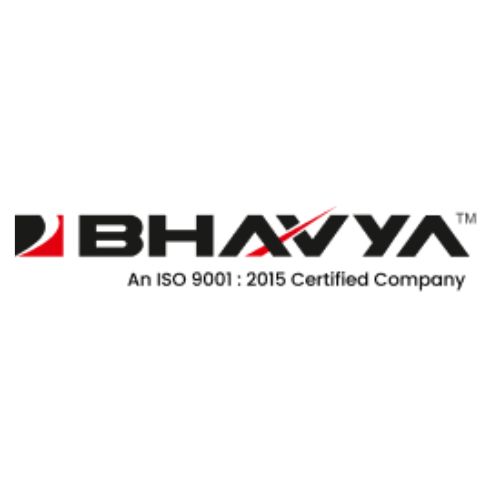
The Magic of Different Shaping Methods with Single Point Tool-A Multipurpose Solution for Flat Surface Machining
The Increasing Industrial Demand for Different Shapes Shaping of materials stays a prime requirement in the metal industry as every process is done in accordance with the expectations from different industries. Metals such as steel, cast iron, aluminium, etc are…
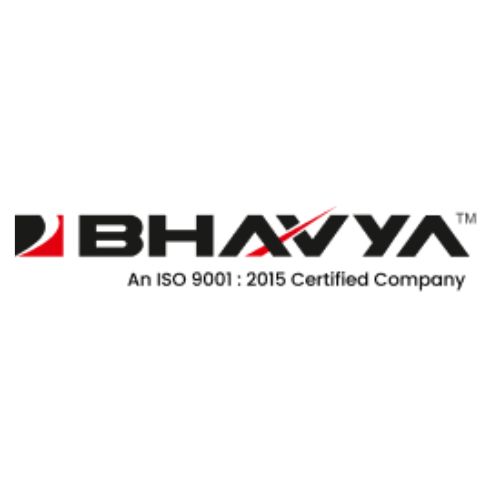
5 Most Important Machine Tools For Any Workshop [INFOGRAPH]
Nowadays, several types of workshop machine tools are manufactured in many countries around the globe. These tools are commonly used for different purposes in a wide range of industrial segments such as woodworking, automobile, electrical, construction, etc. This infograph give…
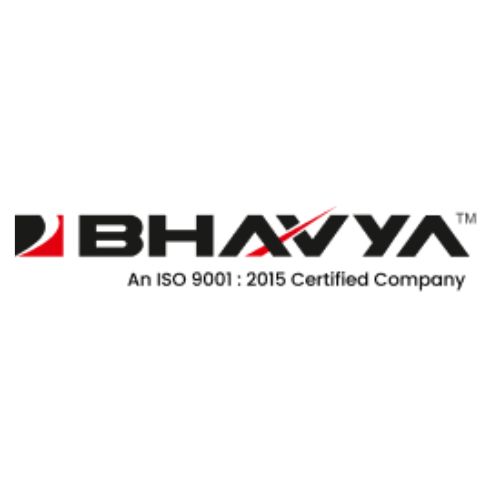
Types of Workshop Machinery – Milling, Grinding, Shaping Machines
Types of Workshop Machinery – Milling, Grinding, Shaping Machines Machine play a very important role in a workshop where metal working or woodworking tasks are performed. They enable speed process in the workshops and enhance the accuracy and efficiency of…
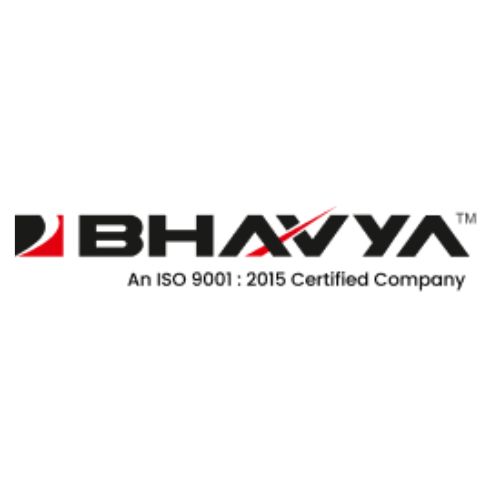
The Most Important Machine Tools Required in Any Workshop
The most important tools required in any workshop, nowadays are described below. Milling Machines The milling machine is used for milling, cutting, shaping, carving, planing, contouring, drilling, stamping, and die-sinking a variety of solid materials. The work piece is positioned, to…
