Category Archives: Milling Machine
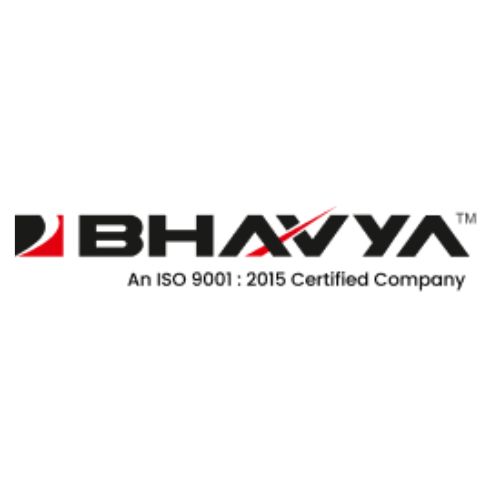
Various Milling Machines and their Applications
Milling machines are indispensable tools in the manufacturing industry. They come in different types, each designed for specific tasks, ranging from light precision jobs to heavy-duty operations. This article covers different types of milling machines, including Vertical Turret Milling Machines,…
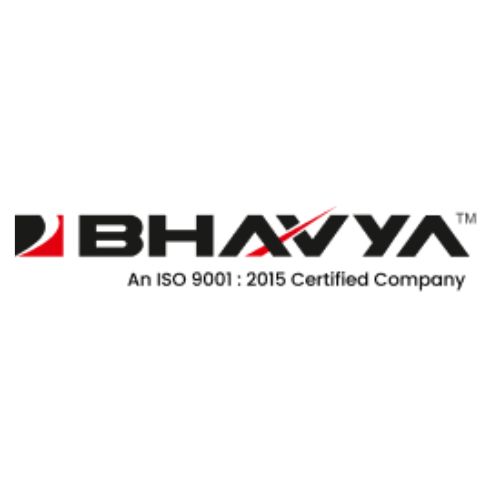
Vertical Turret Milling Machines: Significance of Industrial Capabilities in UAE
Introduction to Vertical Turret Milling Machines Vertical turret milling machines are versatile and efficient tools designed for cutting, drilling and shaping metal and other materials. These machines feature a spindle that moves vertically and a turret head that allows angular…
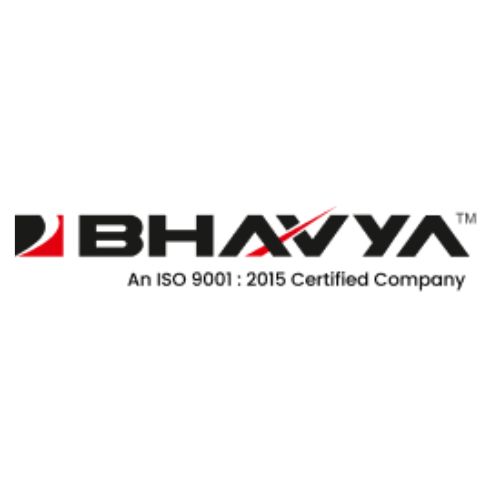
Vertical Turret Milling Machine in Oman: Precision Engineering for Versatile Applications
Introduction Milling machines play a crucial role in the world of precision engineering, where accuracy and efficiency are key to success. One such versatile tool is the vertical turret milling machine, designed for reshaping metal and solid materials with precision.…
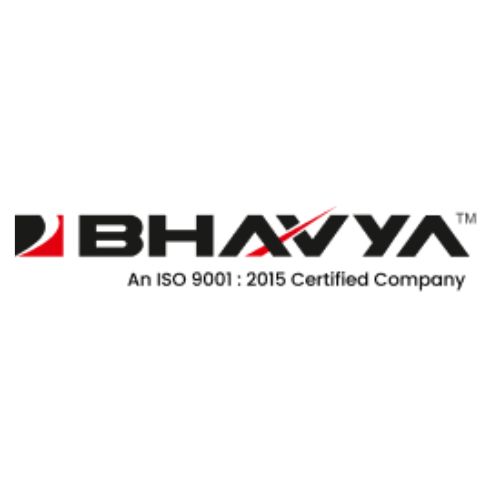
Transforming Manufacturing with Advanced Milling Machines in Africa
Introduction The industrial landscape in Africa is rapidly evolving, driven by technological advancements and the increasing need for precision and efficiency in manufacturing processes. Among the essential tools contributing to this transformation is the milling machine. Milling machines are used…
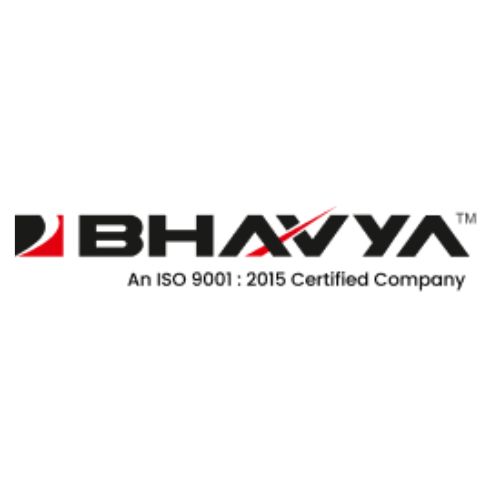
The Different Types of Milling Machines and Their Working Benefits for African Countries
Milling machines play a crucial role in various industries, contributing significantly to the manufacturing processes in African countries. Understanding the different types of milling machines and their unique working benefits is essential for industries seeking efficiency and precision in their…
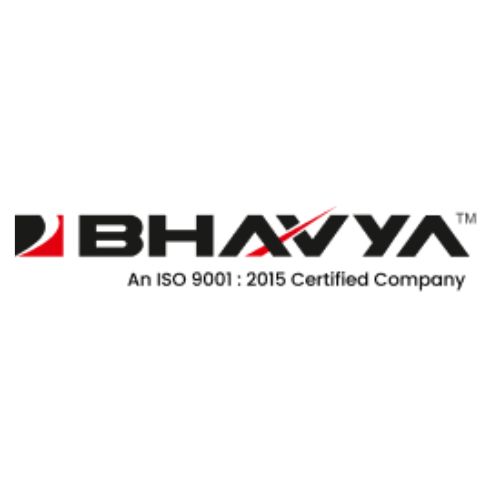
European Artisanal Workshops and the Role of Milling Machines: Crafting Excellence
