Category Archives: Machine Tools
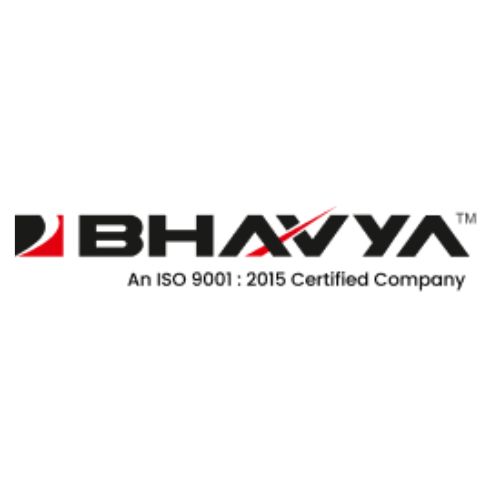
Exploring the Import Market of Machine Tools in UAE
The UAE continues to strengthen its role as a leading industrial and trade hub in the Middle East. With significant investment in infrastructure, manufacturing and engineering, the demand for precision equipment is consistently rising. A key component of this industrial…
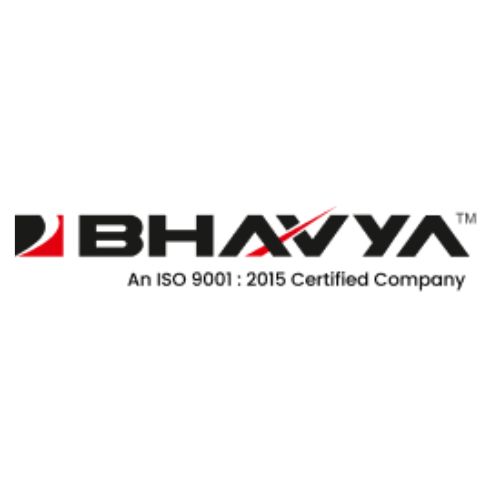
The Machine Tools Industry in Oman
The machine tools industry in Oman is gaining traction in the market. Several factors are contributing to this. Some of the issues that have been identified include skilled workers in the industry, the high cost of labour, and the speedy…
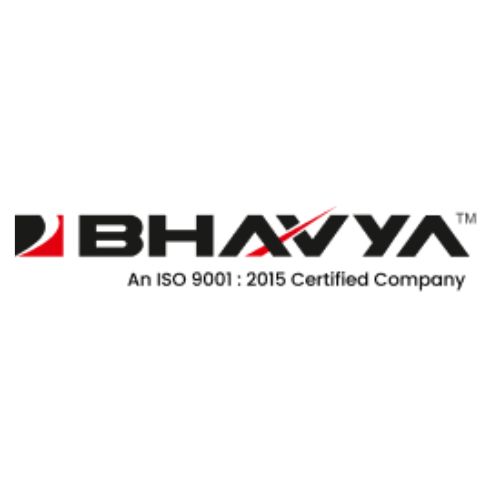
FDI in the Machine Tools Industry in Qatar
FDI in Machine Tools Industry in Qatar has been impacted by various microeconomic factors. One of the main microeconomic factors that are affecting the market is the increase in the cost of raw materials and labour cost. In addition, one…
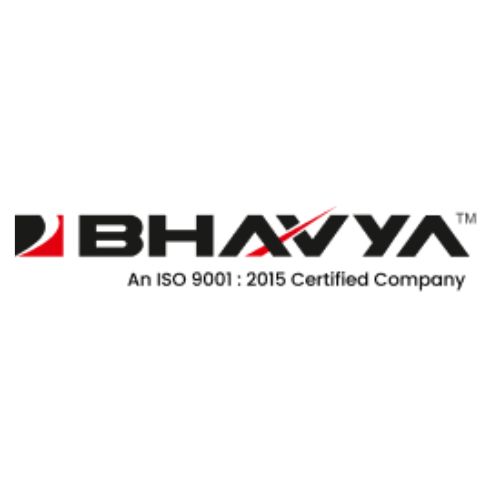
The Machine Tools Industry in Bahrain
Currently, the Machine Tools industry in Bahrain is dominated by the Automotive segment and the Metal cutting segment. According to the reliable sources, the Metal cutting segment is expected to grow at the highest CAGR during the forecast period. The…
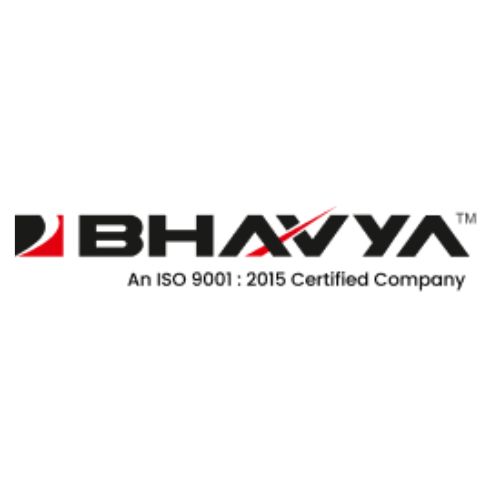
Machine Tools Market in Latin America
The machine tool for working metal exports in Latin America reached millions in 2022. These exports experienced steady but slow growth during the period between 2020 and 2022. Brazil was the largest exporter of machine tools in Latin America, accounting…
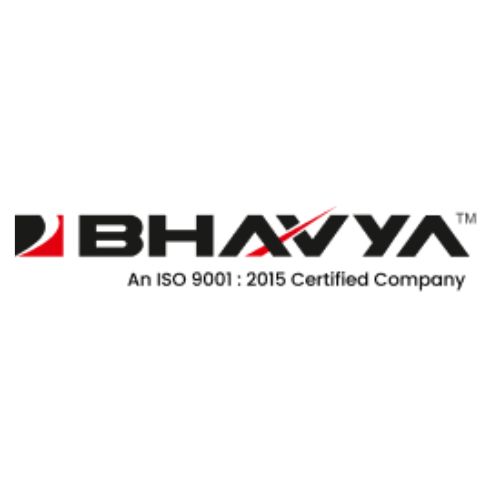
Coronavirus Pandemic Implications on the Global Machine Tools Market