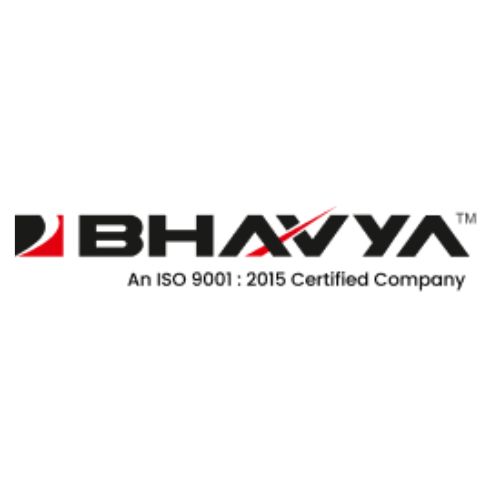
How to Choose a Highly Efficient Shaping Machine
Today, several types of machines, equipments and tools are invented in order to automate numerous industrial activities; such as cutting, drilling, milling, threading, shaping etc. A small or large work piece made from wood, metal etc. can be used to…
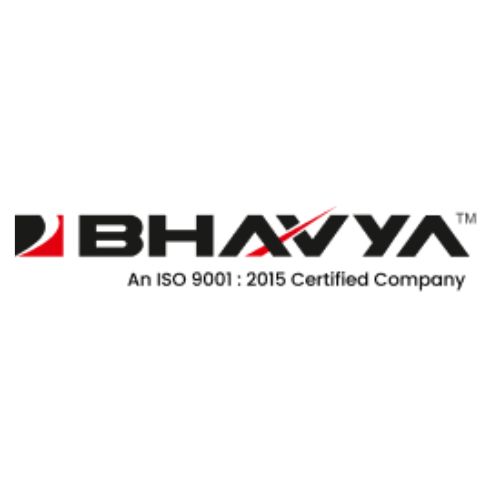
A Brief Description About Useful Tool Room Machines
A tool room basically refers to a room in an industrial unit where special machinery is used, in order to manufacture or repair the various tools and components that are necessary to produce the final product. A tool room also…
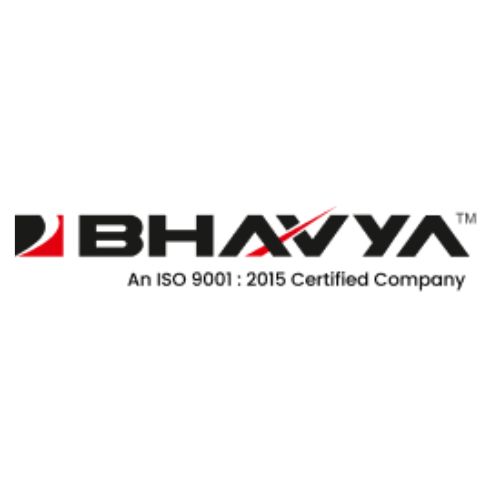
Do You Have the Right Machines for Your Workshop?
In industries, workshop is termed as a place, room or a building containing machines, required to manufacture or repair products. The equipments in a workshop can be wood working, sheet metal, automobile and garage, food processing, printing, welding etc., which…
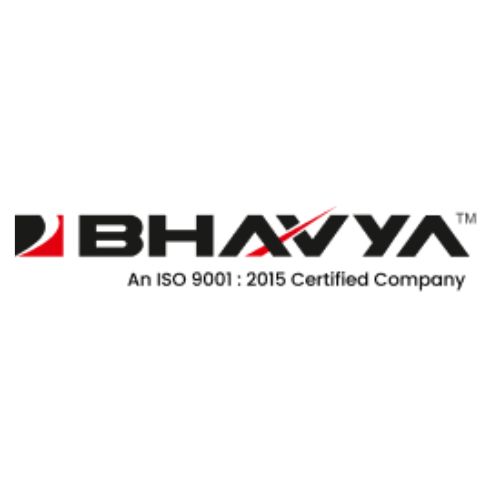
Important Tool Room Machines You Need to Buy for a Workshop
Improvement of processes in a workshop and automation doesn’t need to be an expensive affair. It needs to be a smarter choice of tool room machines required in a workshop. Various industrial applications require rigid material like wood and metal…
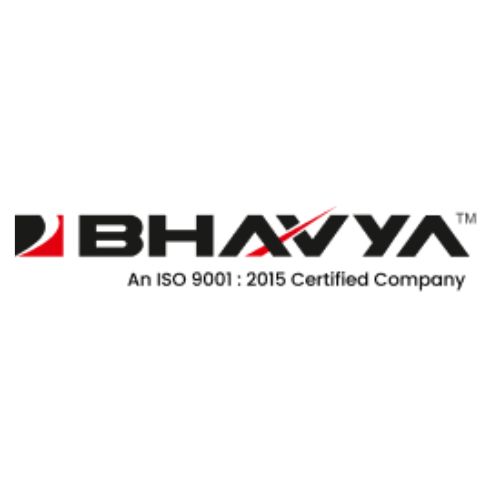
Bhavya Machine Tools Supplies Latest Technology Shaping Machines for Industrialists of New Era