In the heart of Europe, artisanal workshops continue to uphold centuries-old traditions of craftsmanship, producing exquisite works that blend skill, passion, and heritage. In this narrative of craftsmanship, milling machines have emerged as crucial tools, harmonizing tradition with innovation. This…
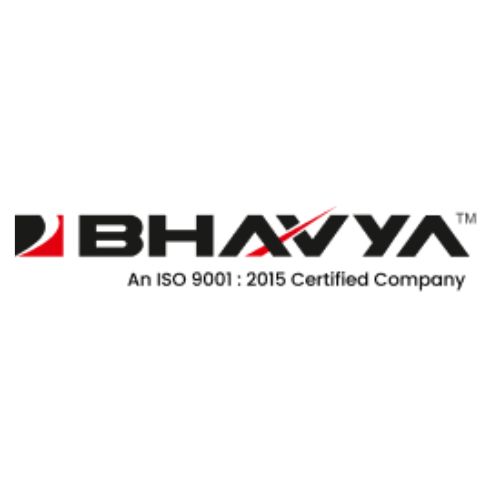
Milling Machine Tools Market in United Arab Emirates
The United Arab Emirates is a major market for the milling machine tools industry. This market is mainly fueled by the increased demand for automobile parts in the region, as well as the growing manufacturing sector in the region. The…
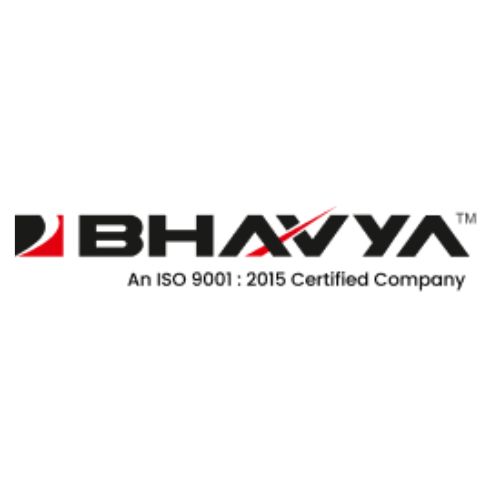
The Milling Machine Tools Industry in Dubai
The Milling Machine Tools Industry in Dubai is one of the most vibrant and growing industries in the Middle East. The industry's growth is fueled by an expanding manufacturing sector and the increasing demand for machinery. A variety of different…
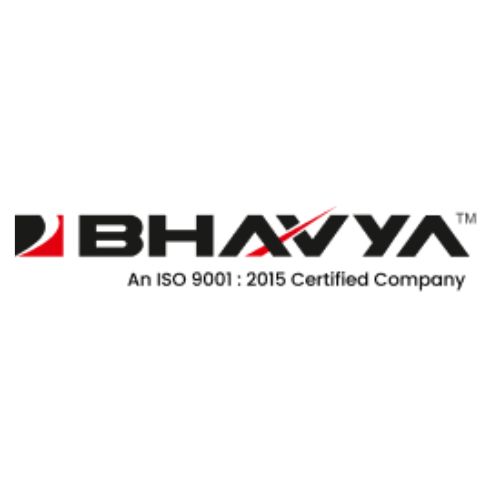
Different Types of Milling Machine and their Market in Kuwait
Bhavya Machine Tools are one of the best milling machine manufacturers for the Kuwait market, and we offer several types of milling machines, such as the horizontal milling machine, vertical milling machine, and CNC milling machine. Bhavya Machine Tools being…
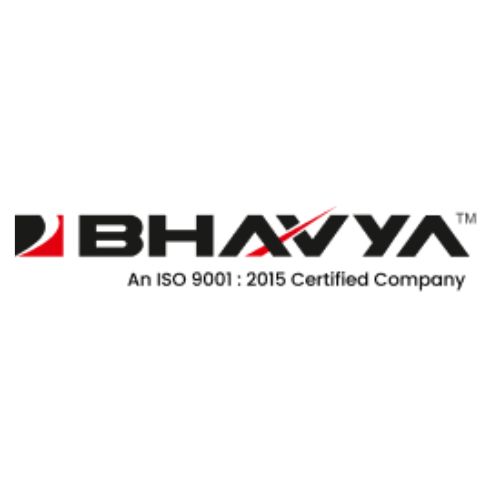
How to Choose Milling Machine in Bahrain?
We, at Bhavya Machine Tools one of the leading suppliers of milling machine to Bahrain, and other countries knows understand the need of choosing the right milling machine for your work is a key decision. The speed at which a…
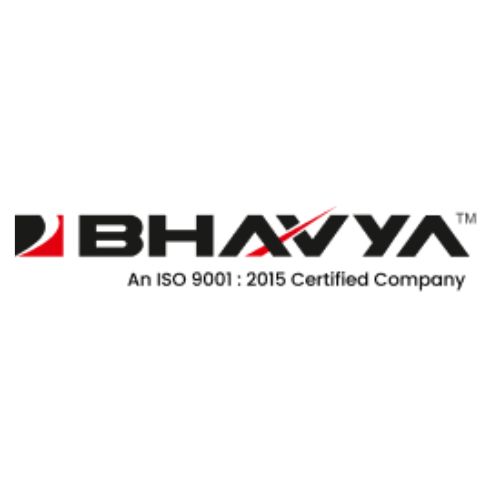
Milling Machine Demand and Supply in Oman Market
The demand for Milling Machines has increased in Oman. The Milling Machines are used in various industrial sectors such as Automobile, Construction, Aerospace, and Defense. The demand for Vertical and Horizontal Milling Machines has increased significantly. Demand of Milling Machine…
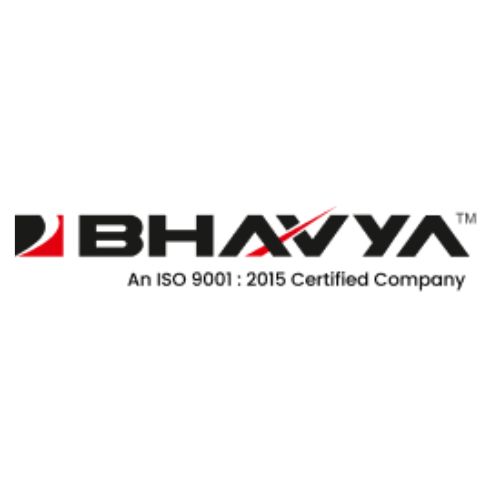
Know about Milling Machine Market in Bahrain
During the last few years, the milling machine market in Bahrain has witnessed an increase in demand for the machines. This is primarily due to the increasing demand for the machines from the construction industry. However, there are other factors…