The coronavirus outbreak has created several challenges for many industries and businesses around the world. A majority of the leading countries of the world have been forced to take strict actions like complete lockdown to prevent the coronavirus disease to…
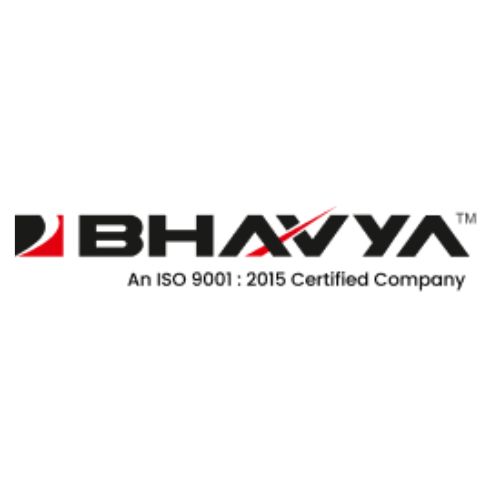
Air Compressor Technology That Has Delivered Efficiency in Manufacturing
When your air compressor is unreliable, then your business will suffer due to recurring inefficiencies in the equipment and downtimes. It is always advisable to invest in high quality and energy efficient air compressors for the various industrial applications that…
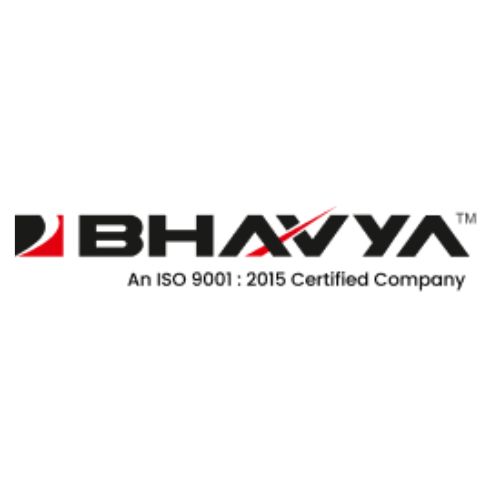
Innovations in Machine Tools that has Changed Global Production
It is said that few organizations can prosper without innovation. This has been very profound in the field of machine tools which has gone in leaps and bounds through innovation leading to tremendous improvements in the production capacity and overall…
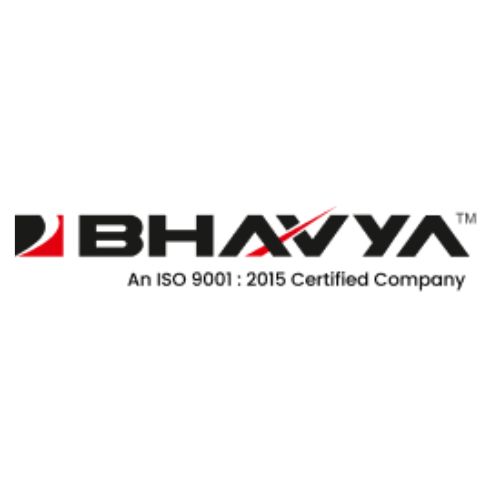
Machine Tools – Journey from Mechanical to Electronics and Beyond
In the history of machines, the range of evolution is something beyond our imagination. Whenever something new technologies come to the market, users can get something better and smarter than the previous versions of the machine. Change is the only…
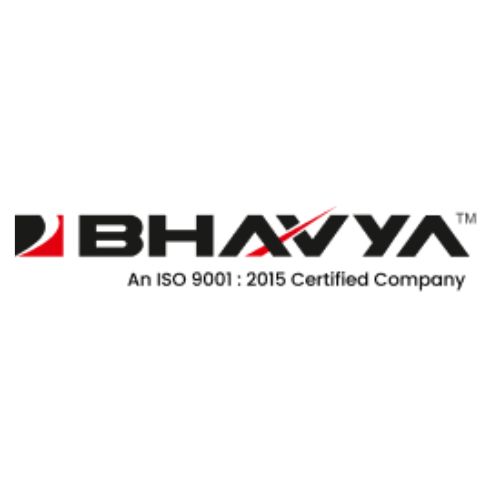
The Checklists While Dealing with Online Machine Shop
Online shopping is a great alternative to regular walk in shopping for various reasons. Listed here is a list of the many advantages of using the online Bhavya machine shop to buy quality machine tools for your organization. The Quality…
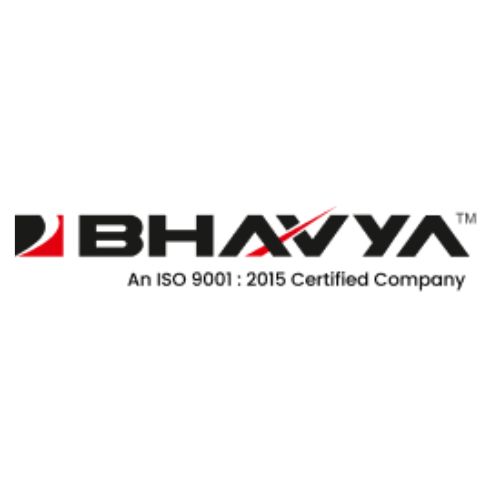
How Industrial Efficiency and Bulk Productivity can be Achieved?