Higher production requirements of the industries are compelling the industrialists to update their manufacturing equipment with latest technology which gives higher and also faster production rates. Team at Bhavya have very well understood this requirement of industrialists of the new…
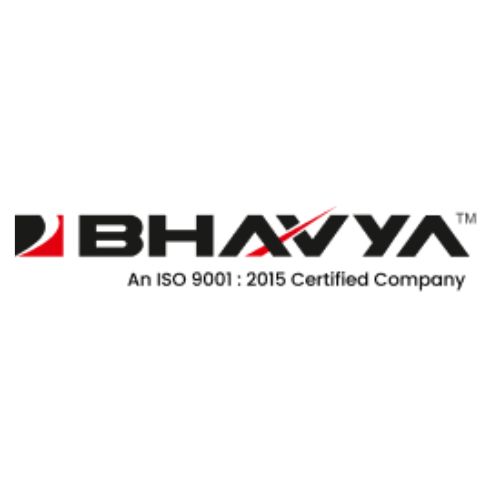
Bhavya Machine Tools Presents Grinding Machine, Slotting Machine & Shaping Machine
Machine tools are widely used tool room machineries across the industries. As an industry leader in manufacturing machine tools in various sizes and standard materials for rough & tough usage. There is a high demand of tool room, lathe, drill,…
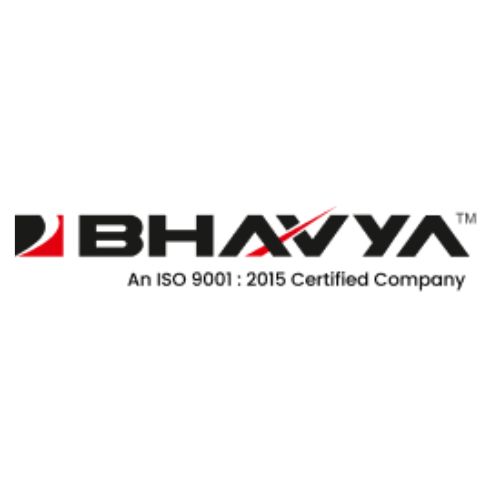
Tool Room – Types of Tool Room Machines, Toolroom Setup
Tool room Tool room is the room where the tools are kept for storage, prepare, repairing and machining. The space area can be varied based on the types of the tool room machines and applications. It may include high end…
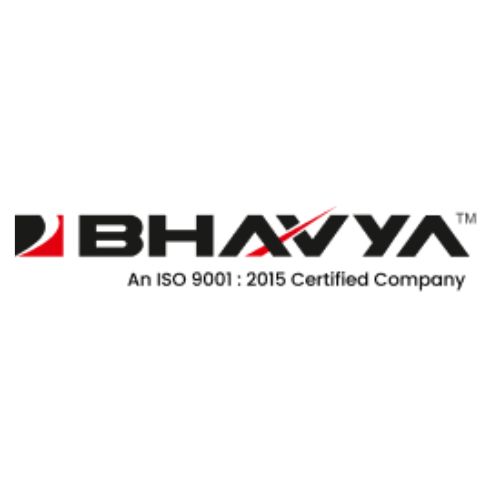
Machine Tools – Grinding Machine, Shaping Machine, Milling Machine
Grinding Machine Grinding machine is one of the important tools for industrial usage. It is also referred as Grinder. It has two abrasive wheels for grinding the work piece. Grinder can be used to cut and grinding the work piece…
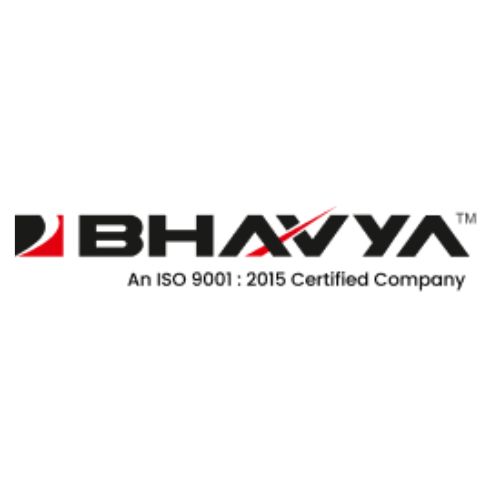
Metal Shaping, Sizing, Slotting & Bending with Machine Tools
Metal shaping and sizing is a big industries which needs heavy machine tools to differently shaping a cutting of the metals. Handling with tools are totally mechanical works with electrical integration. In this process metal work piece is carved by…