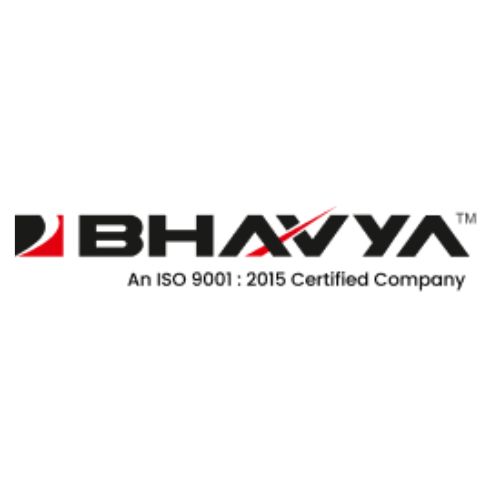
Keyway Milling with CNC Milling Machine
If you are a manufacturer of a variety of different types of products, you may want to consider using a Milling Machine to perform the necessary operations. This type of machine is used to create complex shapes using different kinds…
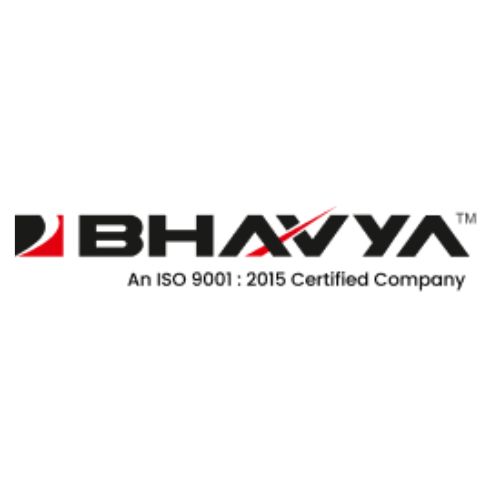
Factors to Consider When Choosing a Drilling and Milling Machine
A Drilling and Milling Machine is the most useful tool for cutting metal parts, such as drill bits and bolts. These machines offer different features, such as cutting horizontally and vertically. Although drills are an ideal choice for beginners, milling…
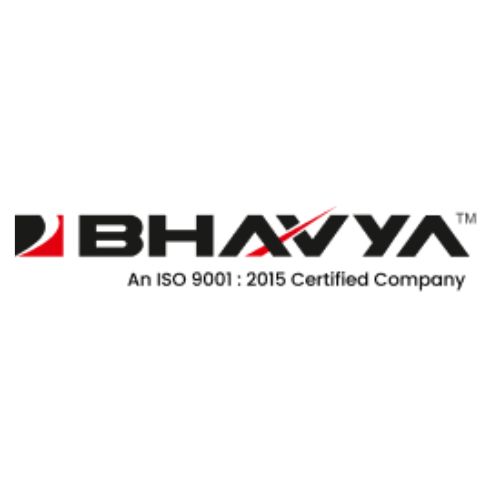
Milling Machine Market in Middle East and North Africa – Global Market Trajectory and Analytics
According to a newly published report that is related to Milling Machine Market in the Middle East and North Africa, and which provides global market trajectory and analytics and fresh insights on the opportunities in the post-COVID-19 marketplace the Milling…
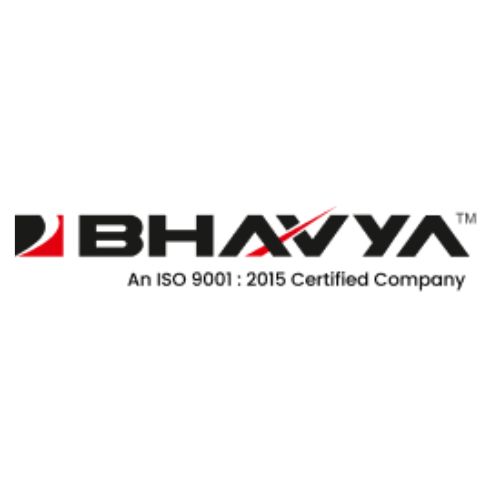
Types of Universal Milling Machines
A Universal Milling Machine is a versatile piece of machine tool that is capable of performing a wide variety of operations, from boring to shaping. Its rotary fixture allows the table to rotate at an appropriate angle, and its indexing…
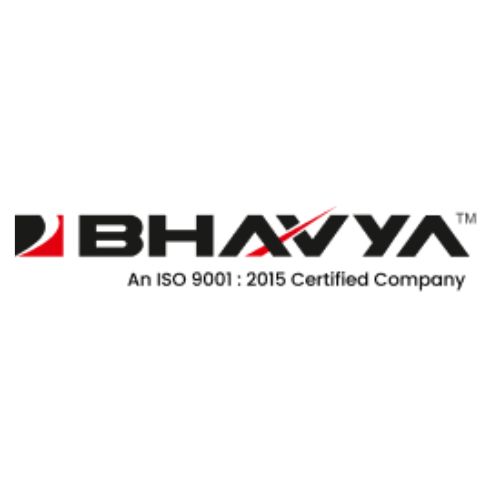
Choosing a Vertical Machining Center
Choosing a vertical machining center (VMC) is an important decision for any business, and it is important to do your homework to make sure that you make the best choice for your needs. The type of machine tool you select…
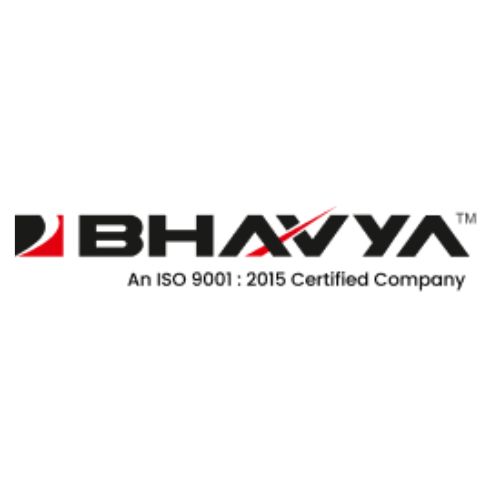
Benefits of a Vertical Milling Machine
A Vertical Milling Machine is used to create precision cuts on metal parts. Its versatility is unmatched, and its fast turnaround time makes it ideal for everyday jobs. The benefits of a vertical milling machine are also extensive, making it…
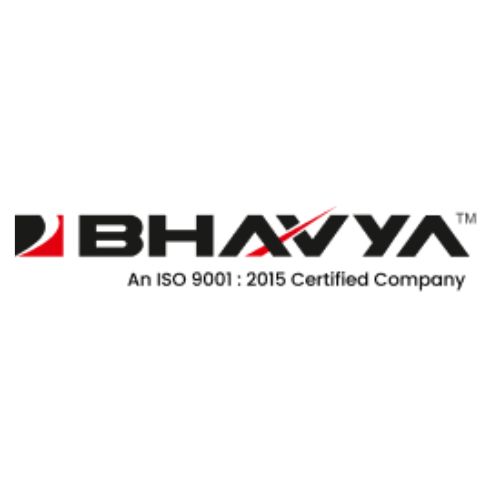
CNC Programming Commanded Vertical Milling Machine