Research and development has led to the availability of many new and better products across many industries throughout the world. This has resulted in designing and producing a vast range of innovative machinery including tool room units for the local…
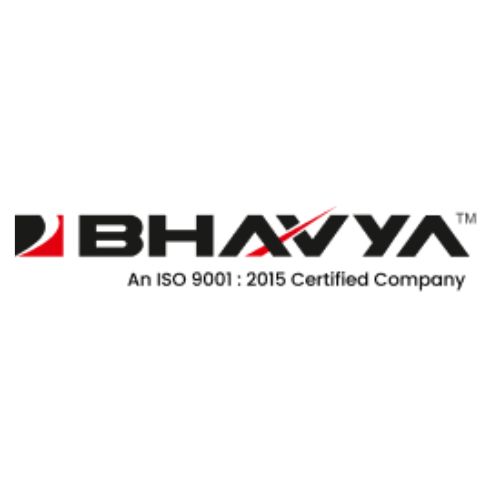
5 Important Revisions in Traditional set up of Press
Traditional Press Setup Traditional press brake setup was found to be with hydraulic principle and the usage can be traced back to ancient Mesopotamia and Egypt. Later as years went on Greeks introduced some changes into the provisions considering suitability…
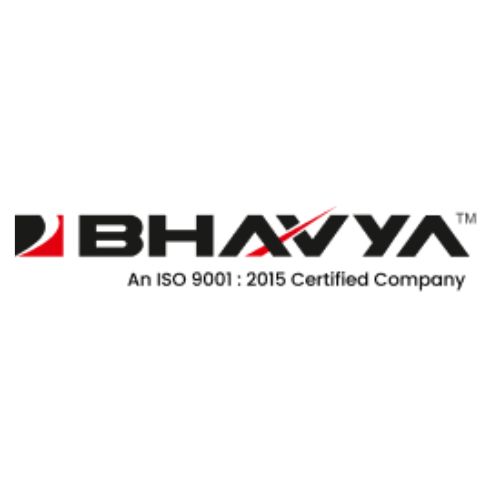
DMTG Promotional Offers at Bhavya Machine Tools
We proudly presents you the second season of preferential promotion offer in association with Dalian Machine Tools Group. This offer is an exclusive one to celebrate DMTG 10th Anniversary Promotion. We bring you the following turning device from DMTG Cl-15/250,…
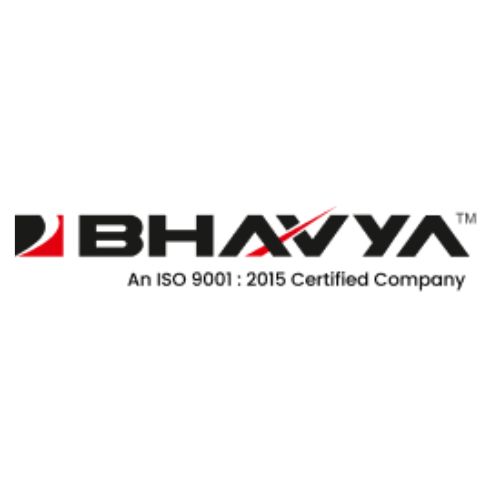
Bhavya Machine Tools Presents DMTG Milling Machines
We bring you with exciting offers in machinery. We, in association with Dalian Machine Tools Group provide promotional offers for the two VMC models VDF-850 with CNC Fanuc 0I-mate MD and VDL-1000 with CNC Fanuc 0i-mate MD and Fanuc 0i…
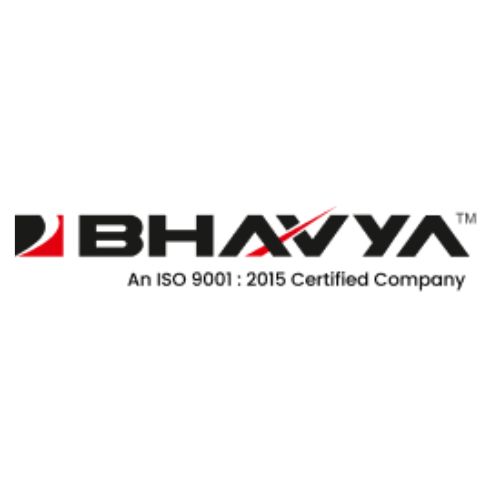
The Vertical Machine Center – Advanced Milling Techniques that Deliver High Quality Workmanship
Milling requirements have been changing in accordance with the industrial requisites. There are innovations made in milling specifications and vertical center is one among them that is suitable to obtain rigid and flexible milling in fragile work materials. Development of…
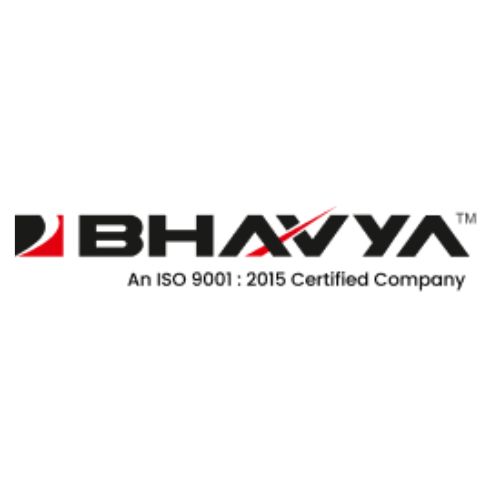
India is Growing as Global Hub in the field of Manufacturing Machine Tools
Machine tools manufacturing Industry is a very planned and important industry today. Indian manufacturing industry has grown many fold be it automobiles, aerospace, defense, electric machinery. For a country to progress, to become influential it must progress in technology. Today…
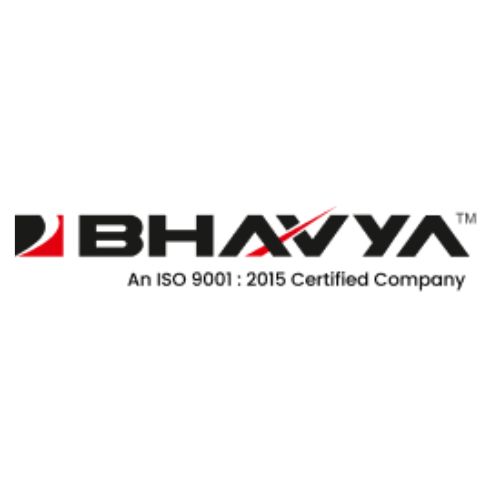
Why do Moderate Construction Projects Deserve Mobile Concrete Mixture?
Modern Construction Industry and Construction Equipments Construction process includes variety of activities hence, time consumption is quite long. To make the work proceed faster unlike conventional activities, several friendly equipments have been introduced by machinery industries. The Advent of Concrete…
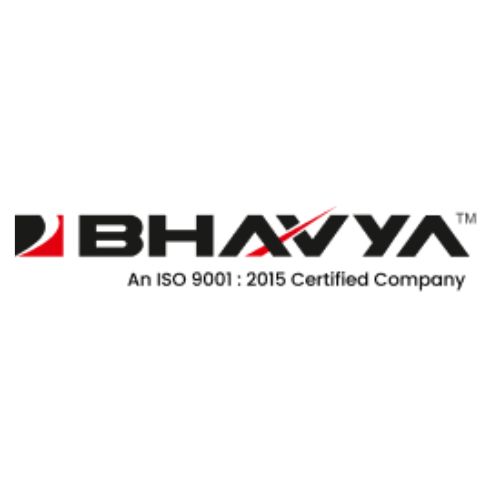
How to Choose Power Tools that Saves Core Machining Expense and Maintenance Costs Considerably?