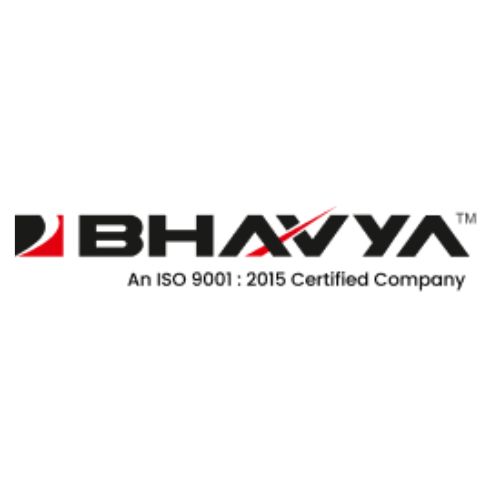
Types of Machines Used for Shaping and Cutting Metals
Types of Machines Used for Shaping and Cutting Metals The use of metal has become essential in many industries like automobiles, construction, electrical, furniture etc. Thus, there are many equipments used for shaping and cutting metals for the faster production.…
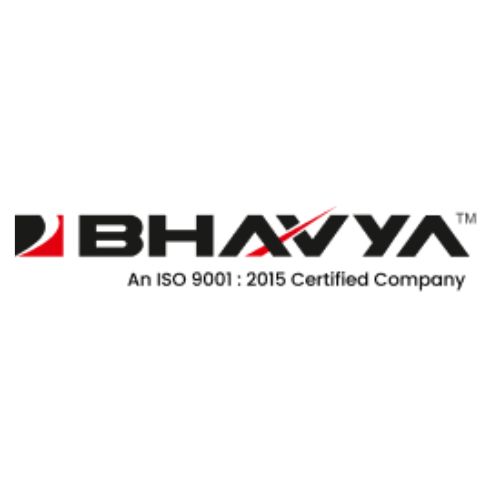
Shaping Machine, Slotting Machine, Milling Machine
Forms of Metal Forming Machinery - Shaping Machine, Slotting Machine, Milling Machine, Lathe Machine Different kinds of metal working machineries are used to form the metals into required shapes and sizes. These include the metal shaping machines, metal cutting machines,…
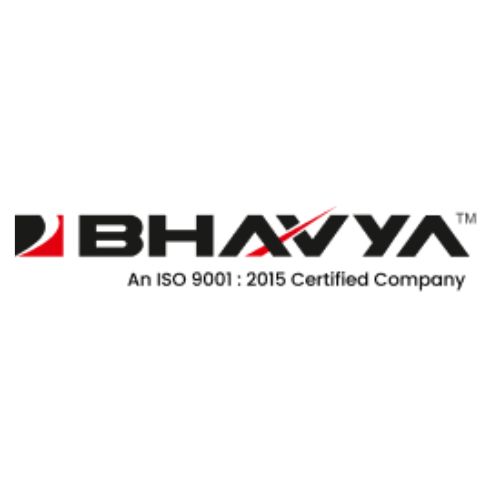
Machine Tools for Sheet Metal Industries for Slotting, Shaping & Bending
Slotting Machine for Sheet Metal Industry It is used to shape and cut metal, wood and other hard materials. It is a heavy duty machine with robust design and high speed equipment used in metal industries. Slot making applications are…
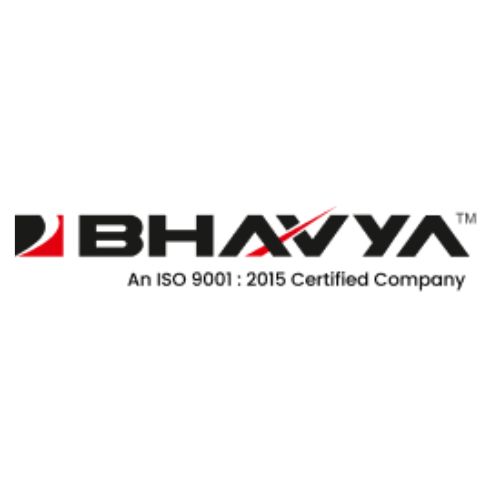
Tool Room Machines – Slotting Machine, Shaping Machine, Milling Machine
Tool Room Machines - Slotting Machine, Shaping Machine, Milling Machine Tool room is a space for making tools. In a broader sense it can be defined as facility where the tools and machining equipment are made, stored, and repaired on…