A vertical milling machine is a very important machining tool that has become very popular over the last ten years or so. This type of machine can do some very precise and intricate tasks, which makes them very desirable to…
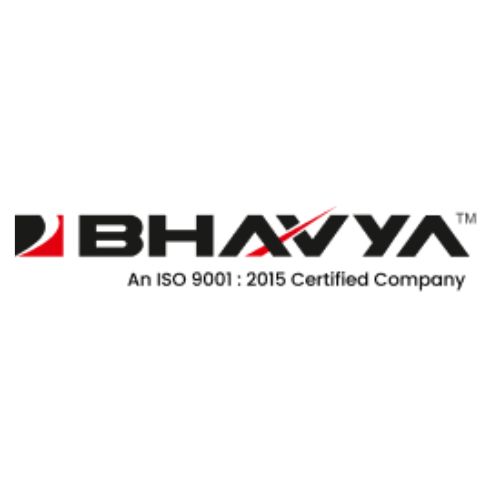
Vertical Knee Type Milling Machine
If you are in the market for a vertical milling machine, then this information will prove very useful. Vertical milling machines are very popular for many different types of applications, including metal and woodworking. It's important to know what type…
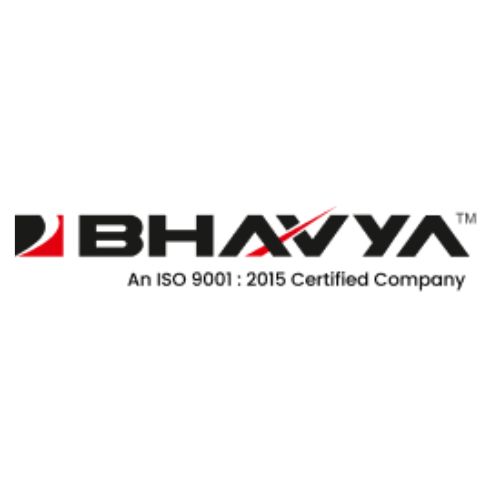
Types of Milling Machines
The universal milling machine offers the following capabilities: mill, table, router, and plasma cutter. This versatile machine can be operated in a stand-alone mode with its power supply or it can be connected to the table and plasma cutter. In…
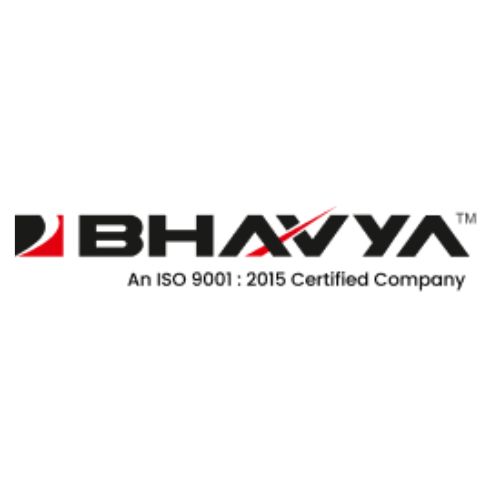
All About Knee Type Milling Machine
There are several types of machines used in knee milling processes. The basic function of any type of milling machine is to move the workpiece from one position to another. Depending on the type of machine, the different processes can…
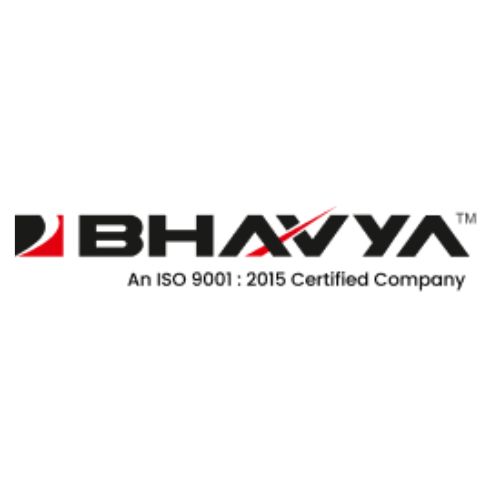
New Keyway Machine in the Market This Year
If you are in the keyway milling business, then you should know that it is not an easy business. It involves lots of tedious works such as polishing and grinding to create products that look great. These machines are extremely…
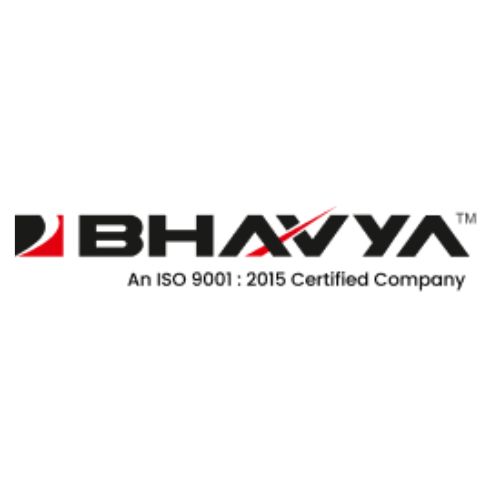
What is M1TR Milling Machine and How Does It Work?
The M1TR Milling Machine is recognized as a dependable, tough, and steadfast milling machine. Low maintenance, high reliability, and extreme ease of operation have made it the perfect choice for many industries. Factors to Consider when Buying M1TR Milling Machine…
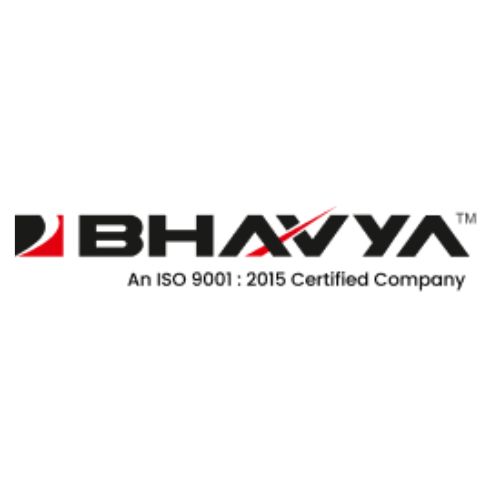
Heavy Duty Milling Machine for Perfection in Workflow
A heavy-duty milling machine is used for the production of large numbers of identical products at a fast rate. In addition, it can also perform other tasks that increase its versatility to any business. When purchasing a milling machine, it…
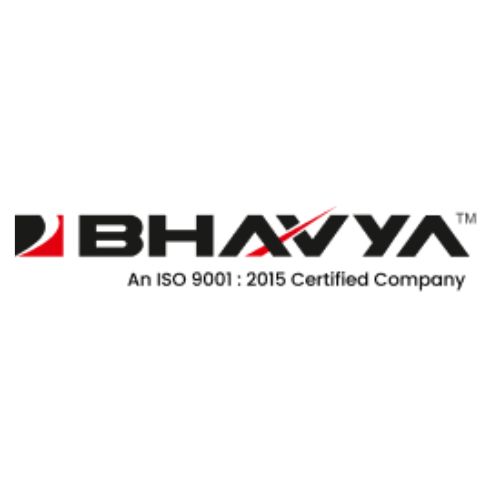
What Are the Main Parts in a DRO Milling Machine?
