Chamfering machines have been an integral part of manufacturing processes for decades, providing precise and uniform beveling to different materials such as metal, wood, and plastic. However, with advancements in technology, chamfering machines are undergoing significant transformations, enabling manufacturers to achieve higher productivity, efficiency, and quality in their operations.
Automated Chamfering Solutions
One of the prominent future trends in chamfering machine technology is the integration of automation. Automated chamfering machines are designed to perform repetitive tasks with minimal human intervention, resulting in increased productivity and reduced labor costs. These machines can automatically adjust cutting parameters, tool positioning, and material handling, allowing manufacturers to streamline their production lines.
Integration of Artificial Intelligence
Artificial Intelligence (AI) is revolutionizing various industries, and chamfering machines are no exception. By incorporating AI algorithms, chamfering machines can analyze vast amounts of data, optimize cutting processes, and make real-time adjustments to ensure the highest level of precision and efficiency. AI-powered chamfering machines can also learn from previous operations and continuously improve their performance.
Enhanced Precision and Accuracy
Future chamfering machines are focused on achieving even greater levels of precision and accuracy. Advanced sensors, vision systems, and feedback mechanisms enable these machines to detect minute irregularities in the workpiece and make necessary adjustments during the chamfering process. This results in superior-quality finished products and reduces material waste.

Advanced Material Handling
Efficient material handling is crucial for optimizing production processes. Future chamfering machines are being equipped with advanced material handling systems, including robotic arms and conveyors, to ensure smooth and seamless material flow. These systems can handle different shapes and sizes of workpieces, further enhancing the versatility of chamfering machines.
Eco-Friendly Chamfering Machines
Sustainability is a growing concern in the manufacturing industry. Manufacturers are increasingly adopting eco-friendly practices, and chamfering machines are following suit. Future chamfering machines are designed to minimize energy consumption, reduce emissions, and optimize the use of cutting fluids and lubricants. This not only helps in conserving resources but also ensures a safer and healthier working environment.
Compact and Portable Designs
Flexibility and mobility are becoming essential requirements in modern manufacturing setups. Chamfering machines are being developed with compact and portable designs, allowing them to be easily moved and integrated into different production lines. These portable machines offer greater convenience and versatility, especially in industries where space is limited.
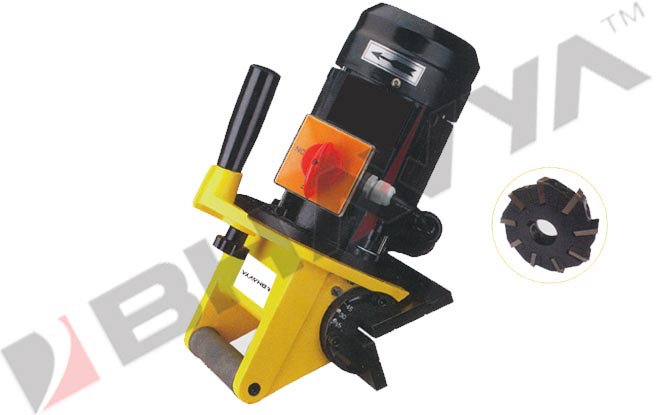
Remote Monitoring and Control
With the advent of Internet of Things (IoT) technology, chamfering machines can now be remotely monitored and controlled. Manufacturers can access real-time data, monitor machine performance, and adjust from anywhere using connected devices. This enables proactive maintenance, reduces downtime, and improves overall operational efficiency.
Improved Safety Features
Safety is a paramount concern in manufacturing environments. Future chamfering machines are equipped with advanced safety features to protect operators and prevent accidents. These features include safety shields, emergency stop buttons, automatic tool detection, and comprehensive safety protocols. By prioritizing safety, chamfering machines ensure a secure working environment for all personnel involved.
Cost-Effective Solutions
Cost-effectiveness is a key factor for manufacturers when investing in new technology. Future chamfering machines are designed to provide cost-effective solutions by optimizing resource utilization, reducing maintenance requirements, and improving production efficiency. Manufacturers can achieve higher productivity while minimizing operational costs, leading to better profitability.
Integration with IoT
Chamfering machines are embracing the principles of Industry 4.0, which emphasizes the integration of digital technologies for intelligent manufacturing. By connecting chamfering machines to the Internet of Things (IoT), manufacturers can achieve seamless data exchange, real-time analytics, predictive maintenance, and synchronized production processes. This integration enhances overall productivity, flexibility, and agility in the manufacturing environment.
Application-Specific Chamfering
Different industries have unique chamfering requirements. Future chamfering machines are being developed with customizable features to cater to specific applications. Whether it’s automotive, aerospace, furniture, or any other industry, chamfering machines can be tailored to meet the precise needs of the sector. This customization ensures optimal performance and maximizes efficiency for specific manufacturing processes.
User-Friendly Interfaces
To facilitate ease of use and enhance operator productivity, future chamfering machines feature user-friendly interfaces. Intuitive touchscreens, graphical displays, and interactive controls make it easier for operators to set parameters, monitor operations, and adjust as needed. User-friendly interfaces reduce the learning curve and enable operators to maximize the capabilities of chamfering machines effectively.