Usability of Power Tools in Drilling and Welding Process Power tools are machinery components that can work with extra source of energy and they are the reliable choice for small to moderate core machining operations. Significance of Power Tools These…
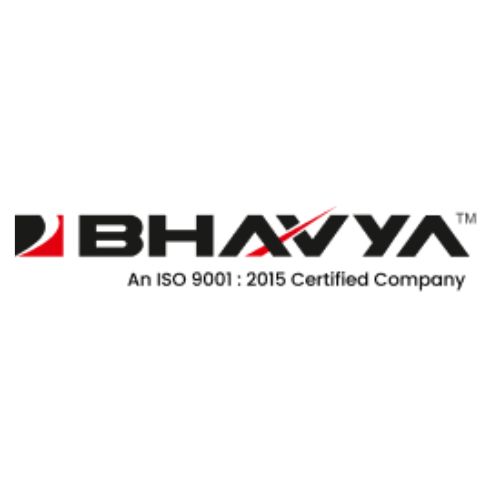
Safety Norms to be Followed while Applying Slab Trolley with Rails and Tower Hoist
Construction Made Easy with Innovative Mechanisms Apart from Concrete mixer, batch plant, weight batcher, there are special equipments available today to make the construction work faster. These equipments are suitable to handle heavy or big level of construction projects. Machines…
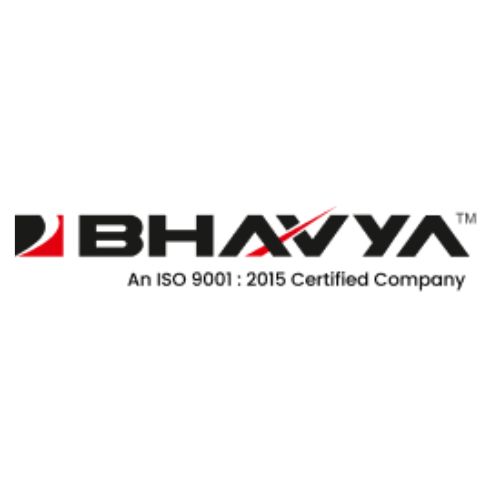
How can You Find & Buy Your Required Machine Tools Online?
Machine Tool Search is not limited to Local Area/Local Market-Machine Tools Global Market Machine tools are used for a wide range of uses such as shaping, cutting and grinding metal in workshops. They therefore have a wide application in the manufacturing…
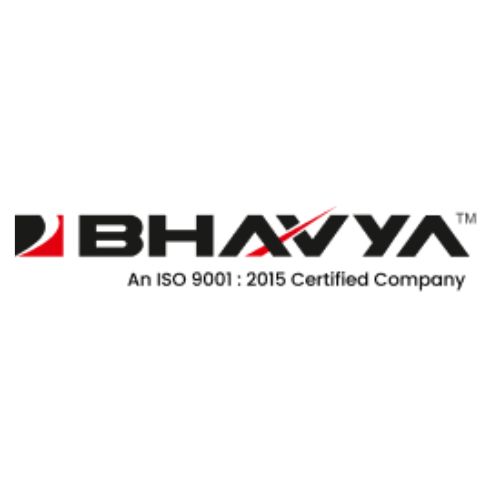
Right way of Setting up Your Workshop with Machine Tools
Setting up your own workshop with tools can be time consuming and it involves big money. But when you have a workshop set up according to your requirements it makes working more enjoyable. To set up your workshop you need…
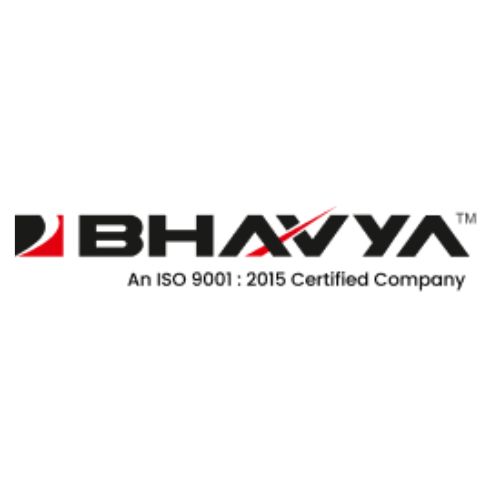
Benefits of Buying Machine Tools from Indian Manufacturers
The machine tool industry is regarded as the backbone of any industrial economy. It is basically the source through which a broad variety of industrial products and consumer goods are manufactured. India is a developing nation with a rising economy,…
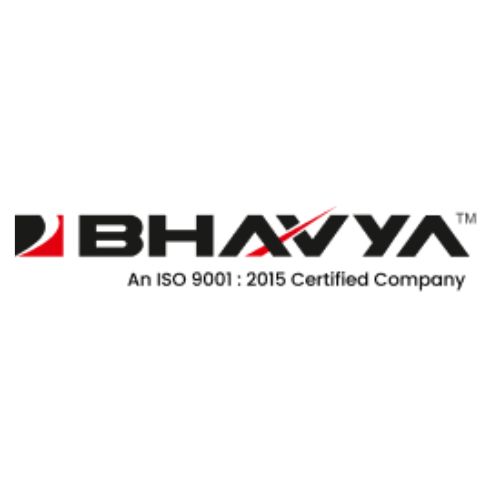
5 Most Important Machine Tools For Any Workshop [INFOGRAPH]
Nowadays, several types of workshop machine tools are manufactured in many countries around the globe. These tools are commonly used for different purposes in a wide range of industrial segments such as woodworking, automobile, electrical, construction, etc. This infograph give…
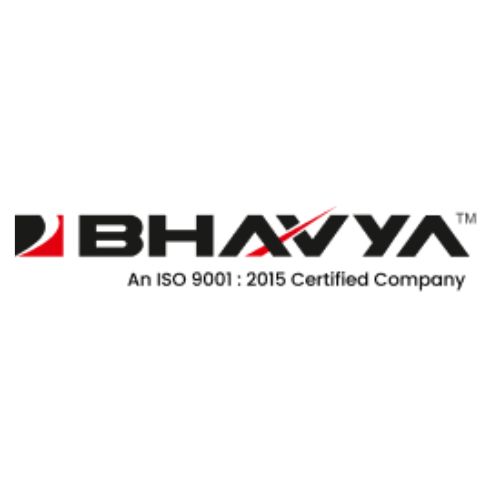
Rising Challenges & Opportunities for Power Press Manufacturers in India