A DRO milling machine is a tool used in the production of metal alloys and aluminum products. This type of machine is used for the precise molding of metal and other solid materials. It provides different varieties of tools for…
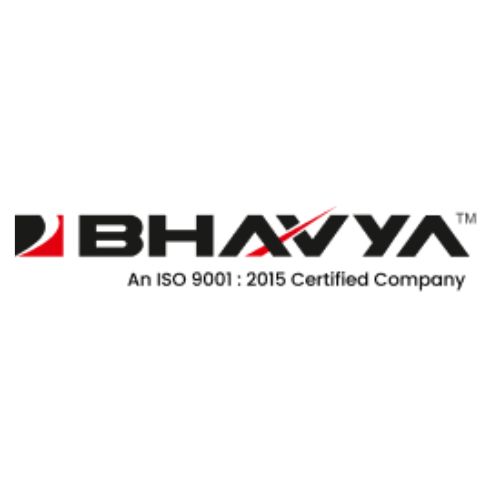
How Are Drilling and Milling Machine Tools Different?
The drilling and milling machine tool is an automated machine tool that incorporates drilling, cutting, grinding, and polishing, and is usually utilized in the production of medium and small-sized components. It is mostly used for cutting, drilling, and milling abrasive…
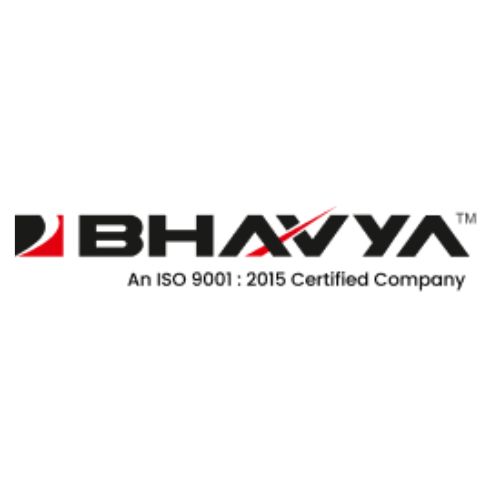
Column Type Milling Machine – Best Materials for Metal Casting
Column-type milling machines can be used in a variety of applications including scrap aluminum fabrication, making of frames, metal tubes, air cushion filling, components of musical instruments, etc. The machines are designed to operate with minimum strain on the operator's…
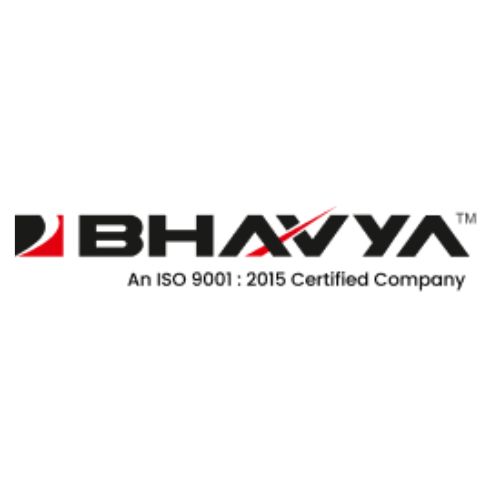
The Major Differences between Column and Knee Milling Machines
Column and Knee Type Machines They are the most popular commercial milling machines utilized for general industry work. The two types differ mainly by their functions and characteristics, although both employ the same methods of turning steel into components. Difference…
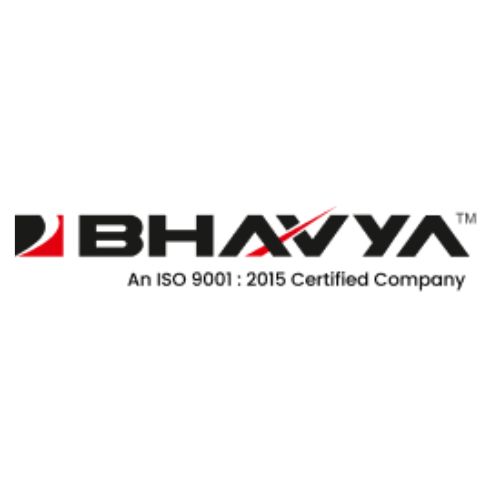
Rising Demand for Different Machine Tools in Industrial Sectors of Punjab
Punjab has emerged as India’s one of the most industrially advanced states. The demand for specialized industrial machine tools has risen significantly over the years in Punjab state, thanks to rapid industrialization and the rise of small and medium-sized businesses.…
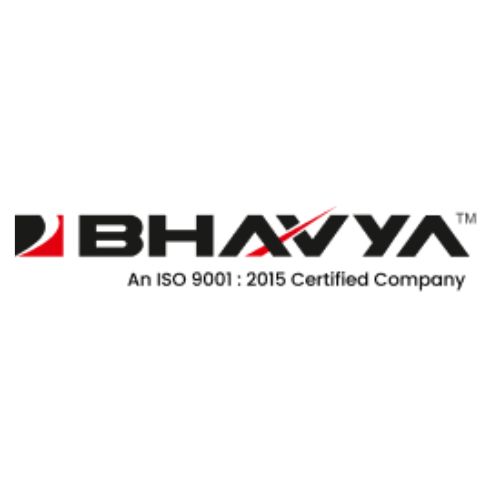
The Elaborations on Metals: Milling Machines
A milling machine is a tool extensively used by metal industry because of its versatile, multi-purpose and advantageous capability to work with pieces of metal. The key feature of a milling machine is the cutter which susceptible to desired speeds…
