Machinery for Wood Work
Machining wood work piece boards to obtain straight, angular, and many more shapes with accuracy requires the support of appropriate tools. With the advent of AutoCAD and relative software machineries are designed in innovative ways to obtain workshop equipments with ease.
Production of Fashionable Wooden Components
Wood works are preferably done in furniture and construction industries. As people expect convenient and flexible option in furniture, more complicated and innovate wooden furniture are made and wood work instruments stay very supportive to obtain wood work piece into the desired shapes, curves, angles and in different dimensions.

Innovative Equipments to Produce Complicated Designs in Wood
Woodworking tools are available with versatile mechanisms. There are many devices that can be illustrated to handle complicated machining with wood work piece. Surface planner modular, chain mortise, bandsaw device, bench grinder and many more equipments are designed by manufacturer.
Wood working machinery for furniture making purpose
Jig saw for coarse machining process with wood work piece, double auto mould to work on two sides simultaneously and for making angular moulds, auto mould for efficient moulding operation, chisel mortise for drilling operations, router device to make grooves, and many more options are available to continue with furniture designing.
The One Stop Destination to find Wide Range of woodworking machinery
We supplied workshop equipments to support machining operations on different work piece materials. They have plethora of woodworking machines made from high quality metals and supply to different parts of the world with complete customer support.
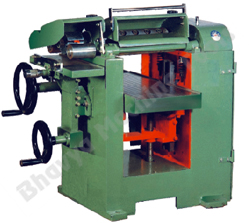
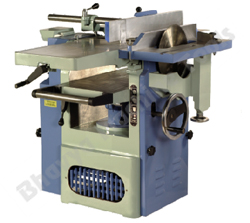
Pioneering Wood Machining Tools Supplied
We supply equipments for specific and multiple machining purposes. They have specific devices to carry out exclusive machining options such as thickness planer with auto mould, surface planer with circular saw attachment, tilting arbour spindle moulder, chisel mortise and many more.
Machinery to Produce Wooden Boards of Overall Precise Thickness
We offers Thickness Planer with auto mould, a compatible equipment to make wooden boards with precise thickness. This device is customized with either 2 or 3 planer blades and auto mould system to keep the wood work accurate.
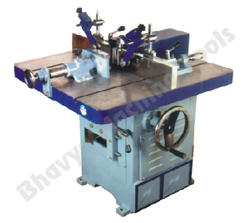
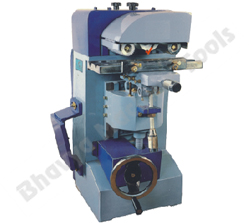
Machinery for Economic Mortising Jobs
Mortising jobs play significant role in many wood works. Though machining options are available for easy mortising, yet, wastage, precision and expense features remain challenging for moderate and huge production requirement.
Difference between Chisel and Chain Mortiser
Chain Mortiser economy model supplied by us stays perfect for precise cavity creating jobs and it supports the operator for easy operations. Chisel Mortiser is used for industrial drilling operations and it is supplied with standard components like drill chuck, 3 phase electric motor, etc that makes the equipment to come out with enhanced performance.
Machinery to Form Grooves in Wood Piece
Roture machine is a versatile option applied to cut grooves. A high speed router stays effective to complete bulk work. Similarly, router can also be preferred to obtain different patterns in wood work pieces.
Supportive Machinery for Workshop Activity in Furniture Industry
We offers wide range of supportive device for wood works such as edge trimmer for trimming operations, edge bander for banding process, multi boring to drill multiple heads, post forming for protecting the wood surface of the furniture, dust collector to collect the granules of wood and stays supportive for overall maintenance.
Conclusion
Wood works especially furniture making is a creative job and finding a machinery to support work word will be a reliable option to experience precise productivity.