The power press is a powerful sheet metal machine. It is mainly used for cutting, bending, pressing, forming and stamping sheet metal into different shapes and sizes. This highly precise and versatile machine deforms and cuts metal by pressing it…
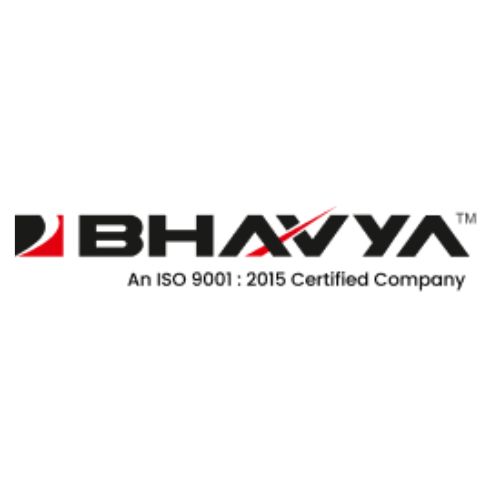
Rising Demand of Woodworking Machineries Across the World
Woodworking machines are highly popular and widely used equipments. They are basically utilized for performing various processes on wood, such as cutting, carving, drilling, finishing, grinding, joining, molding, sawing, sanding, shaping, etc. It help to avoid manual labor and the conventional…
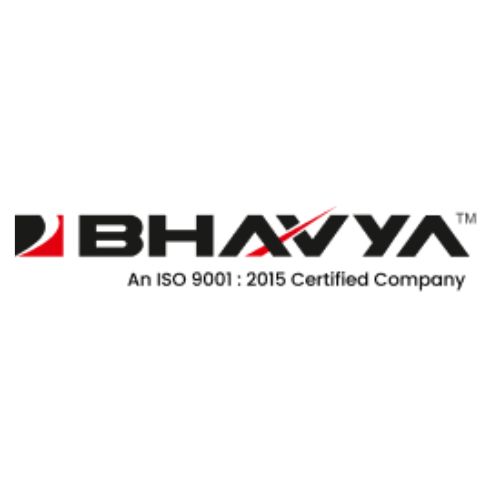
Sheet Metal Machineries for Shearing, Bending & Cutting
The various sheet metal machineries for shearing, bending and cutting are described below: Press Brake The mechanical press brake has a sturdy frame built from high grade steel. It also consists of steel plates with appropriate thickness and machined guide…
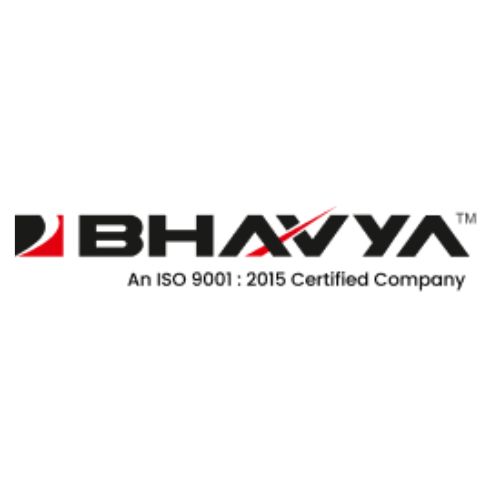
Industrial Applications of Different Sheet Metal Machineries
Metals play an important part in our lives today. Think of any object around us and either it is made of metal or some part of it is of metal. Metals are an integral part of our lives today. A…
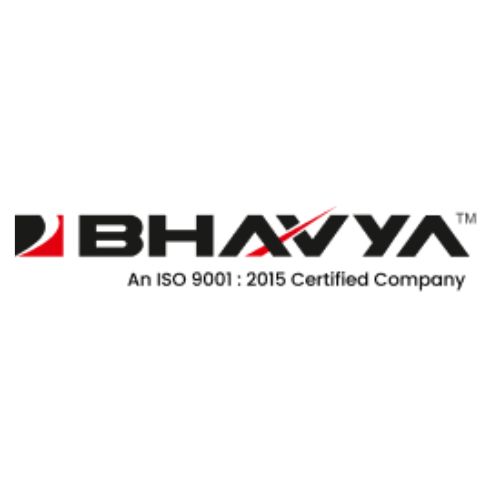
Woodworking Machinery – Efficient Solution for Wood Shaping Applications
Woodworking machinery or tools are used to cut, carve or shape wood. A tool with a motor reduces the work of the operator and increases the production. In a wood processing business these are craft the desired shape or dimensions from…
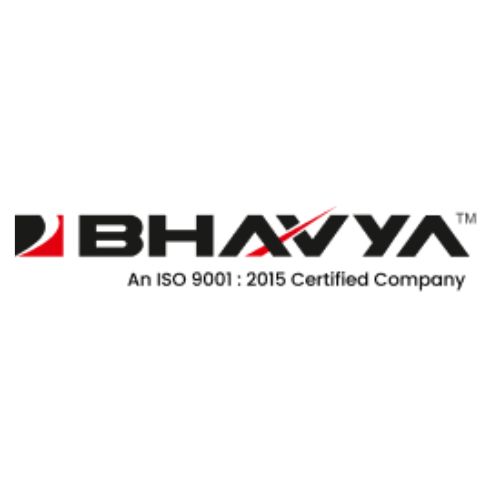
Significance of a Press Brake in Metal Cutting Applications
A number of machines are used in the process of fabrication of sheet metal parts. Fabrication is the process of collective operations which are used to give a shape to the metal sheet. This involves a number of equipments like…
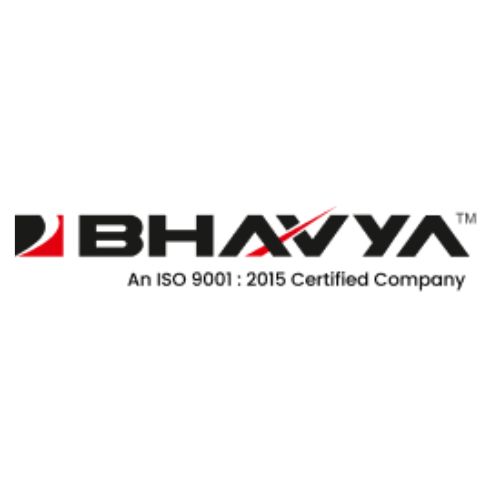
Facts About a Surface Grinding Machine
To give a meticulous smooth finish to the surface, as regards the level, size or finish of the surface of a flat metallic or non-metallic object, surface grinding tools are used. In order to make the surface flat and smooth…
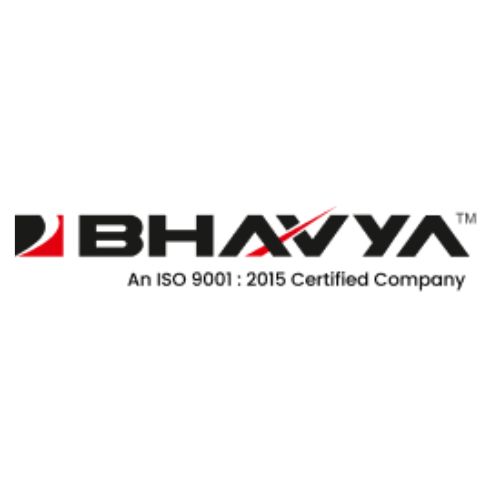
Applications of a Horizontal Bandsaw Machine