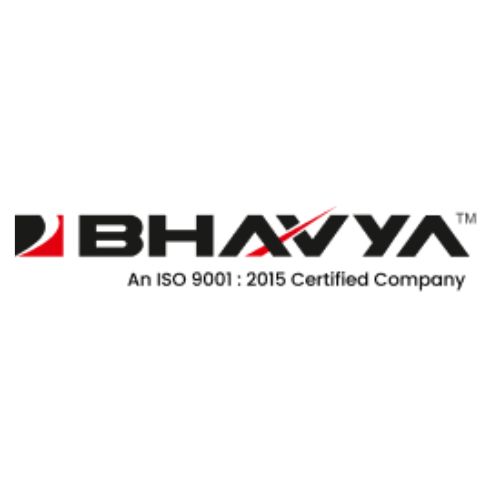
Milling Machine & Its Benefits in Industries
To be a market leader in the industry, it becomes top most priority to understand which technology becomes a need fit to your business. You know your business needs well. You know precisely what is going to be the specific…
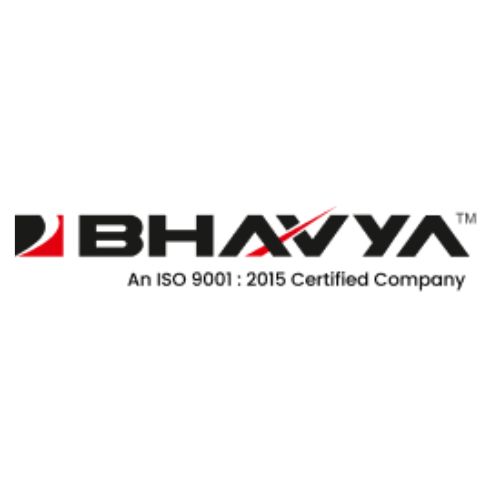
Development of Milling Machines & Its Types
With the growing manufacturing industry, milling machines have replaced the role of other types of equipment. It is one of the most important machine tools in the manufacturing industry. Initially, milling machines were been experienced for a simple processing equipment,…
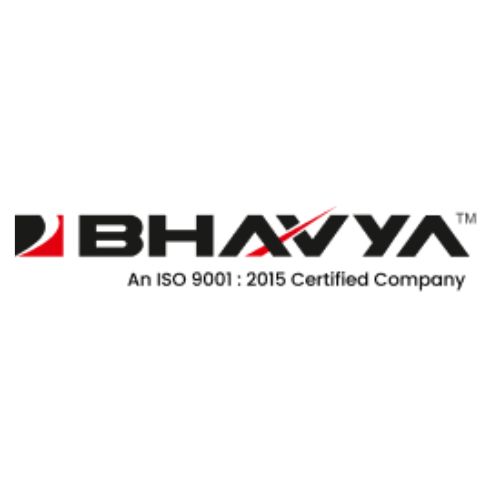
The Milling Machine in Packaging Material Manufacturing
The packaging equipment making such as plastics and paper processing are heavily mechanized process in industry and there are various equipments used in this process. These include corrugation machines, rotary cutting and greasing machines, slotting machines, sheet-pasting machines, board cutting…
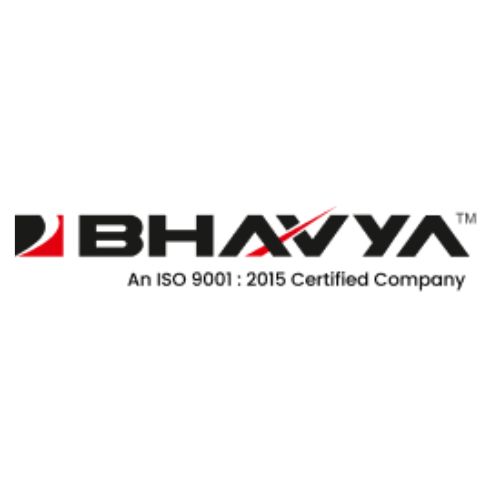
Industrial Milling Machine – Useful Tips While Selecting the Best
Milling machine is used in industries dealing in wood, metal, plastic etc. Solid hard materials can be formed into shapes of desire. With the advanced technology there is a great improvement in the working. Today they work much faster than…
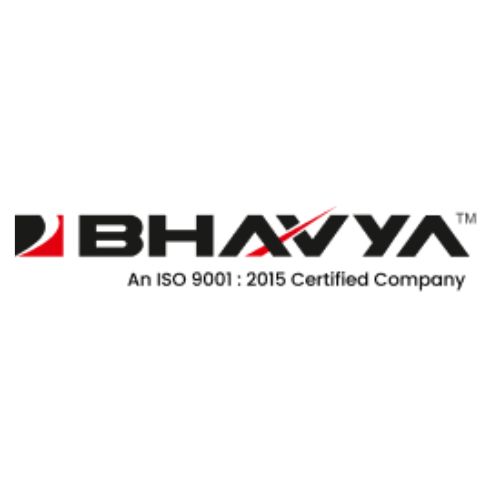
Making of Metal Based Medical Devices
Types of Medical Accessories made from Machining Healthcare industry has extensive demand of minor to major gadgets made from metals. Machining equipments have significant roles to play in formation of metal based gadgets. These accessories range from small to moderate…
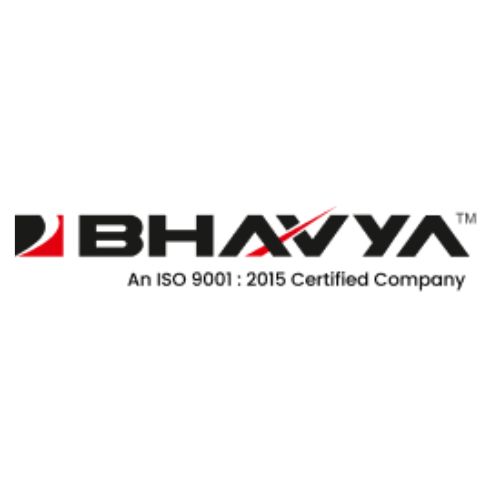
How to Manage Milling in Depth?
Growing Milling Requirements Mill is one of the priority equipments for metal industries and fabrication jobs. It helps it getting the toughest metal components ready to be composed for final produce. It is one of the main devices that prepare…
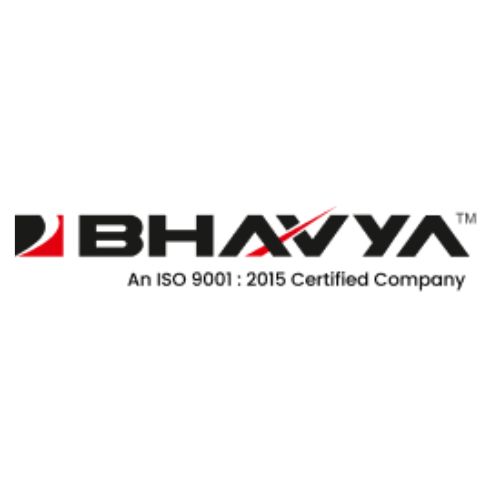
The Vertical Machine Center – Advanced Milling Techniques that Deliver High Quality Workmanship
Milling requirements have been changing in accordance with the industrial requisites. There are innovations made in milling specifications and vertical center is one among them that is suitable to obtain rigid and flexible milling in fragile work materials. Development of…
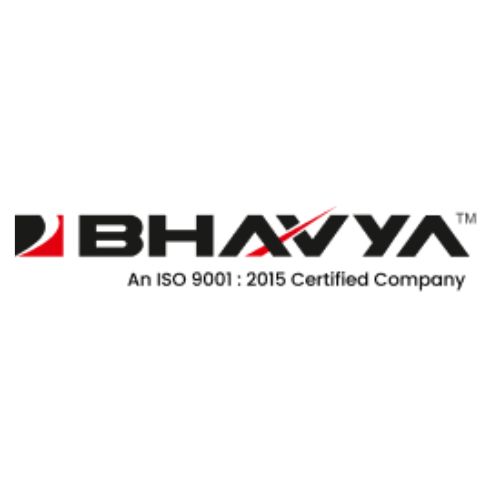
Essential Activities Followed by Machine Designers While Designing Milling Device
Innovations Introduced in Machine Design Unlike earlier days, designers no more need to depend on pencil drawing over graph sheets to bring a new equipment design. It is hard to imagine that tools can be designed with the help of…
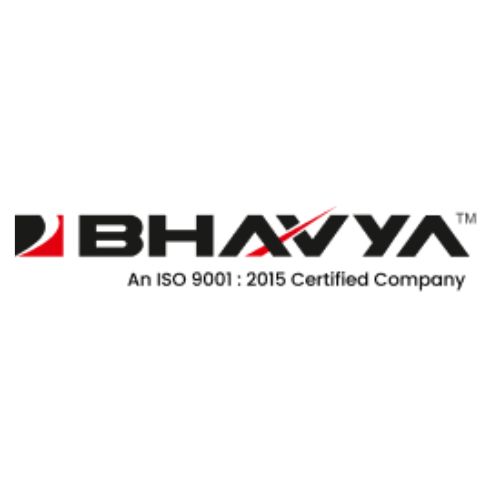
Cut Metal Work Pieces Faster and to High Precision Using Hydraulic Hacksaw Machines Tools
As the production metal cutting volume increases in the industries the hydraulic hacksaw tool offers the solution to accuracy and efficient metal cutting. The skilled and professional manufactures of hydraulic hacksaw equipments have manufactured high superior quality and durable for…
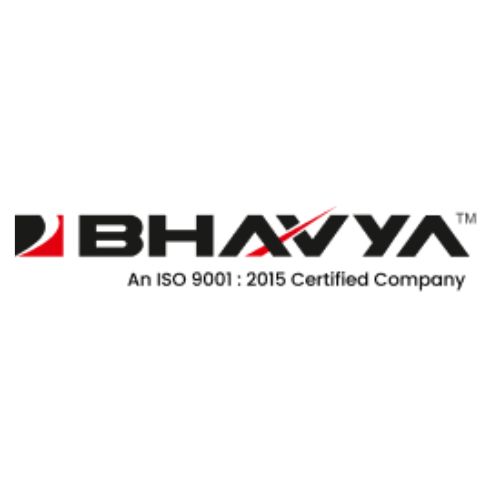
A CAD Directed Milling Device-The Ultimate Solution to Work with Multiple Tool Heads
Working with Multiple Tool Heads-The Interesting Aspect of Milling Milling device is a special component designed to shape different solid work materials such as metals, wood, etc. While machining solid work pieces the equipment helps to bring out the desired…
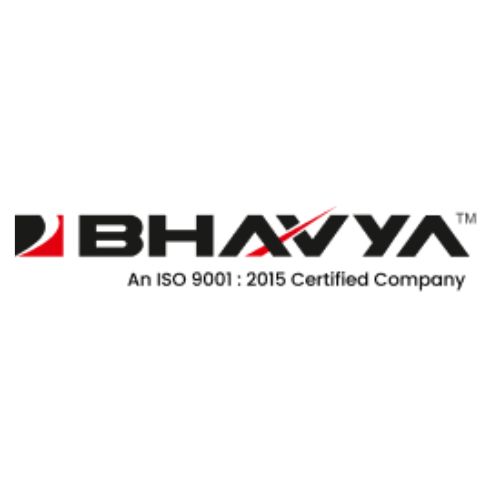
Understanding How Metal Processing Requisites Elaborated With Milling Device
Metal Processing- A Job with Tough Requisites Processing a solid material like metals contains tough requirements as it is not easy to obtain precise dimension without the help of machining device. A milling apparatus is the one that is manufactured…
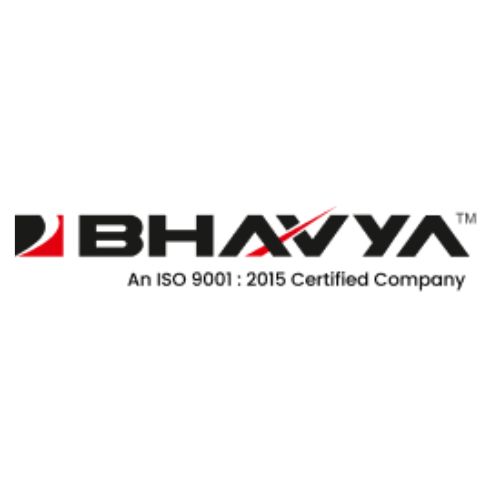
Workshop Machinery Employed for Standard Mechanics
Workshop machinery is also known as machine shop tools. This equipment is used in the fabrication or machining process. The process will involve transforming raw material into a useful product. Each type of Workshop equipments will have its pros and…