A machine that is used for cutting wood, metal, plastic and a variety of materials into straight, curved or irregular shapes is called a horizontal bandsaw. A wide range of bandsaw equipments are available in the market. They are made from cast…
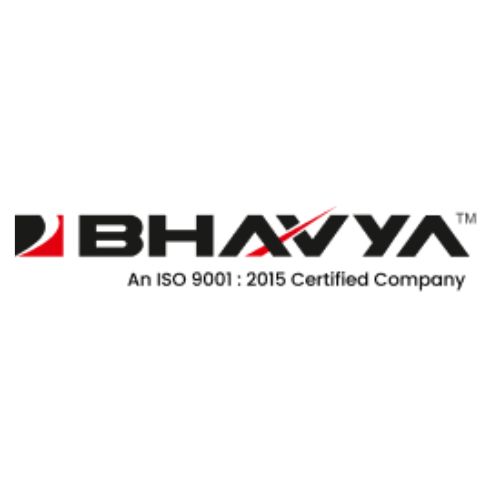
Press Brake, Slotting Machine – Machines used for Bending and Cutting Metals
Press Brake, Slotting Machine – It used for Bending and Cutting Metals Cutting and bending are the two primary functions performed on metals for casting the desired shape or dimensions. Therefore when it comes to metal working, the two most…
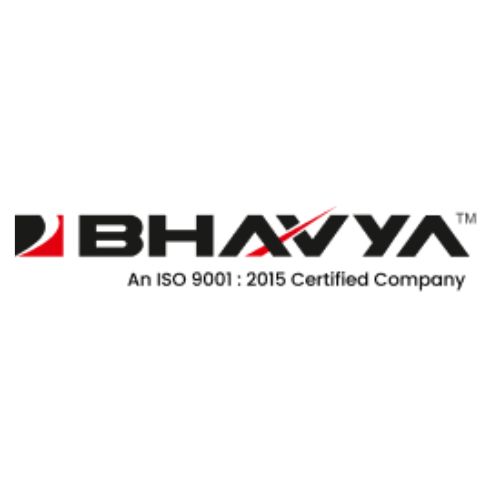
Guide to Various Kinds of Sheet Metal Machines Used in Workshops
Sheet metal machines are primarily utilized for cutting, shaping, pressing, and forming metal sheets into specific shapes and dimensions. Nowadays a number of sheet metal are available in the market. The various kinds of tools used in workshops are as…
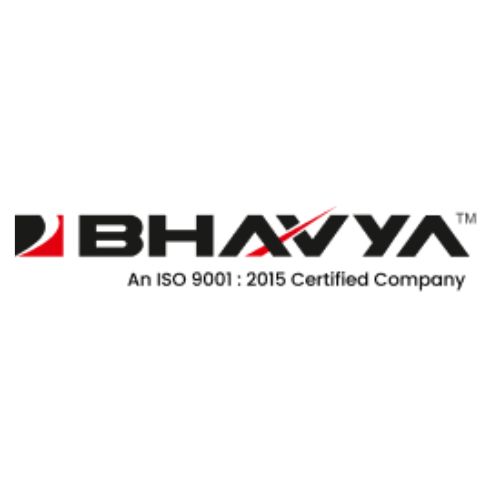
Types of Workshop Machinery – Milling, Grinding, Shaping Machines
Types of Workshop Machinery – Milling, Grinding, Shaping Machines Machine play a very important role in a workshop where metal working or woodworking tasks are performed. They enable speed process in the workshops and enhance the accuracy and efficiency of…
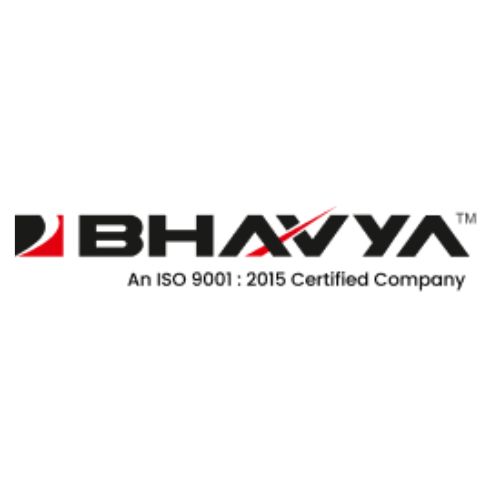
How to Use a Grinding Machine Safely?
The grinding machine is utilized in a tool shop for various purposes such as finishing, forming, sharpening, cutting, roughing, snagging, cleaning, polishing, buffing, etc. However, while operating a grinding device, it may cause serious injuries to the operator or any…
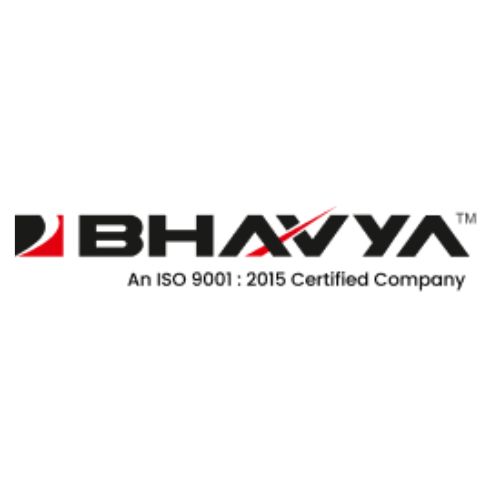
Features to Look for While Selecting a Bandsaw Machine
The bandsaw machine is one of the most essential tools widely used for woodworking, metalworking and cutting a variety of materials into straight, curved and irregular shapes. Nowadays, a wide range of bandsaw equipments are available in the market. They are built…
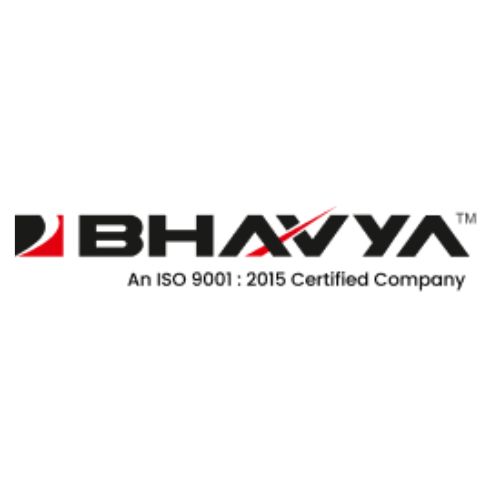
All You Should Know About Machine Tools
A machine tool which is used for machining or shaping metal or any other solid material, by various methods such as cutting, grinding, milling, shearing, boring; or other suitable ways of deforming the related work piece. All unit generally use a…