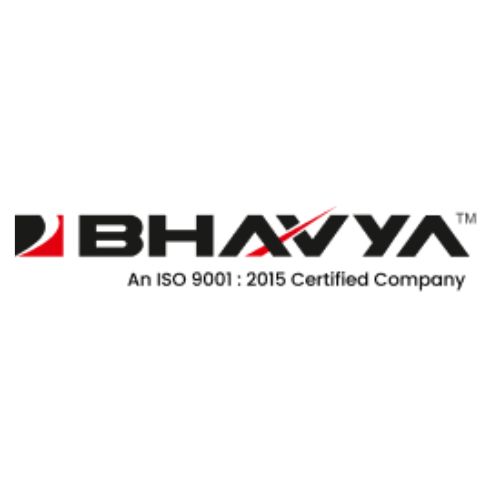
Operational Efficiencies and Drawbacks of a Turret Milling Machine
What is Turret Milling Machine? Workshop machineries stay useful for several core machining works. It is one of the workshop equipments that are used particularly for cutting metals into a predetermined shape. It is preferred for workshop process to obtain…
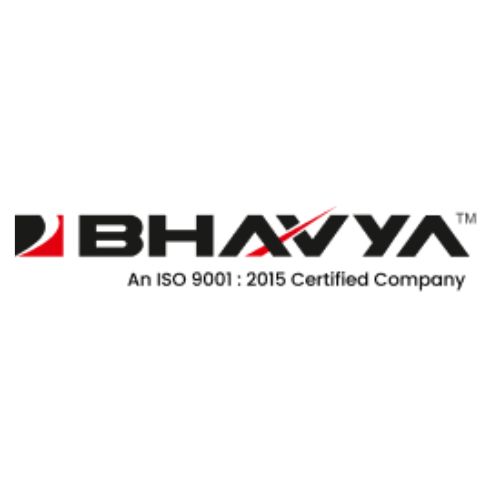
Difference between CNC turret Milling machine and a normal milling machine
Milling is the process by which rotating cutters remove extra material from a metal or wood piece of work to give it a definite shape by means of a machine. It is a frequently used process in the industry and…
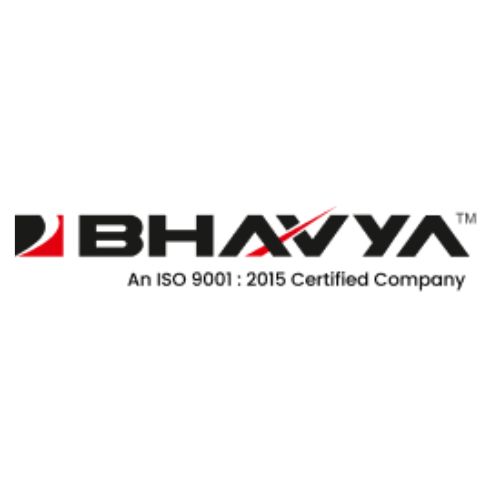
Demand of Slotting Machine & Milling Machine (Tool Room Machines) in World Market
India and China immerging as a Manufacturing Hub for Tool Room Machines and other Machine Tools Research and development has shown a great deal of demand for tool room machinery with their availability and functionality. New and better products are…
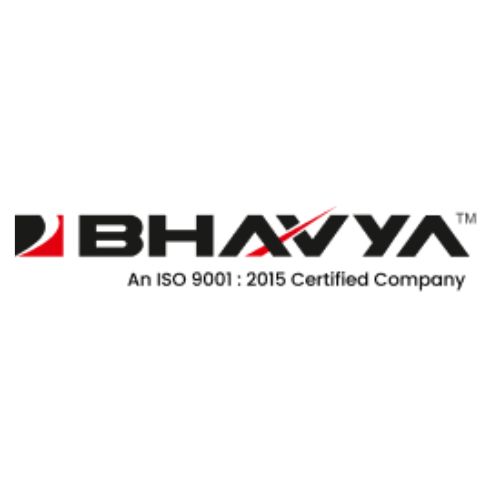
5 Most Important Machine Tools For Any Workshop [INFOGRAPH]
Nowadays, several types of workshop machine tools are manufactured in many countries around the globe. These tools are commonly used for different purposes in a wide range of industrial segments such as woodworking, automobile, electrical, construction, etc. This infograph give…
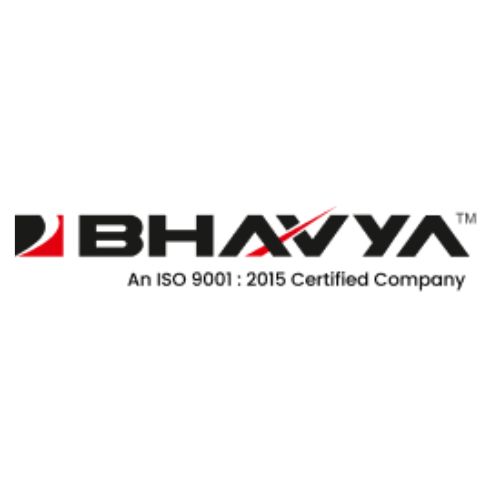
Know the Important Safe Guards while Operating Milling Machine
A milling machine includes a cutter that functions at a high speed. Hence, it can harm the user if not operated properly. Moreover, the milled material may cause serious injuries, because the metal chip is very sharp. Further the metal…
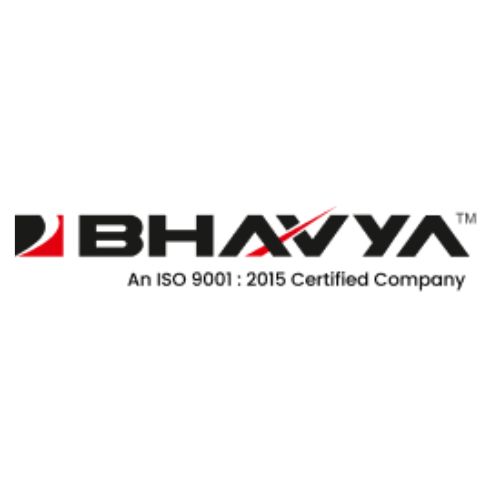
Types of Workshop Machinery – Milling, Grinding, Shaping Machines
Types of Workshop Machinery – Milling, Grinding, Shaping Machines Machine play a very important role in a workshop where metal working or woodworking tasks are performed. They enable speed process in the workshops and enhance the accuracy and efficiency of…
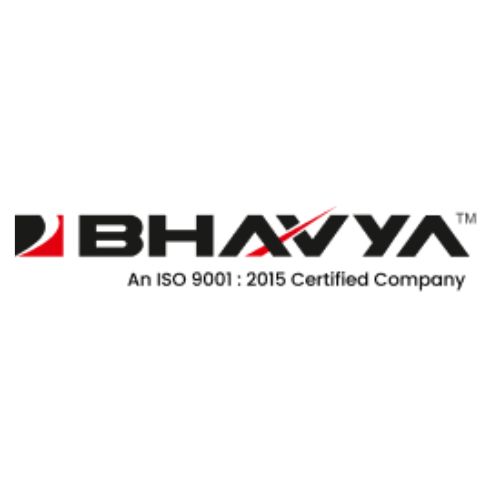
An Overview of CNC Milling Machine
The milling machine is a versatile tool that is utilized for machining solid materials. It can perform various simple as well as complicated operations, such as slot and keyway cutting, planing, drilling, contouring, diesinking, etc. They are mainly classified in two basic configurations namely vertical and…