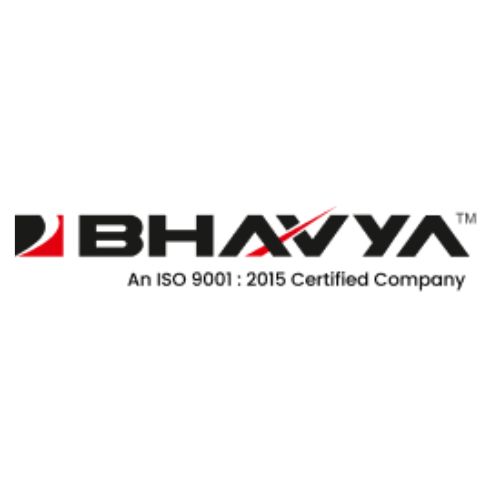
The Most Important Machine Tools Required in Any Workshop
The most important tools required in any workshop, nowadays are described below. Milling Machines The milling machine is used for milling, cutting, shaping, carving, planing, contouring, drilling, stamping, and die-sinking a variety of solid materials. The work piece is positioned, to…
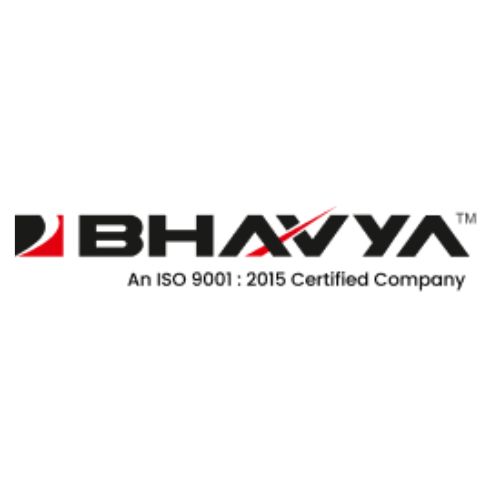
Range of Turret Milling Machine for Machining Solid Objects in Workshop
The constant development in technology and the introduction of modern machines; helps us to produce better products, optimize costs and increase productivity. All industrial units utilize a variety of machine tools; that typically include the milling machine. It is one…
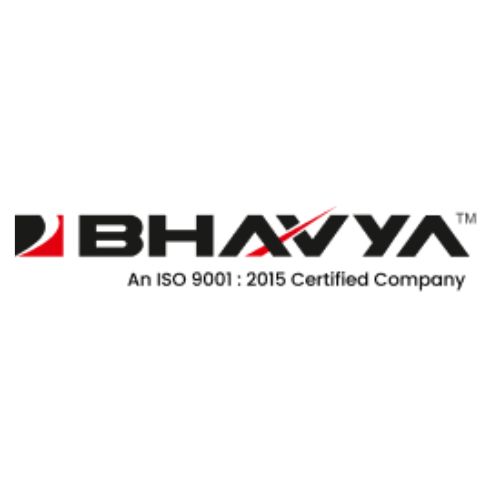
Lathe Machine Operations
Nowadays, the tool room work and workshop machine activities; are done by repairers or through suitable lathe tools. A lathe is a tool utilized to perform various functions like turning, cutting, drilling, grooving, knurling, parting, threading etc. They are used to produce accurate products made from…
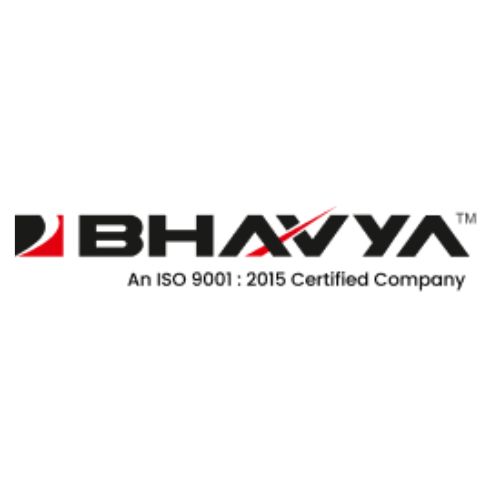
Bhavya Machine Tools Delivers Lathe Machines for Industries and Institutes across India
Lathe machine is wonderful equipment used to shape objects with symmetrical physical properties about the axis of rotation. Various actions like cutting, knurling, sanding, drilling or deformation can be easily and quickly performed on a work piece using a modern…
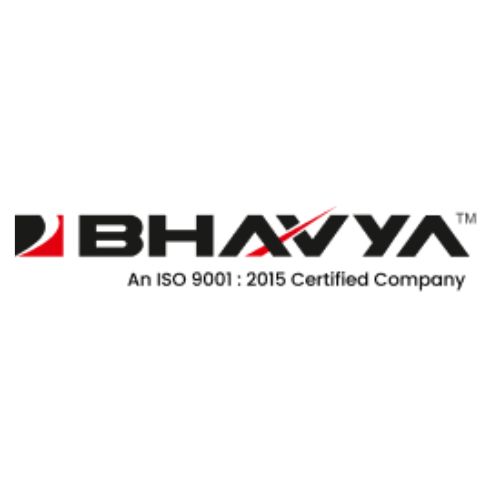
Bhavya Machine Tools Introduces 165mm and 175mm Light Duty Lathe Machines
Lathe machines are the most efficient tools for handling jobs of cutting, shaping and fabricating metals. We introduces a multipurpose light duty lathe which can easily and efficiently handle wide range of applications in a workshop or industry including production…
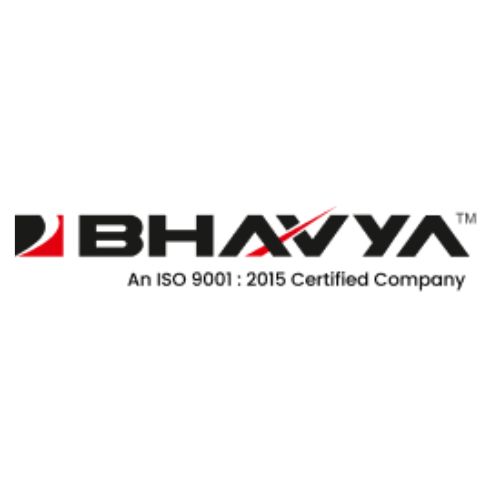
History of Milling Machine
Rotary filling was the first in base of invention of the first milling machine that reduced the efforts need to put on hand filling and save the time. The development history is still unclear as the variety of custom machines…
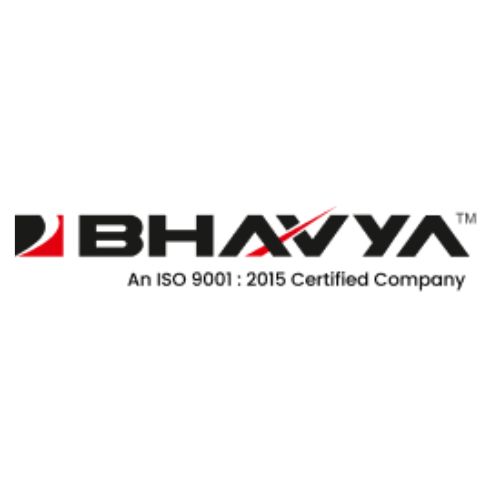
All About Slotting Machine
A slotting machine is a machine which is used to slot materials made of metal and wood. It can make slots on heads of screws, bolts and other automobile components as well as other similar parts. The main purpose of…
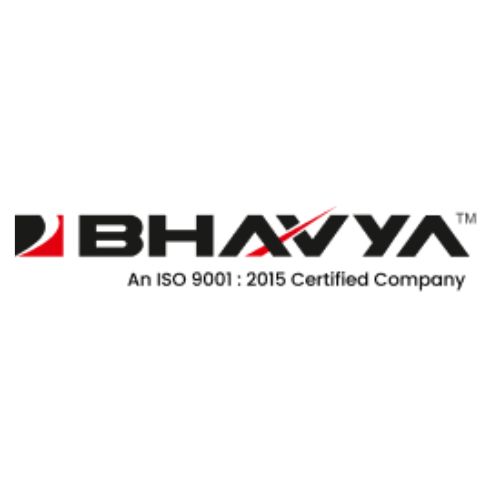
Machine Tools – Grinding Machine
Machine tools are used for various processing work on different metals. Machining works like cutting, grinding, shaping machine to shape the metal workpiece, boring, slotting on metal through slotting machine, shearing and others are carried out by mechanical and electronic…
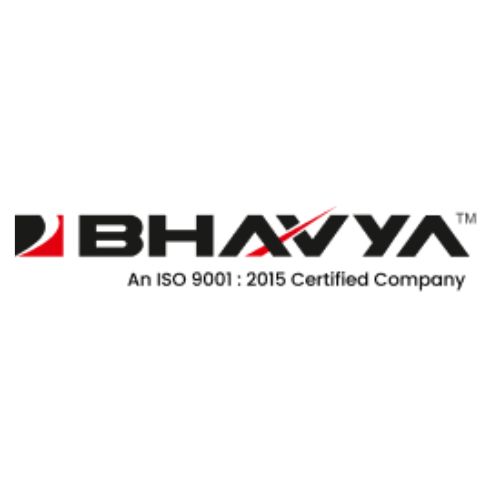
Tool Room – Types of Tool Room Machines, Toolroom Setup
Tool room Tool room is the room where the tools are kept for storage, prepare, repairing and machining. The space area can be varied based on the types of the tool room machines and applications. It may include high end…
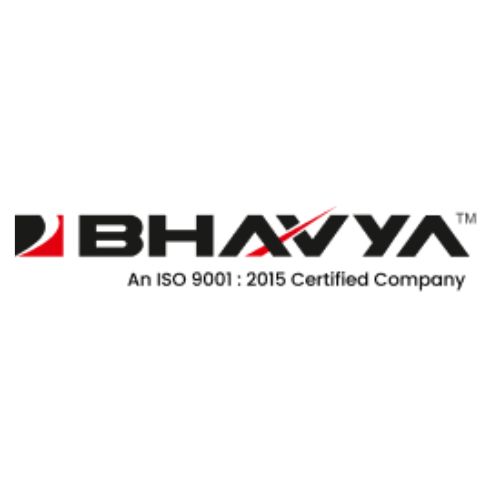
How to Select Power Press for Metal Forming Applications?
Press machines or press brakes are the most important metal shaping tools. With these one can easily bend, cut and form the shapes of various kinds of metals. Different kinds of press machines are available in the market today. There…
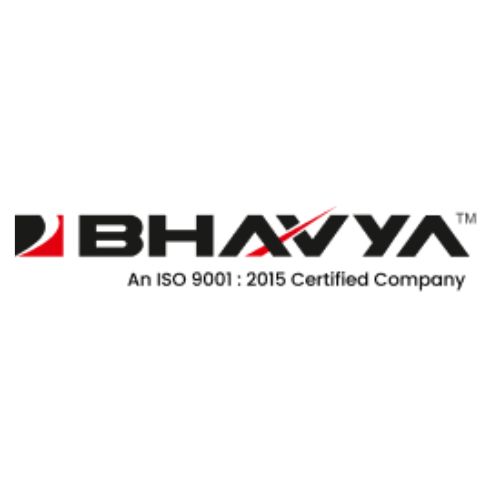
Metal Bending and Shaping Machines – Press Brake, Lathe Machine
Metal Bending and Shaping Machines – Press Brake, Lathe Machine Basically two types of equipments are widely used in metal forming industries. One is sheet bending and other is lathe. A sheet bending machine is the one that bends metal…
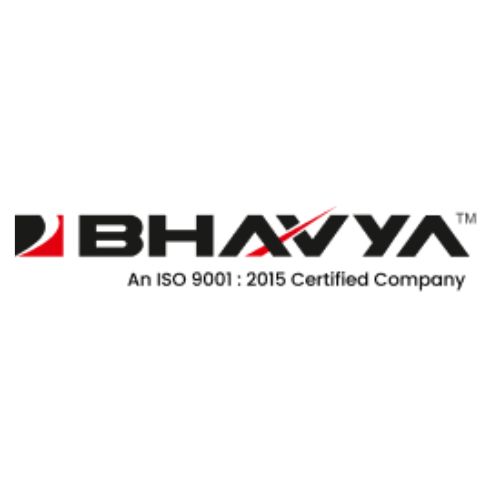
Types of Power Press, Applications of Power Press – C Type Power Press, Pillar Type Power Press
Power Press - C Type, Pillar Type It is used for bulk production from cold working of ductile materials like mild steel with rotating flywheel acting as energy storehouse to operate ram to impact on the workpiece. It is used…
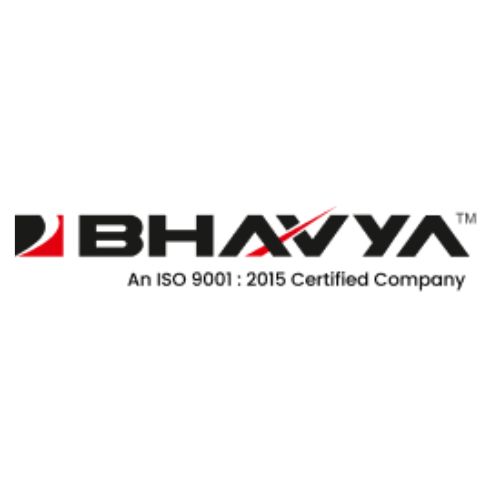
C Type Power Press, Pillar Type Power Press, Safety Measures for Power Press Operation
Power Press – C Type Power Press, Pillar Type Power Press Power presses are powered equipment used to stamp, cut or form materials by the use of dies (or tools). They include equipment known as "croppers" or "metal workers". These…